Fiberglass flanges have emerged as a crucial component in various industrial applications, owing to their robust characteristics and versatility. These flanges are typically used to join sections of pipes, valves, pumps, and other integral parts of a piping system, providing a reliable seal while maintaining the structural integrity of the overall assembly. Recognized for their exceptional corrosion resistance, fiberglass flanges are preferable in environments where traditional metal flanges may deteriorate or fail.
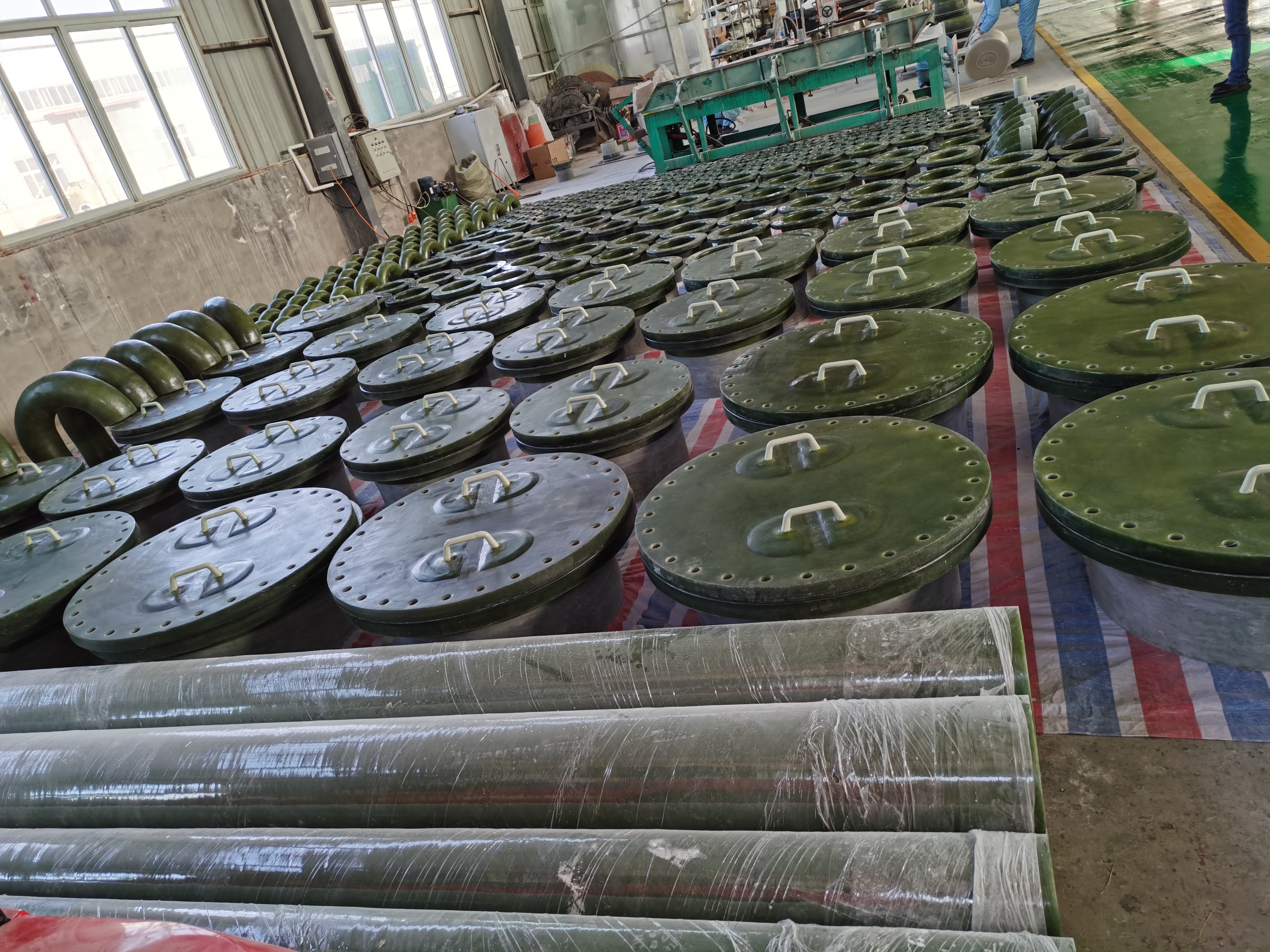
The unique properties of fiberglass flanges begin with the materials used in their manufacturing. Comprised of a composite of glass fibers and resin, these flanges offer superior resistance to harsh chemicals, making them ideal for chemical processing plants where exposure to corrosive substances is frequent. The use of high-quality resin ensures that the flange maintains its shape and resilience under thermal and mechanical stress, thereby extending its service life far beyond that of traditional materials.
From an engineering perspective, fiberglass flanges stand out due to their lightweight nature. The reduced weight translates into lower transportation and installation costs, easing the burden on labor and equipment. Yet, this weight reduction does not come at the expense of strength. Fiberglass flanges can endure significant pressure and temperature variations, thus guaranteeing performance and safety in demanding applications such as waste treatment and desalination plants.
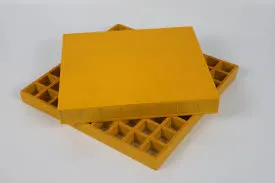
Professionals in the industry also appreciate the electrical insulation properties of fiberglass flanges. Traditional metal flanges can pose risks in applications where electrical conductivity is a concern. In contrast, fiberglass flanges mitigate these risks, making them suitable for use in electrical power plants and substations, where the insulation of components is critical for ensuring system integrity and operator safety.
fiberglass flange
Despite their many advantages, the successful deployment of fiberglass flanges requires a precise understanding of their application limits and installation requirements. Experts emphasize the importance of adhering to manufacturer guidelines for torquing and gasket selection to ensure a leak-proof connection. Regular maintenance and inspections are also recommended to monitor the condition of the flanges, especially in high-stress environments, to prevent premature failure.
The credibility of fiberglass flanges as high-performance components is further backed by extensive research and development in composite material science. Research institutions and manufacturers are continually seeking ways to enhance the material properties of fiberglass, fostering innovation that translates into improved performance and reliability in industrial applications.
For companies contemplating the integration of fiberglass flanges into their systems, it's crucial to partner with reputable manufacturers who possess a proven track record of delivering quality products. These manufacturers not only supply high-grade fiberglass flanges but also offer comprehensive support, from initial product selection to after-sales service, reinforcing the trustworthiness of their offerings.
In conclusion, fiberglass flanges offer an unmatched combination of durability, cost-effectiveness, and versatility, making them indispensable in modern industrial operations. By selecting the right flange type and adhering to best practices in installation and maintenance, industries can leverage fiberglass flanges to enhance performance and ensure operational reliability, ultimately safeguarding their investments in infrastructure and resources.