The Integral Drill Rod A Revolutionary Tool for Efficient Drilling
The world of manufacturing and engineering has always been on the lookout for tools that can enhance precision, speed up processes, and reduce costs. One such innovation is the integral drill rod, a versatile tool designed to revolutionize drilling operations across various industries.
An integral drill rod combines the functions of a drill bit and a tap in a single tool. This fusion allows users to drill and tap threads in one operation, significantly reducing the time and effort required for traditional methods. By eliminating the need for multiple tools and steps, the integral drill rod not only streamlines production processes but also minimizes setup errors, leading to higher quality end products.
The design of an integral drill rod features a cutting edge similar to a standard drill bit, followed by a thread-forming region that creates the desired threads as it proceeds through the material. This unique structure ensures that the threads are formed immediately after the hole is drilled, preventing any misalignment or deviations that could compromise the thread's integrity.
Material selection for integral drill rods is crucial to their performance and longevity. Typically made from high-speed steel (HSS) or carbide, these rods are heat-treated to withstand the stresses of high-speed drilling and the friction generated during thread formation. HSS offers a good balance of toughness and hardness, while carbide provides superior durability and cutting efficiency, making it ideal for drilling through harder materials.
Industrial applications of integral drill rods range from automobile manufacturing, where they are used to create precise threads for assembly, to construction, where they speed up the installation of threaded rods and bolts
Industrial applications of integral drill rods range from automobile manufacturing, where they are used to create precise threads for assembly, to construction, where they speed up the installation of threaded rods and bolts
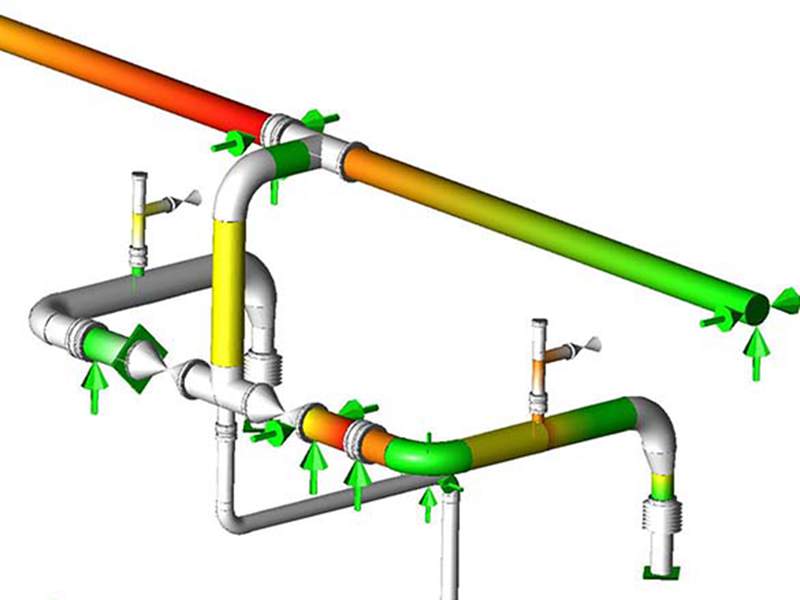
Industrial applications of integral drill rods range from automobile manufacturing, where they are used to create precise threads for assembly, to construction, where they speed up the installation of threaded rods and bolts
Industrial applications of integral drill rods range from automobile manufacturing, where they are used to create precise threads for assembly, to construction, where they speed up the installation of threaded rods and bolts
integral drill rod. Aerospace engineers also rely on integral drill rods to fabricate parts with exacting standards, ensuring the safety and reliability of aircraft components.
The efficiency of integral drill rods is further enhanced by their compatibility with CNC (Computer Numerical Control) machines. These advanced systems can precisely control the drilling depth, speed, and feed rate, optimizing the threading process and resulting in a high degree of accuracy and repeatability.
As technology continues to advance, so too does the development of tools like the integral drill rod. Future enhancements may include coatings to improve lubrication and reduce wear, as well as hybrid materials that combine the benefits of different metals to offer even greater resilience and cutting power.
The integral drill rod represents a leap forward in drilling technology, offering unparalleled convenience and efficiency. Its ability to perform two operations at once not only saves time but also raises the bar for precision and quality in manufacturing. As industries seek to optimize their processes, the integral drill rod is poised to become an essential tool in the drive towards excellence in engineering and production.