In the ever-evolving world of automotive engineering, the debate around using advanced materials to create lighter, faster, and more cost-effective vehicles continues to captivate industry professionals and consumers alike. One such material making headlines is Fiberglass Reinforced Plastic (FRP), a composite material that has carved a niche for itself in the realm of automotive manufacturing. FRP's unique properties make it particularly suitable for crafting lightweight components without compromising on strength or durability.
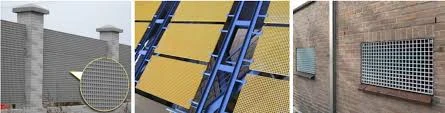
The magic of FRP lies in its composition. It is engineered by embedding glass fibers within a plastic resin, which endows it with the ability to withstand high levels of stress while maintaining flexibility. This adaptability allows automotive designers to push the boundaries of innovation, crafting not only aesthetically pleasing designs but also ensuring superior aerodynamic performance. The lightweight nature of FRP offers significant benefits in fuel efficiency and handling, making it a preferred choice for modern performance vehicles and eco-conscious minds alike.
A testament to FRP's growing acceptance and reliability can be seen in its adoption across various sectors within the automotive industry. High-performance sports car manufacturers often utilize FRP to mold body panels, spoilers, and other components where weight reduction can lead to notable performance gains. By integrating FRP, these manufacturers achieve a perfect balance — a vehicular symphony of decreased weight, improved speed, and agile handling.
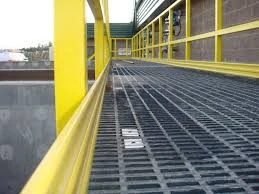
The manufacturing process of FRP is an intricate dance of art and science. Designers sculpt the intended automotive part's mold, which is then intricately layered with glass fibers. The application of resin follows, acting as a binding agent, before the composite is cured under high temperatures. The result? A part that is not only incredibly strong but resistant to corrosion and weathering — attributes highly sought after in a variety of automotive applications.
frp car
Beyond the realm of supercars, FRP's reach extends to commercial and passenger vehicles where its properties are leveraged to improve longevity and reduce maintenance costs. Vehicles that frequently operate in challenging environments — think off-road conditions or coastal regions prone to rust — benefit immensely from FRP’s rust-resistant attributes, maintaining their integrity where traditional metal counterparts may falter.
However, while the advantages of FRP are numerous, their application must be pursued with thorough expertise. Challenges such as repair difficulty and higher initial production costs necessitate careful consideration. This is where industry expertise truly shines, with manufacturers employing advanced technology and skilled artisans to maximize the material's potential.
Trust in FRP continues to grow backed by extensive industry research and collaborative efforts to overcome its challenges. Industry leaders invest in technological advancements, refining production techniques, and ensuring that FRP components meet rigorous safety and performance standards. As a result, consumers can enjoy peace of mind, entrusting their vehicles to a material that promises durability, safety, and sustainability.
Navigating the dynamic landscape of automotive materials requires keen insight and informed decision-making. FRP stands as a strong candidate, celebrated for its numerous attributes, each offering unique advantages that align with the modern pursuit of efficiency, innovation, and ecological responsibleness. As automotive technology advances, FRP remains at the forefront, having proven itself a material of the future, ushering in a new era of automotive design and application efficiency.