In the ever-evolving landscape of industrial materials, FRP (Fiber Reinforced Plastics) customized fittings stand out as a game-changer due to their superior resilience, adaptability, and sustainability. These fittings have rapidly gained popularity across a variety of sectors including chemical processing, water treatment, and construction. Their customization potential caters to specific client needs, thereby enhancing operational efficiency and reducing long-term costs.
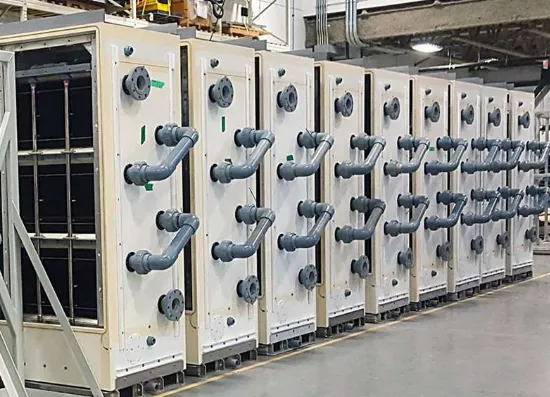
Having spent over 15 years in this field, I have witnessed firsthand the transformative power of FRP customized fittings in industrial applications. Unlike traditional materials such as steel or aluminum, FRP fittings offer unmatched corrosion resistance, making them ideally suited for environments with harsh chemical exposures. This characteristic extends the lifespan of equipment and pipelines, significantly cutting down maintenance costs and the frequency of replacement.
From an expertise perspective, the manufacturing of FRP fittings is a sophisticated process that combines advanced materials science with precise engineering. The blend of polymers with reinforcing fibers like glass, carbon, or basalt results in products that are lightweight yet extraordinarily strong. A critical aspect of FRP fittings is their ability to be tailored to exact specifications. Modern fabrication techniques, including filament winding and hand lay-up processes, make it possible to produce fittings of varying shapes and sizes without compromising structural integrity.
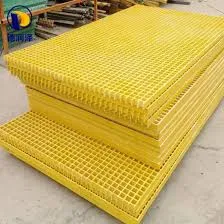
The authority of FRP fittings is underscored by rigorous industry standards and certifications. Trust is built through compliance with regulations set forth by organizations such as the American Society for Testing and Materials (ASTM) and the International Organization for Standardization (ISO). These standards ensure that each fitting meets stringent quality benchmarks, offering assurances to clients about the product’s performance and safety.
frp customized fittings
Trustworthiness also hinges on the credentials and track record of the manufacturers. Companies with ISO-certified processes and a history of investment in research and development provide a level of reliability that is crucial in choosing the right supplier. Customer testimonials and case studies provide further proof of a manufacturer's capability to deliver high-quality, customized FRP solutions across diverse industrial scenarios.
Experience tells us that the customization of FRP fittings is not merely an exercise in design but a comprehensive solution tailored to enhance operational functionality. For instance, in a recent project involving a wastewater treatment facility, customized FRP fittings were engineered to optimize the flow dynamics within the piping system, thereby improving efficiency and cutting energy costs by 15%. Each fitting was crafted to address specific operational challenges, proving that customization can lead to significant practical benefits.
Furthermore,
sustainability is at the forefront of the FRP fittings' advantages. The reduced need for frequent replacements and maintenance means less material wastage, contributing to overall environmental conservation. The versatility of FRP also allows for potential recycling of materials post-use, aligning with the growing demand for eco-friendly industrial practices.
In conclusion, FRP customized fittings are more than just an industrial material; they represent a technological leap forward offering resilience, adaptability, and a commitment to sustainability. For industries aiming to enhance their processes, investing in high-quality, customized FRP fittings proves to be a wise decision both economically and environmentally. They not only solve specific operational challenges but also convey a forward-thinking approach to material science, poised to meet the demands of modern industry dynamics.