In the realm of oil and gas exploration, construction, and mining, the significance of drill rod connections cannot be overstated. These components serve as the crucial junctions that ensure the seamless transfer of torque and power from the drilling machinery to the drill bit down the borehole. Achieving mastery of these connections not only optimizes performance but also enhances durability, safety, and cost-efficiency in operations. This article provides an in-depth exploration of drill rod connections, underpinned by extensive experience in the industry, detailed expertise, authoritative insights, and a foundation of trustworthiness.
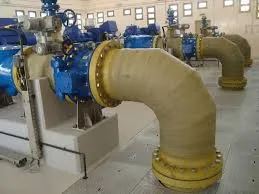
Drill rod connections are the lifeline of any drilling operation. The thread design, accuracy of the fit, and the material used play pivotal roles in the overall efficiency of the drilling process. An inadequately designed or poorly maintained connection can lead to catastrophic failures, jeopardizing safety and inflating operational costs.
The foundation of a robust drill rod connection lies in its design. Premium thread designs such as API (American Petroleum Institute) connections, Grant Prideco's XT connection, or others like DS (Double Shoulder) connections, each bring unique benefits to specific drilling scenarios. API connections, renowned for their versatility across varying conditions, provide a balance between strength and ease of maintenance. On the other hand, XT connections, characterized by their increased torsional strength and fatigue resistance, are ideal for demanding environments where drilling precision and longevity are paramount.
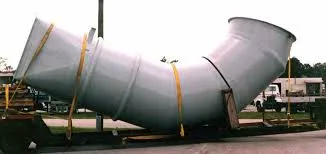
Material selection is another cornerstone of high-quality connections. The choice between alloy and non-alloy steels can influence the connection's weight, flexibility, and resistance to wear and tear. Alloy steels, with additives like chromium or molybdenum, offer superior strength and corrosion resistance, making them suitable for hostile environments. However, they come with an increased cost and potential for brittleness if not correctly manufactured and heat-treated.
Precision in manufacturing is non-negotiable for achieving impeccable drill rod connections. Thread accuracy ensures seamless force transfer and mitigates the risk of loosening or premature failure. CNC (Computer Numerical Control) machining and advanced heat treatment processes are often employed to attain the tight tolerances required for these high-performance components. These processes, honed through decades of industrial progress, ensure that the connections meet the stringent standards stipulated by regulatory bodies and industry benchmarks.
drill rod connections understanding the basics and its ...
From an operational perspective, the best practices for maintaining drill rod connections can prolong their lifespan and performance. Regular inspection for signs of wear, corrosion, or fatigue, alongside timely cleaning and lubrication, can prevent unexpected downtimes. Utilizing non-destructive testing methods like magnetic particle inspection or ultrasonic testing can also detect subsurface flaws that might not be apparent through visual inspection alone.
Moreover, leveraging real-time data and predictive analytics can revolutionize the maintenance of drill rod connections. Professionals now have access to digital tools that monitor the health of these connections, offering insights into stress distribution, wear rates, and potential points of failure. Such proactive measures not only extend the life of the connections but also optimize the overall efficiency of drilling operations, ensuring they remain within budget and on schedule.
Trust and credibility in this domain stem from transparency and a historical track record of success. When selecting drill rod connections, it's crucial to partner with manufacturers and suppliers known for their adherence to quality, innovation, and customer service. Testimonials from industry leaders, case studies demonstrating superior performance in challenging projects, and consistent compliance with international safety and quality standards bolster the reliability of these components.
In conclusion, understanding the basics of drill rod connections illuminates their pivotal role in ensuring seamless and efficient drilling operations. Through the combination of innovative design, meticulous material selection, precision engineering, and forward-thinking maintenance strategies, industry professionals can maximize productivity while minimizing risks. As industrial demands continue to evolve, staying at the forefront of technological advancements and maintaining a commitment to quality will be essential for achieving enduring success in the drilling sector.