In the world of industrial and chemical engineering, the importance of a reliable chemical storage tank cannot be overstated. Organizations specializing in the handling and storage of hazardous materials recognize the critical role these tanks play in ensuring safety, regulatory compliance, and operational efficiency. This expertise, honed over years, underscores a deep understanding of the complexities involved in storing chemicals securely and efficiently.
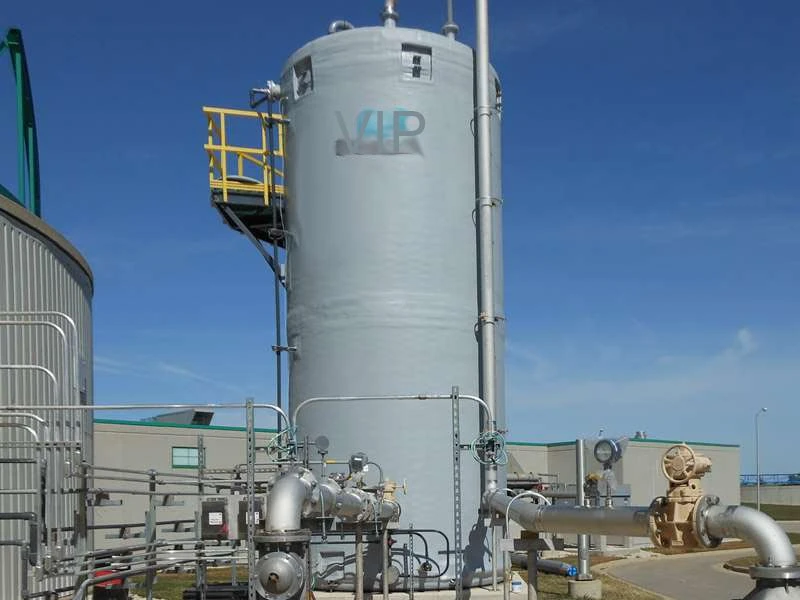
At the core of effective chemical storage is a meticulous consideration of material compatibility. Different chemicals react uniquely with various materials. For instance, polyethylene storage tanks are preferred for their resistance to a multitude of acids and caustic chemicals. Conversely, stainless steel tanks offer unparalleled durability for storing solvents, fuels, and high-temperature liquids. Companies must leverage their expertise to choose the appropriate tank material that aligns with the chemical properties and environmental conditions of their operational context.
Expertise in this field also involves an authoritative grasp of the regulatory framework governing chemical storage. The Occupational Safety and Health Administration (OSHA), Environmental Protection Agency (EPA), and other regional bodies put forth stringent guidelines for the design and maintenance of chemical storage systems. Dedication to compliance not only ensures the safety of personnel and the environment but also safeguards the company against potential legal repercussions and penalties.
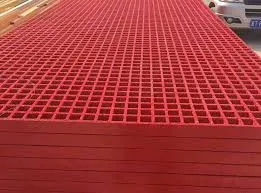
Designing a chemical storage system requires a synthesis of engineering acumen and practical experience. Engineers must consider factors such as temperature control, pressure management, and mixing requirements. Experience gleaned from past projects enables professionals to anticipate challenges unique to specific chemical interactions and storage conditions, thereby informing design choices that preclude operational disruptions.
chemical storage tank
Furthermore, the conversation on trustworthiness in chemical storage cannot be devoid of discussions on risk management. Effective risk assessment and mitigation strategies are cornerstone practices. By employing state-of-the-art sensors and monitoring systems, organizations can detect leaks and temperature fluctuations in real-time, allowing for prompt corrective actions. This proactive approach evidences a commitment to safety and reliability, fostering a sense of trust among stakeholders.
Trustworthiness is further reinforced through rigorous inspection and maintenance protocols. Regular inspections ensure the integrity of the tanks and the ancillary infrastructure, identifying potential points of failure before they escalate into critical issues. An authoritative stance on maintenance, grounded in real-world experience and recognition of industry best practices, carries significant weight in safeguarding the reliability of chemical storage systems.
In an industry where transparency can mean the difference between trust and skepticism, clear and open communication with stakeholders is paramount. Clients and regulatory bodies alike place immense value on documented proof of compliance, maintenance records, and incident reports. Maintaining such records meticulously not only enhances transparency but also underlines a company’s commitment to accountability and continuous improvement.
Ultimately, the narrative of chemical storage tanks is one woven with the threads of experience, expertise, authoritativeness, and trustworthiness. By drawing on a rich well of industry knowledge, companies can design and implement storage solutions that not only meet but exceed industry standards. Through a steadfast focus on compliance, safety, and innovation, the leaders in this domain elevate the discourse from mere storage to a comprehensive strategy in chemical management. This holistic approach ensures not only operational success but also contributes to the overarching aim of creating safer, more sustainable industrial practices.