With the rapid advancements in mining technologies, equipment for mining with fiberglass components has become a focal point for enhancing performance, safety, and sustainability. As industries push the boundaries of what is possible, fiberglass emerges as a material of choice due to its exceptional characteristics. This persuades manufacturers and mining experts to adopt fiberglass in various mining tools and machinery, signaling a transformative impact on the mining landscape.
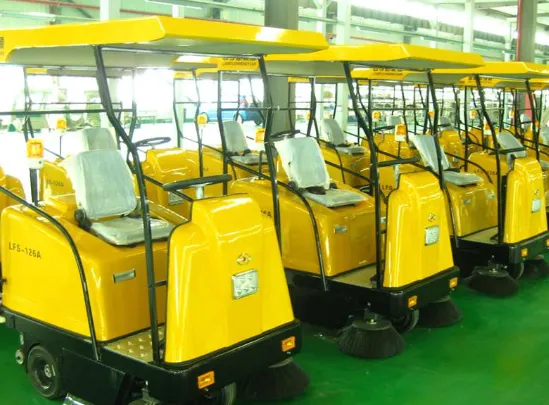
Fiberglass, known for its high tensile strength, durability, and resistance to corrosion, is increasingly being used in the production of mining equipment such as safety helmets, mine ventilation systems, and structural components of large machinery. Unlike traditional metal components, fiberglass does not rust, which is a critical advantage in the often moist and chemically harsh environments in which mining activities occur. Furthermore, its lightweight nature contributes to reduced energy consumption and greenhouse gas emissions, aligning with the industry's move toward more sustainable practices.
The expertise embedded within fiberglass technology enables the design of mining components that excel in performance. For instance, drill casings made with fiberglass can withstand greater stress and shock without deformation, ensuring that operations are not interrupted by mechanical failures. Moreover, fiberglass’s flexibility allows for innovative designs that metal cannot accommodate, offering customized solutions tailored to specific mining needs.
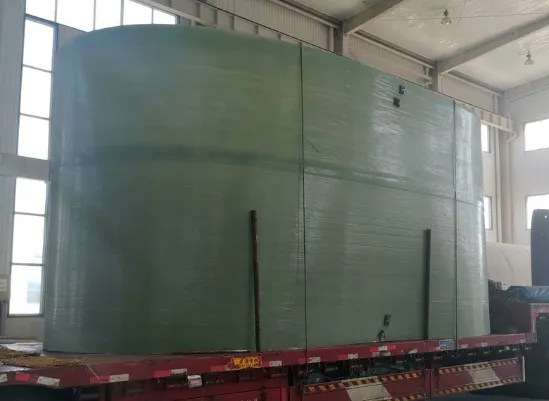
Trust in fiberglass components is well-justified through extensive testing and certification. Products made from fiberglass are subjected to rigorous quality control standards, ensuring they meet international safety and performance benchmarks. This authoritative stance is reinforced by endorsements from leading geologists and engineering bodies, who advocate for its use based on proven data and field success stories.
equipment for mining with fiberglass components
In real-world applications, mining operations using fiberglass-enhanced equipment have reported significant improvements in efficiency. A notable example comes from a high-altitude copper mine in South America, where the utilization of lightweight fiberglass ventilation ducts facilitated quicker installation times, resulting in 30% more efficient air circulation and a tangible reduction in dust-related health issues among workers. The cost savings from reduced downtime and maintenance were substantial, further underscoring the economic benefits.
Furthermore, fiberglass's non-conductive properties are invaluable in ensuring safety in mines where electrical equipment is extensively used. Traditional metal components can pose a risk of electric shock and short circuits, which fiberglass can proficiently mitigate, offering peace of mind to operators and safety officers.
As fiberglass technology continues to evolve, ongoing research and development promise further breakthroughs that will reinforce its role in the mining sector. Future applications may include advanced composite materials combining fiberglass with other compounds to enhance thermal insulation or noise reduction—addressing common industry challenges.
In conclusion,
the advantages of using fiberglass components in mining equipment are clear. While metals have served the industry well throughout its history, the transition to more advanced materials like fiberglass speaks to a commitment to technology evolution, better safety standards, and environmental responsibility. Companies adopting fiberglass in their mining operations not only gain a competitive edge through improved efficiency and reduced costs but also contribute to a greener and safer mining industry, benefitting communities and the environment alike. The investment in fiberglass is an investment in innovation, sustainability, and operational excellence.