Fiber Reinforced Plastic (FRP) blind flanges are revolutionizing the way industries approach sealing and piping solutions, offering an unparalleled combination of strength, corrosion resistance, and cost-effectiveness. As companies globally strive for increased efficiency and sustainability, FRP blind flanges present themselves as an invaluable component in various industrial applications.
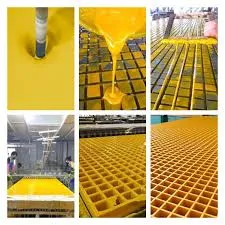
FRP blind flanges hold a commanding advantage in environments where metal flanges fail due to corrosion or weight issues. Traditionally, industries relied heavily on metal flanges which, while strong, are susceptible to rust and degradation, especially in aggressive chemical environments. Conversely, FRP materials do not corrode, even when exposed to the harshest chemicals, making them ideal for sectors like chemical processing, wastewater management, and offshore oil drilling.
Moreover, when considering weight, FRP blind flanges are remarkably lightweight compared to their metal counterparts. This feature significantly reduces the transportation, handling, and installation costs. Industries working with large piping systems can benefit from lower operation expenditures and reduced labor costs, paving the way for more streamlined processes.
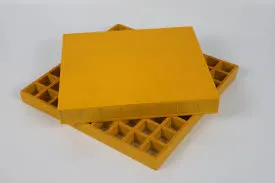
From a technical standpoint, the expertise embedded in manufacturing FRP blind flanges speaks to their superior performance attributes. These flanges are designed using sophisticated engineering techniques that incorporate multidirectional layers of reinforced fabrics and superior resins. This manufacturing process ensures that FRP blind flanges exhibit excellent tensile strength and can endure high-pressure environments, a necessity for many industrial applications.
The authoritativeness of FRP blind flanges is underscored by their expanding use among industry leaders. As more companies prioritize longevity and reliability, the demand for these components has seen a significant uptick. Companies such as Ashland and Owens Corning have invested heavily in FRP technologies, affirming the product's reliability and endorsing its widespread use. Peer-reviewed studies further reinforce their applicability, citing case studies where FRP blind flanges have sustained performance in critical infrastructure projects over decades.
frp blind flange
Trustworthiness extends beyond mere functionality; it is about ensuring a product can be depended upon when it matters most. FRP blind flanges are subjected to rigorous testing procedures to adhere to international standards, including pressure testing, impact resistance assessments, and chemical compatibility checks. These tests ensure that the flanges perform consistently under the prescribed conditions, mitigating the risk of failure.
A real-world testament to the reliability of FRP blind flanges can be seen in their deployment in a wastewater treatment plant in Florida. The plant, which operated with metal components, faced continual issues with corrosion, leading to leaks and maintenance shutdowns. The switch to FRP blind flanges resulted in a marked improvement in performance, eliminating the corrosion-related downtimes. This transition not only improved operational efficiency but also resulted in substantial savings on maintenance and part replacement costs.
The environmental impact of choosing FRP blind flanges cannot be understated. With industries moving towards greener operations, utilizing materials with a longer lifespan that require less resource-intensive maintenance is a substantial benefit. The durability and longevity of FRP materials result in a lower carbon footprint over their lifecycle when compared to traditional materials.
In conclusion, FRP blind flanges represent a strategic investment in quality and reliability. Their unique properties offer real-world improvements in efficiency, reduce operational costs, and support sustainable industrial practices. As industries continue to navigate the challenges of modern manufacturing and construction, the advanced design and proven performance of FRP blind flanges solidify their role as a cornerstone in future piping solutions. Embracing these innovative solutions ensures industries not only meet their present needs but also ensure resilience and adaptability for future challenges.