Fiber Reinforced Polymer (FRP) covers have gained significant traction in a variety of industries due to their lightweight, durable, and corrosion-resistant nature. These attributes make them an attractive alternative to traditional materials such as steel and concrete. By integrating these innovative FRP covers into their operations, businesses can experience enhanced functionality and long-term economic benefits. This article delves into the experiences and expertise surrounding FRP covers, highlighting their authority and trustworthiness in the product market.
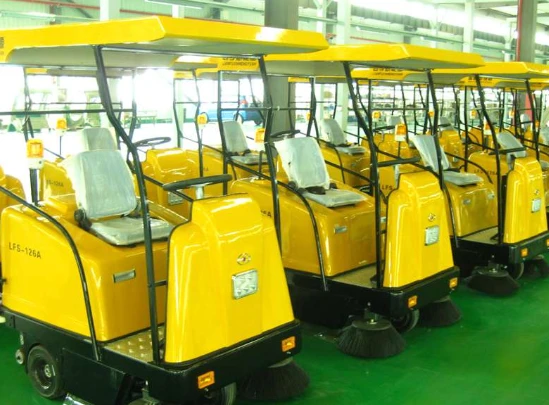
FRP covers are engineered to withstand harsh environmental conditions, which makes them particularly valuable in corrosive environments, such as wastewater treatment plants and chemical processing facilities. The unique composition of FRP involves a polymer matrix reinforced with fibers, typically glass or carbon, which results in a material that can be 70% lighter than steel yet still exceptionally strong. Users consistently report that the reduced weight of FRP covers not only eases installation processes but also decreases transportation and handling costs, without compromising on performance integrity.
The expertise behind FRP cover technology is rooted in decades of composite material research and development. Engineers in this field have honed the manufacturing processes to ensure that these covers meet stringent industry standards for safety and durability. One commonly cited advantage is their resistance to UV radiation and chemical exposure, which extends the product's lifespan significantly compared to metal counterparts. In industries where exposure to corrosive substances or outdoor elements is inevitable, adopting FRP covers can lead to fewer replacements and maintenance demands, enhancing operational efficiency.
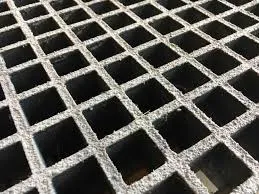
Industries such as oil and gas, transportation, and public infrastructure have recognized the authoritative role of FRP covers. Within these sectors, FRP applications have been rigorously tested and certified by professional bodies, cementing their status as reliable solutions for critical infrastructure components. For instance, in bridge construction, FRP covers contribute to longer-lasting bridge decks, significantly reducing lifecycle costs. The combination of strength, flexibility, and resistance to environmental stressors positions FRP as a frontrunner in innovative engineering solutions.
frp cover
Trustworthiness is a cornerstone of FRP cover applications, and this trust is built on empirical evidence and customer testimonials. Many businesses choose to share their success stories, where the deployment of FRP covers led to improved safety records and incalculable cost savings.
Professionals who have transitioned to this advanced material frequently highlight its predictability and consistent performance over time. This documented reliability is often a determining factor for new consumers and industries considering FRP solutions for the first time.
Given the growing environmental concerns and the push for sustainable practices, FRP covers also meet the eco-friendly requirements many companies now face. The production process of FRP materials is less energy-intensive compared to traditional materials, and their long lifecycle translates into less frequent replacements and waste. This characteristic aligns with the sustainability objectives of many modern corporations, allowing them to meet regulatory standards while reducing their carbon footprint.
In summary, the adoption of FRP covers offers multifaceted benefits that address both functional and environmental objectives. With documented experience in diverse industries, proven expertise through stringent testing and certification, acknowledged authority in critical applications, and a strong track record of trustworthiness, FRP covers stand out as a superior choice in the realm of durable materials. For companies seeking long-term, cost-effective, and environmentally conscious solutions, FRP covers provide the necessary assurances of quality and performance.