Maintaining the integrity and safety of hazardous substances often starts with the selection of the right storage solution. One critical component in industries such as chemical manufacturing, agriculture, or pharmaceutical production is the acid storage tank. Understanding the complexities and considerations involved in choosing and maintaining these tanks is essential for operations reliant on the safe handling of corrosive materials.
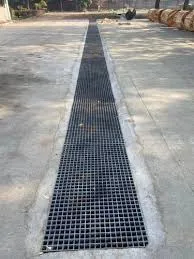
When it comes to acid storage tanks, material selection is a primary concern. These tanks are often constructed from materials like fiberglass-reinforced plastic (FRP), stainless steel, or high-density polyethylene (HDPE). Each material offers different benefits and challenges. FRP, for instance, is valued for its excellent corrosion resistance and durability.
It is an ideal choice for storing aggressive acids such as hydrochloric acid. Stainless steel, particularly grades like 316L, is another popular option thanks to its robustness and resistance against specific corrosive agents. However, the suitability of stainless steel can vary depending on the acid concentration and temperature. HDPE tanks, although more budget-friendly, are typically used for less volatile acids due to their limited temperature tolerance.
Once the appropriate material is chosen, understanding the engineering specifications is crucial. This involves calculating the tank's capacity needs, including potential expansion for future storage requirements. An expert approach considers factors such as the chemical compatibility of the tank's components, the structural integrity required to withstand pressure variations, and compliance with relevant industry standards and regulations.

An essential aspect that bolsters trust and reliability in manufacturing environments is the incorporation of safety and monitoring systems in acid storage tanks. Modern tanks are often equipped with real-time monitoring technologies that measure internal temperature, pressure, and pH levels. Having integrated alert mechanisms helps avert potential failures by informing operators of any deviations from normal operation ranges, thus ensuring preventive maintenance can be conducted promptly.
acid storage tank
Furthermore, the expertise in installation and maintenance of these tanks cannot be overstated. Proper installation not only involves the physical setup but also includes ensuring adequate ventilation, spill containment measures, and precise calibration of monitoring systems. Regular maintenance by trained professionals, who have deep knowledge of the specific acids in use, is paramount to extend the lifespan of the tank and prevent costly leaks or contamination incidents.
Selecting and utilizing acid storage tanks demand not only a deep understanding of the materials but also a robust framework for ongoing assessment and maintenance. Suppliers with a proven track record of providing reliable storage solutions and after-sales service become invaluable partners. Their experience in tailoring tanks to meet specific industrial needs greatly enhances operational safety and efficiency.
In conclusion, the effective management of acid storage is not only about acquiring a high-quality tank but embracing a holistic approach. This includes strategic planning, deployment of advanced technologies for monitoring, regular maintenance, and ensuring compliance with safety regulations. Industries that prioritize these aspects benefit from enhanced safety, reduced risk of environmental impact, and optimized operational procedures—ultimately driving forward a culture of trust and authority in handling hazardous substances.