FRP (Fiber Reinforced Plastic) car body components have been pivotal in transforming the automotive industry with their lightweight, durable, and versatile nature. Having delved deeply into the intricacies of FRP usage in car manufacturing, I find its applications not only innovative but also critical to addressing the growing demand for efficiency and sustainability in vehicles.
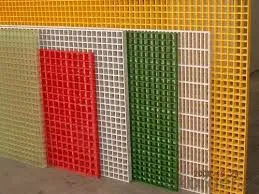
To unpack the advantages of FRP car bodies, consider the fundamental characteristics that set these materials apart. FRP composites are primarily celebrated for their impressive strength-to-weight ratio. By integrating fibers like glass or carbon with a polymer matrix, manufacturers achieve remarkable structural rigidity while significantly reducing weight. This weight reduction is pivotal in improving fuel efficiency, enhancing speed, and reducing emissions, thus aligning with global efforts to minimize the automotive industry's carbon footprint.
FRP's versatility is another noteworthy feature. Unlike traditional materials, FRP can be molded into complex shapes and designs, providing designers with unprecedented creative freedom. This capacity for customization allows for aerodynamically optimized vehicle bodies, contributing directly to enhanced vehicle performance and aesthetic appeal. Moreover, the ability to produce bespoke components without the need for excessive tooling costs makes FRP an economically viable solution for both large-scale manufacturers and smaller bespoke producers.
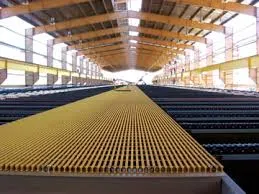
From a durability perspective, FRP stands resilient against the wear and tear commonly encountered in automotive applications. Its innate resistance to corrosion, impacts, and harsh weather conditions ensures that FRP car bodies can maintain their integrity over time, reducing maintenance costs and prolonging the vehicle's lifespan. Additionally, repairs, when necessary, are often simpler and quicker, thanks to the composite nature of the material, which can be patched or re-bonded efficiently.
frp car body
Critically, the adoption of FRP in car bodies amplifies sustainability efforts. As the automotive sector faces increasing scrutiny over its environmental footprint, the recyclable nature of many FRP components positions it as an eco-friendly alternative to metals. Manufacturers dedicated to creating more sustainable vehicles view FRP as a means to achieve significant progress in this regard without sacrificing performance or aesthetic value.
However, leveraging the full potential of FRP in car body production requires in-depth expertise and a commitment to innovative engineering practices. Engineers must navigate the challenge of integrating FRP with other automotive systems to ensure safety and performance. This involves optimizing fiber orientations, laminate thickness, and bonding techniques to meet rigorous safety standards. The expertise involved in these processes underscores the importance of ongoing research and development, which continually refines FRP applications and expands their potential uses.
It's essential to address the sense of authority and trustworthiness surrounding FRP applications. As an established material in various industries, its credibility is continuously reinforced by successful implementations in automotive design. Collaborative efforts between material scientists, automotive engineers, and industry leaders have led to significant advancements in FRP technology, further validating its role in future car manufacturing.
In summary, FRP car body components embody a transformative shift towards more efficient, sustainable, and versatile vehicle design. Embracing the benefits of FRP, alongside a sophisticated understanding of its properties and applications, allows the automotive industry to forge a path that aligns with modern demands for innovation, performance, and environmental responsibility. As the shift continues, FRP's role in redefining vehicle manufacturing solidifies, promising a future where cars are as much a testament to human ingenuity as they are to our commitment to preserving the planet.