Navigating the expanding universe of chemical products for FRP (Fiber Reinforced Plastic) applications can be a challenging endeavor. FRP is widely recognized for its durability, lightweight nature, and resistance to corrosion, making it a prominent choice across various industries. Here’s an in-depth guide to understanding and selecting the right chemical products tailored for FRP applications, harnessing industry insights, extensive research, and authoritative expertise.
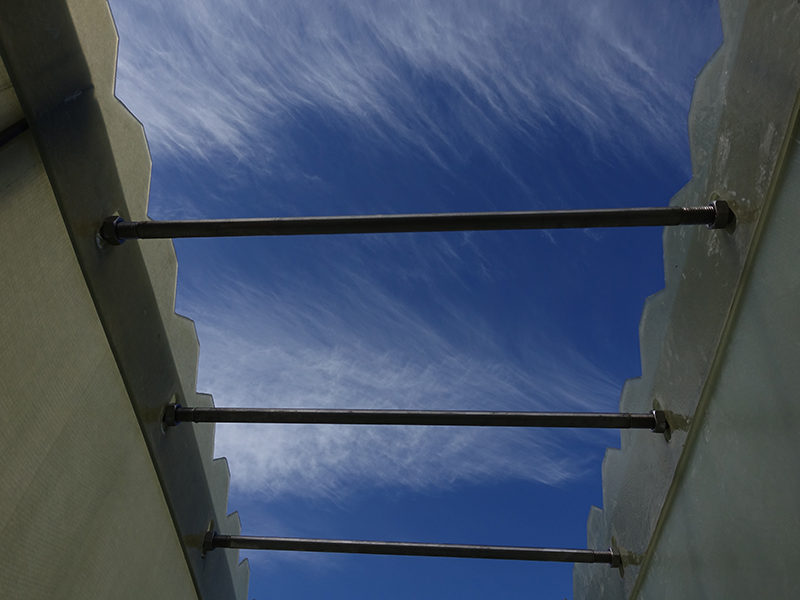
In the realm of FRP manufacturing, epoxy, polyester, and vinyl ester resins are the cornerstone chemicals. Each resin type features distinct properties dictating its application suitability. Epoxy resins are celebrated for their superior mechanical and thermal properties, making them ideal for aerospace and automotive industries, where performance under stress is paramount. In contrast, polyester resins provide a cost-effective solution with favorable resistance to environmental and chemical degradation, serving industries such as marine and building construction with efficiency and reliability. Vinyl ester resins bridge the gap between epoxy and polyester, offering enhanced thermal and chemical resistance, essential for applications requiring high durability in corrosive environments.
Your choice of resin significantly impacts the performance of the FRP product. Advanced formulations are continually evolving to enhance bonding strength, UV resistance, and processing efficiency. For instance, advancements in epoxy resins focus on reducing cure times without compromising strength, a critical factor for large-scale manufacturing.
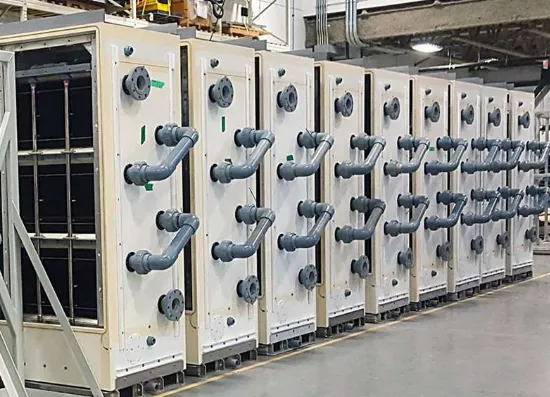
Catalysts and hardeners play an equally pivotal role in the FRP production process. Initiating the curing process, catalysts significantly influence the working time and stability of the resin. Methyl ethyl ketone peroxide (MEKP) is widely preferred for polyester resin systems due to its balance of effectiveness and economic cost. Meanwhile, amine-based hardeners for epoxy systems offer versatility, allowing customization of the curing schedule to adapt to various operational conditions. Innovations in catalyst development are revolutionizing FRP applications by offering faster curing times and improved final product properties without increasing toxicity or handling risks.
Additives, such as stabilizers, colorants, and flame retardants, cater to specific application requirements, optimizing the functionality and aesthetics of FRP products. Ultraviolet (UV) inhibitors enhance outdoor longevity by preventing degradation from solar exposure, fostering extended lifecycle and efficiency in applications like outdoor signage and marine vehicles. Adding pigments not only enhances aesthetic appeal but also provides coverage, reducing costs by minimizing the number of layers needed for desired opacity or color uniformity.
chemical products for frp applications a comprehensive guide
Surface treatments and coatings further complement these chemical products, ensuring the longevity and efficacy of FRP in demanding environments. Gel coats, often applied as an outermost layer, provide significant protection against environmental factors and mechanical wear. Innovative gel coat formulations focus on improving abrasion resistance and weathering performance, ensuring that FRP products maintain both appearance and functionality over time.
Compliance with industry standards and environmental regulations epitomizes the trust and credibility of chemical products for FRP applications. Adhering to ISO and ASTM standards guarantees that products meet essential safety and quality benchmarks, instilling confidence in their application. Additionally, the increasing focus on environmentally sustainable practices has propelled the development of eco-friendly resin formulations that reduce VOC emissions and incorporate renewable materials, catering to the growing demand for green manufacturing solutions.
In the dynamic landscape of FRP applications, collaboration with reputable suppliers and manufacturers is crucial. They provide invaluable experience and technical support, guiding the selection process and ensuring optimal integration of chemical components into fabrication processes. Transparent communication about the specific demands of a project ensures that the most appropriate chemical solutions are deployed, maximizing performance and economic efficiency.
In conclusion, selecting the right chemical products for FRP applications demands a nuanced understanding of resin types, catalytic systems, additives, and their interplay within specific application environments. By emphasizing expertise, authority, and trustworthiness, you ensure that each component enhances the cumulative properties of FRP, aligning with industrial needs for durable, efficient, and sustainable solutions. Staying abreast of innovations and regulatory developments further empowers industry stakeholders to drive forward with confidence, setting new benchmarks for quality and performance in FRP applications.