Fiberglass 90 degree elbows have become a pivotal component in modern piping systems, renowned for their durability and versatility across a myriad of applications. As industries evolve and the demand for robust infrastructure solutions increases, the importance of understanding the unique characteristics of these fittings cannot be overstated.
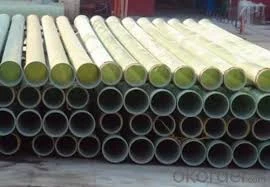
Fiberglass, known for its impressive strength-to-weight ratio, is an ideal material for pipe fittings, particularly in environments where corrosion poses a significant threat to infrastructure longevity. The 90 degree elbow, a critical component in routing pipelines, allows for a shift in direction without compromising the integrity or flow efficiency of the system. This makes it indispensable in industries ranging from chemical processing to wastewater management and beyond.
The practical advantages of fiberglass 90 degree elbows are worth noting. Unlike metal counterparts, fiberglass resists rust and chemical degradation, which significantly prolongs the lifecycle of the pipeline system. This resistance to corrosion is particularly beneficial in coastal or acidic environments where metal pipes suffer from accelerated wear and tear. Furthermore, the lightweight nature of fiberglass makes installation and transportation more manageable, reducing labor costs and time.
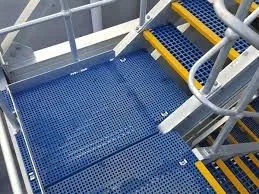
Moreover, the manufacturing process of fiberglass elbows leverages advanced techniques to ensure precision and reliability. Each elbow is crafted with meticulous attention to detail, ensuring that the internal and external dimensions conform strictly to industry standards. This precision manufacturing guarantees that the fittings can withstand high pressures and temperatures typical in industrial applications, thus providing peace of mind to engineers and contractors alike.
Expertise in the field of fiberglass composites plays a critical role in the production of these high-quality 90 degree elbows. Industry leaders employ a team of specialized engineers who continuously innovate the design and production processes. By conducting rigorous testing and analysis, these experts are able to refine product features, enhancing tensile strength and thermal tolerance. Their deep understanding of composite materials ensures that the final product meets the dynamic demands of modern infrastructure projects.
fiberglass 90 degree elbow
Authoritativeness in the market is further cemented by compliance with global standards and certifications. Fiberglass 90 degree elbows produced by reputable manufacturers are often accredited by organizations such as ASTM and ANSI, which validate their suitability for various applications. These certifications not only affirm the mechanical and thermal properties of the products but also build trust among clientele who are increasingly conscious of safety and environmental concerns.
Trustworthiness is fostered by transparent business practices and the provision of comprehensive technical support to customers. Manufacturers typically offer extensive documentation, including installation guides and maintenance manuals, which empower users to maximize the lifespan and performance of their fiberglass fittings. Additionally, dedicated customer service teams are available to address any queries or technical challenges that may arise, further reinforcing confidence in the product.
Case studies from industry applications underscore the real-world benefits of utilizing fiberglass 90 degree elbows. In the oil and gas sector, for instance, pipelines outfitted with these fittings have demonstrated remarkable resilience in harsh offshore conditions, where metal pipes had previously failed. Similarly, in the chemical industry, installations have reported significant reductions in maintenance costs due to the non-reactive nature of fiberglass, allowing for uninterrupted production schedules and enhanced operational efficiency.
Looking to the future, advancements in composite technology promise to enhance the performance characteristics of fiberglass 90 degree elbows further. Researchers are exploring hybrid materials and nano-enhancements to improve durability and reduce costs, positioning fiberglass as an even more attractive option for sustainable development.
In summation, fiberglass 90 degree elbows stand out as a superior choice for modern piping systems thanks to their corrosion resistance, precision manufacturing, and compliance with industry standards. The collaboration between seasoned engineers and forward-thinking manufacturers ensures that these fittings remain at the forefront of infrastructure advancement. As industries worldwide continue to seek reliable and cost-effective solutions, fiberglass elbows are poised to meet and exceed these expectations, now and in the future.