When comparing materials for industrial applications, corrosion-resistant FRP (Fiber Reinforced Polymer) stands out due to its remarkable durability and versatility. Used widely across various sectors such as water treatment, chemical processing, and infrastructure, FRP offers unparalleled resistance against corrosive environments. This article delves into the intricacies of FRP, highlighting its benefits, applications, and why it should be considered the material of choice for projects demanding long-term sustainability amidst harsh conditions.
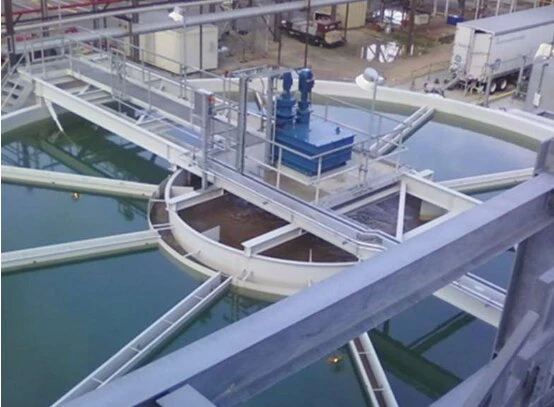
One of the primary advantages of corrosion-resistant FRP is its exceptional durability. Unlike traditional materials such as steel or aluminum, which are prone to rust and corrosion when exposed to harsh chemicals or salty environments, FRP is inherently resistant. This resistance stems from its composite nature; typically consisting of a polymer matrix reinforced with fibers like glass, carbon, or aramid. The polymer serves as an impermeable barrier to corrosive substances, while the fibers impart mechanical strength. This combination ensures longevity, reducing the need for costly repairs and replacements over time.
The expertise in crafting FRP lies in its customization capability. Manufacturers can tailor the chemical composition of the resin, the type of reinforcing fibers, and even the fabrication process to meet specific environmental and mechanical requirements. For instance, in highly corrosive environments such as chemical plants, an FRP composite with a vinyl ester resin matrix may be used to maximize chemical resistance. This level of customization ensures that FRP solutions are not merely adequate but optimal for particular applications.
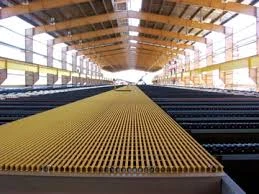
In infrastructure, the authoritativeness of FRP is evident in its growing adoption for constructing bridges, pipelines, and storage tanks. Its strength-to-weight ratio is superior to most metals, allowing for lighter structures without compromising strength. This characteristic is particularly beneficial in seismic zones where structural flexibility can yield better performance during earthquakes. The lightweight nature of FRP also simplifies transportation and installation, resulting in reduced project costs and timelines.
For water and wastewater treatment facilities, FRP's resistance to both chemical and microbial corrosion makes it an ideal material. Unlike concrete, FRP tanks do not degrade over time due to constant exposure to moisture and chemical treatment agents. This translates to a longer lifecycle and reduced maintenance needs, enhancing the credibility of FRP as a trustable solution for municipalities and industrial plants seeking reliable, long-lasting infrastructure.
corrosion resistant frp
A practical experience underscores the usability of corrosion-resistant FRP a large-scale desalination project in the Middle East opted for FRP piping to handle its corrosive brine discharge. Despite the harsh marine environment and high salt concentrations, the FRP pipes have functioned without any signs of degradation, validating their choice showcasing real-world resilience and efficacy.
Moreover, because FRP is non-conductive, it offers safety benefits in electrical applications where the risk of galvanic corrosion or electrical hazards are concerns. This unique feature broadens its applicability across industries that require both safety and durability, further underlining its versatility as an industrial material.
Finally, the trustworthiness of FRP is reinforced through an established track record in harsh environments globally. Many case studies document FRP installations that remain in excellent condition decades after deployment, providing reliability for stakeholders. This longstanding performance record, combined with its technical advantages, positions FRP as a primary candidate for engineers, designers, and decision-makers aiming for sustainable and cost-effective solutions.
Conclusively, corrosion-resistant FRP presents a compelling choice for industries requiring enduring materials in challenging conditions. Its blend of durability, customization, and proven effectiveness substantiates its standing as a superior material when compared to traditional options. Opting for FRP not only ensures resilience and longevity but also exemplifies a commitment to innovative and responsible material use in industrial applications.