In the dynamic and evolving world of composite materials, the use of chemical products in Fiber Reinforced Plastics (FRP) applications stands out as a field rich with innovation and practical utility. This guide delves deep into how these chemical products enhance the quality, durability, and versatility of FRP, offering valuable insights from industry experts.
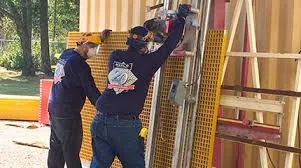
The core allure of FRP applications lies in their ability to combine strength with lightweight properties, making them ideal for a multitude of industries from automotive to aerospace, and even construction. The backbone of this transformative capability is intrinsically linked to the chemical products used in their fabrication. Typically, the main chemical components in FRP include resins, curing agents, and various additives each pivotal in determining the final qualities of the composite.
Resins, predominantly epoxy, vinyl ester, and polyester, serve as the matrix in FRP composites. Each resin type offers distinct advantages. For instance, epoxy resins are renowned for their exceptional mechanical properties and excellent adhesion. Industry experts frequently underscore their superior resistance to environmental degradation, making them a top choice in critical applications such as aerospace and wind energy. Vinyl ester resins provide a middle ground with their exceptional toughness and resistance to water absorption, making them ideal for marine applications and chemical storage tanks. Meanwhile, polyester resins, being more economical, are often used in automotive parts where cost efficiency is vital.
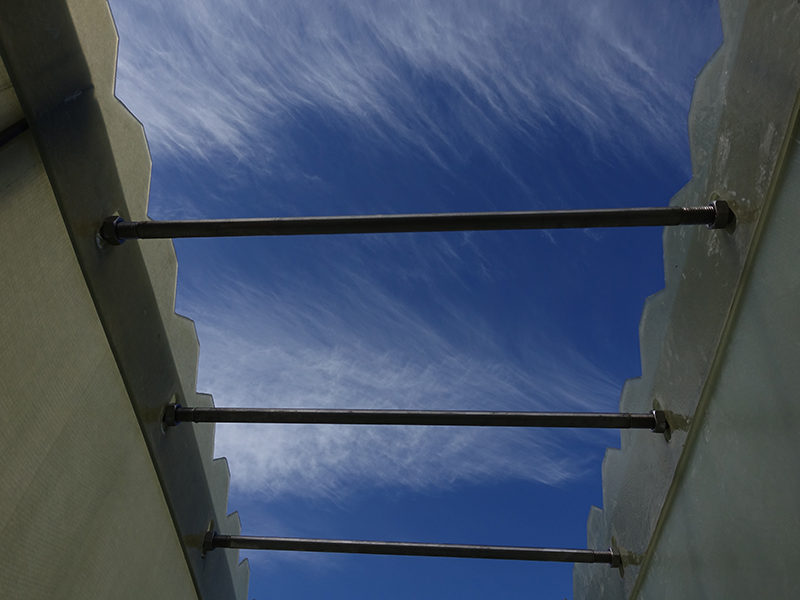
The role of curing agents cannot be overstated in the FRP manufacturing process. These chemical products accelerate the resin’s transformation from liquid to solid, influencing the strength and temperature resistance of the final product. Amines and anhydrides are commonly used curing agents, with amine-cured epoxies being highly valued for their rapid curing properties and excellent thermal stability, a crucial factor in high-temperature industrial applications.
Beyond resins and curing agents, a wealth of additives are employed to further customize the performance of FRP products. Flame retardants, UV stabilizers, and fillers enhance safety and durability, expanding the utility of FRP in environments that present challenging conditions. Flame retardants, such as halogenated compounds and phosphorous-based additives, are extensively used to comply with stringent safety standards in public transport and building materials. Industry specialists emphasize the importance of balancing fire resistance with mechanical integrity, achieved through a judicious selection of these additives.
chemical products for frp applications a comprehensive guide
The application of nanotechnology offers groundbreaking advancements within this field, with the introduction of nano-fillers like carbon nanotubes and nanoclays significantly boosting the mechanical properties and fracture toughness of FRP composites. Through the addition of these nanoscaled materials, designers and engineers can create FRP applications that meet ever-increasing performance demands. Real-life case studies and trials exhibit the striking improvement in impact resistance and flexibility brought about by these innovations, particularly in aggressive environments like oil and gas drilling.
Moreover, real-world application speaks volumes about the practical benefits brought about by these chemical products. Companies such as Hexcel Corporation have showcased remarkable success in utilizing newly developed epoxy resin systems for FRP composites used in automotive body panels. These systems not only enhance aesthetic appeal with superior surface finish but also contribute to vehicle weight reduction—an essential factor in meeting stringent emission regulations.
Trust in the quality and performance of chemical products used in FRP applications is fortified through compliance and adherence to rigorous industry standards such as ISO 9001 for quality management and ISO 14001 for environmental management. Ensuring such compliance garners customer confidence and fortifies the market position of suppliers and manufacturers in this competitive industry.
In sum,
the integration of specialized chemical products into FRP applications significantly optimizes their mechanical properties and performance. Drawing from the informed perspectives of industry leaders and empirical research, the future of FRP shines promisingly with ongoing advancements. The continual development of specialized resins, curing agents, and additives anticipates a future replete with applications that boast superior strength, durability, and environmental resistance—a testimony to the evolving science of FRP technology.