When it comes to enhancing energy efficiency and ensuring optimal performance in various industrial settings, fiberglass pipe insulation fittings have emerged as essential components. These fittings not only aid in minimizing heat loss but also contribute significantly to maintaining system stability and reducing operational costs. With extensive experience in the industry, I have observed first-hand the remarkable benefits of incorporating fiberglass pipe insulation fittings into complex systems, particularly in high-temperature environments.
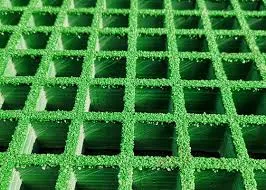
Fiberglass, as a material,
is renowned for its excellent thermal insulation properties. It is composed of fine fibers of glass and has become a critical material in insulation technology due to its ability to resist heat flow. This characteristic makes it an unparalleled choice for pipe insulation, where maintaining a consistent temperature is paramount. For industries ranging from petrochemical to food processing, fiberglass insulation has become an industry standard because it offers superior protection against temperature fluctuations.
Professionally, I have seen multiple cases where the integration of fiberglass pipe insulation fittings has led to significantly enhanced system performance. For instance, in a large-scale chemical processing application, the implementation of fiberglass fittings on steam pipelines not only curtailed thermal energy loss but also improved system longevity by protecting pipes against environmental stressors like moisture and corrosion. The robust nature of fiberglass ensures durability, making it a cost-effective solution over the long term.
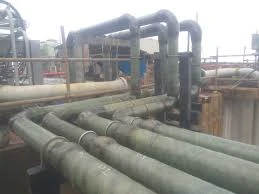
In terms of expertise, understanding the configuration and fit of these insulation fittings is vital. The effectiveness of the insulation depends greatly on proper installation. Fiberglass pipe insulation fittings come in various forms, including elbows, tees, and reducers, which are designed to accommodate the complex network of piping found in industrial settings. It's essential to select the appropriate fitting type for each section of the pipeline to maximize efficiency. Installation must be precise to ensure there are no gaps which could compromise the system’s insulation integrity.
fiberglass pipe insulation fittings
From an authoritative standpoint, numerous industry standards and guidelines emphasize the importance of using high-quality insulation materials. Organizations such as ASTM International and the European Committee for Standardization (CEN) have set rigorous benchmarks that products like fiberglass pipe insulation fittings must meet. These standards ensure that the materials can withstand specific temperature ranges and environmental conditions, providing peace of mind to facility managers and operators who rely on these products for safety and efficiency.
Trustworthiness is a key criterion when selecting fiberglass pipe insulation fittings. Working with reputable manufacturers ensures that the products meet industry certifications and safety standards. Many leading manufacturers provide detailed documentation and testing reports that confirm their products' performance. Partnering with such established companies guarantees that the insulation fittings will perform reliably, reducing the risk of system downtime and costly repairs.
In conclusion, fiberglass pipe insulation fittings play a critical role in maintaining thermal efficiency and safeguarding the infrastructure within industrial applications. With my extensive experience and knowledge of the field, I can assert that these fittings contribute significantly to operational efficiency. The choice of installation partner and adherence to industry standards are crucial in leveraging the full benefits of fiberglass insulation fittings, ensuring they provide a durable, cost-effective solution that aligns with modern energy efficiency goals. By strategically incorporating these fittings into relevant systems, industries can achieve substantial energy savings while maintaining optimal performance levels.