In an era where technology transforms rapidly, Fiberglass Reinforced Plastic (FRP) remains a critical component in industrial applications due to its superior strength-to-weight ratio, resistance to corrosion, and durability. However, one of the major challenges associated with FRP is its cleaning and maintenance, particularly in the laundering process. This often involves complicated steps,
requiring efficient methods to streamline these procedures to ensure both cost-effectiveness and product longevity.
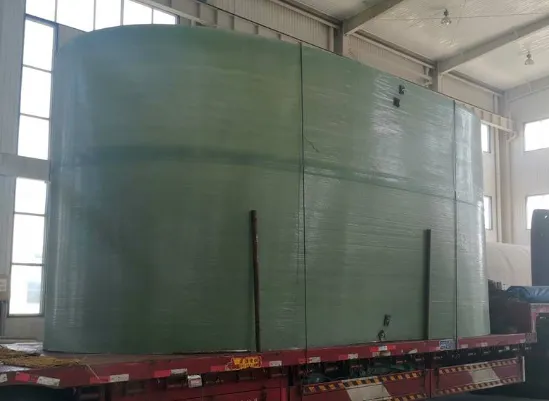
A pioneering approach in the laundering of FRP materials involves leveraging advanced ultrasonic cleaning technology. Ultrasonic cleaners use high-frequency sound waves, producing cavitation bubbles in a cleaning solution that penetrate deeply into the materials' surfaces. This method is excellent for removing all sand particles, resin residues, and contaminants without causing any degradation to the fibers, ensuring the structural integrity of the FRP is maintained.
Furthermore, introducing eco-friendly solvent solutions can significantly enhance the efficiency of FRP laundering. These biodegradable solvents dissolve harmful deposits without emitting volatile organic compounds (VOCs), ensuring compliance with environmental regulations and improving workplace safety. The integration of these solvents into a closed-loop laundering system further minimizes waste and reduces water consumption, which not only benefits the environment but also reduces operational costs.
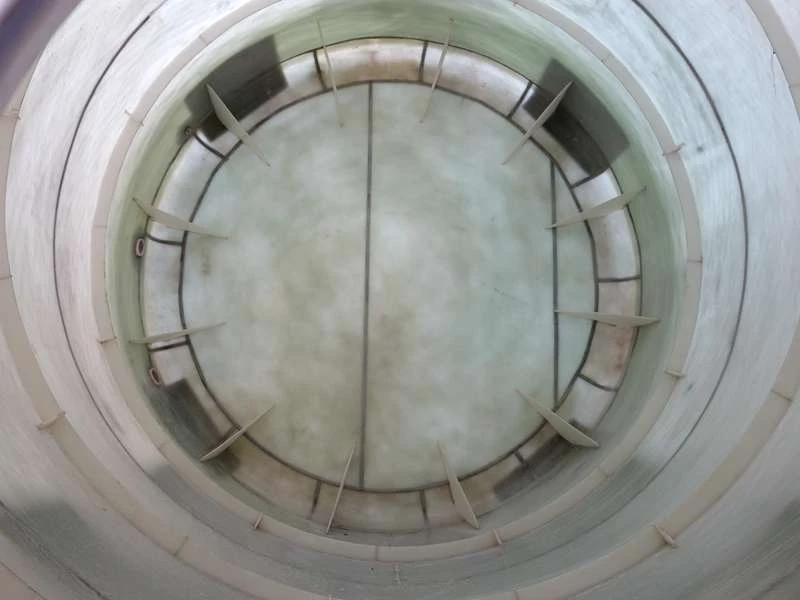
An additional step in streamlining FRP laundering methods involves the implementation of automated brushing systems. These systems ensure that the FRP surface is brushed clean with consistent pressure, eliminating human error and ensuring uniform cleaning across all surfaces. Automation in the laundering process also improves cycle time and can significantly improve throughput in industrial applications.
Ensuring that personnel are well-trained in the nuances of FRP materials is essential. Skilled technicians must understand the intrinsic properties of FRP to avoid exposure to harsh chemicals that can impair the composite matrix. Regular workshops and educational courses can empower staff with the knowledge to handle FRP products appropriately during laundering, thus enhancing both performance and safety.
exploring efficient methods for streamlining frp laundering ...
Moreover, collaboration with material scientists can contribute to the development of FRP blends that incorporate self-cleaning properties. Using photocatalytic coatings, such as titanium dioxide, on FRP surfaces can harness natural sunlight to break down organic contaminants. This innovative approach can reduce the necessity of frequent laundering, conserving resources and extending the life of FRP products.
Establishing a reliable benchmark for quality control is another essential aspect. By using non-destructive testing methods like neutron radiography or digital holography after laundering, any subtle changes in the internal structure of the FRP can be identified, ensuring that laundering processes do not compromise the material's properties.
The synergy of these approaches represents a significant leap towards achieving a systematic and efficient FRP laundering process. Organizations must prioritize innovation and quality assurance to maintain competitiveness in the materials industry. By investing in cutting-edge technology and sustainable practices, companies not only enhance their operations but also strengthen their reputation as industry leaders committed to excellence.
In conclusion, streamlining FRP laundering methods requires a multi-faceted approach that combines the latest technological advancements, environmental responsibility, and expert personnel training. This comprehensive strategy ensures that FRP materials remain a vital, resilient option in industrial applications, meeting the growing demands for sustainability and efficiency in today’s market.