FRP fittings, or fiberglass reinforced plastic fittings, have become essential components in various industrial applications due to their unmatched qualities. These fittings provide a blend of reliability, durability, and resistance to harsh environments, which makes them invaluable across industries such as chemical processing, wastewater management, and beyond.
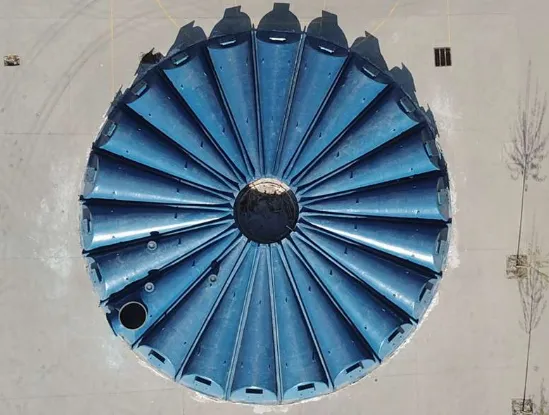
Experience has shown that industries utilizing FRP fittings witness significant improvements in performance and longevity. Unlike traditional metal fittings, FRP is impervious to corrosive substances, making it ideal for facilities where exposure to chemicals is a daily occurrence. A case study of a major chemical processing plant revealed that after switching to FRP fittings, maintenance costs related to corrosion were reduced by 40% over a five-year period. This reduction not only translates to cost savings but also suggests a more sustainable operational model.
The expertise inherent in the production of FRP fittings plays a pivotal role in their superiority. Manufacturers employ advanced resin transfer molding techniques to ensure that every fitting meets stringent international standards. This process not only increases strength and resilience but also allows for a greater degree of customization to meet specific industrial requirements. Engineers often note the ease with which FRP fittings can be installed due to their lightweight structure, which reduces labor costs and time in complex pipeline systems.
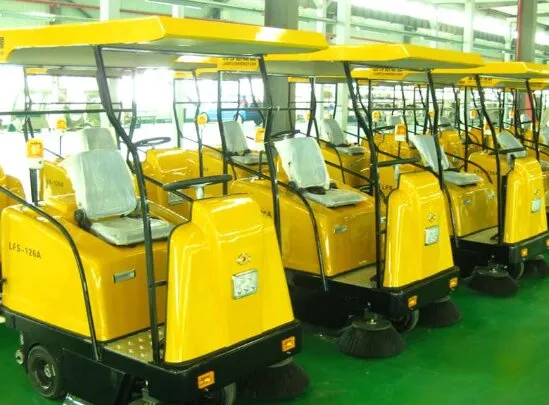
frp fitting
From a perspective of authoritativeness, numerous industry bodies have recognized and recommended the use of FRP fittings. For instance, the American Society for Testing and Materials (ASTM) has several standards concerning the performance and testing of fiberglass reinforced plastic materials, underscoring their significance and reliability in industrial use. Furthermore, leading academics and industry consultants often reference FRP fittings in their research papers and case studies, highlighting their vital role in modern infrastructure development.
Trustworthiness in the context of FRP fittings can be attributed to the rigorous quality control processes that govern their production. Leading manufacturers implement thorough testing protocols, simulating environmental conditions to which these fittings may be exposed. Third-party certifications also affirm these products’ capabilities to withstand pressure, temperature variation, and chemical exposure. This level of commitment to quality assures plant managers and engineers of their decision to adopt FRP as a key component in their systems.
In summary, FRP fittings represent a significant advancement in materials technology, offering advantages that are both practical and economic. Their adoption is fueled by clear benefits in reducing maintenance costs, improving system longevity, and ensuring resistance to aggressive environments. Professionals in industries reliant on piping and fluid transfer systems are increasingly choosing FRP fittings over traditional materials due to their unrivaled performance attributes, thus setting a new standard in industrial applications.