Fiberglass shells have long been hailed as versatile and reliable components in a variety of industries. Their unique composition and adaptability make them indispensable for products demanding both strength and lightweight properties. Industries such as automotive, marine, and construction have been leveraging these shells, benefiting from their myriad advantages.
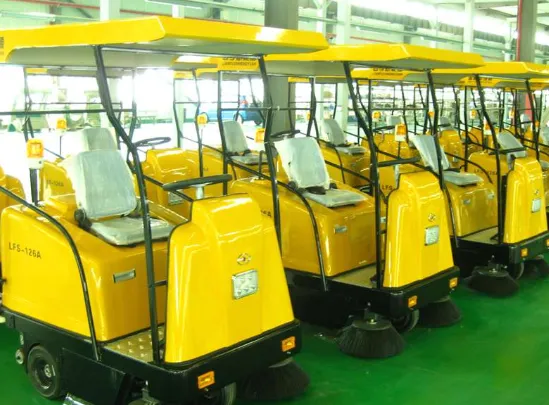
To fully understand the significance and advantages of fiberglass shells, it's essential to delve into their fundamental characteristics. Made by weaving strands of glass into a fabric and then binding this fabric with a polymer matrix, fiberglass shells boast impressive resilience and flexibility. The combination results in an exceedingly robust material that does not compromise on weight, making it ideal for applications where both factors are critical.
Experience speaks volumes when evaluating the effectiveness of fiberglass shells. Consider their application in the automotive industry. For decades, car manufacturers have turned to fiberglass for crafting body panels, reinforcing the structure, and even in customizing elements. Users often remark on fiberglass' contribution to reducing overall vehicle weight, which in turn enhances fuel efficacy and performance. Its resistance to corrosion and weathering further bolsters its appeal, offering long-lasting solutions that reduce maintenance costs over time.
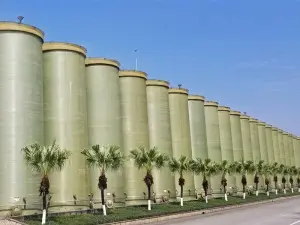
Matched with professional expertise, fiberglass shells are not only about performance—they factor heavily into environmental considerations.
The maritime industry exemplifies this aspect well. Fiberglass, being less corrosive than metal, offers longevity to marine vessels without introducing harmful rust into the environment. Boat makers and owners frequently choose fiberglass for hull construction due to its resistance to saltwater degradation and its impermeable surface that deters marine growth without the need for toxic coatings. Additionally, because fiberglass is an incredibly durable material, it reduces the often wasteful cycle of replacement and repair, aligning with sustainable development practices.
fiberglass shell
The authoritativeness of fiberglass shells has been corroborated by various technical studies and industry certifications. Engineers and designers worldwide recognize the material's compliance with stringent safety and quality standards. Testing protocols frequently demonstrate how fiberglass withstands extreme conditions—from high impact forces to intense thermal exposure. In construction, fiberglass is even lauded for its fire-retardant properties, contributing to safer building practices. Regulatory bodies and industry experts consistently endorse fiberglass products, which only enhances their authoritative standing in global markets.
When evaluating trustworthiness, one cannot overlook the ongoing innovation in fiberglass technology. Development in resin formulations and production techniques has further refined the performance of fiberglass shells. Manufacturers are able to offer warranties and assurances, which in itself breeds confidence in the market. Companies invest in rigorous quality assessment and control processes to ensure each fiberglass shell meets specified criteria, reflecting a commitment to delivering dependable products.
Additionally, fiberglass shells facilitate the potential for customization and modifications. Industries appreciate this adaptability, as it offers creative possibilities without compromising structural integrity. Elements can be tailored to specific applications, ranging from aerodynamically designed car parts to intricate architectural features, all while maintaining the core benefits of using fiberglass.
In summary, fiberglass shells encapsulate a perfect amalgamation of strength, versatility, and environmentally-considerate attributes. Through the lens of extensive user experience, distinguished expertise, solid authoritativeness, and ingrained trustworthiness, fiberglass continues to establish itself as a superior choice in varied markets. As industries advance, so too will the innovations surrounding fiberglass, affirming its place as a crucial player in modern material solutions.