FRP flanges and blinds have risen to prominence across various industries due to their remarkable properties and versatility. Crafted from Fiber Reinforced Plastic, these components are increasingly replacing traditional materials like steel and aluminum due to their lightweight and corrosion-resistant nature.
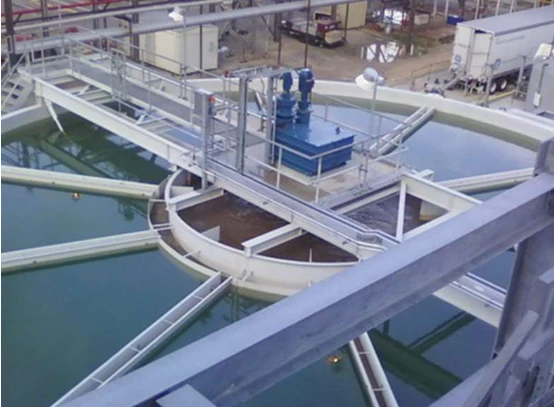
In industrial applications where corrosive substances are prevalent, FRP flanges offer a substantial advantage. The intrinsic properties of FRP materials negate the need for additional coatings or treatments to prevent corrosion, thereby reducing maintenance costs and prolonging equipment lifespan. Industries such as chemical processing, wastewater treatment, and marine sectors have witnessed significant cost savings and operational efficiencies by transitioning to FRP flanges.
One key feature of FRP flanges is their impressive strength-to-weight ratio. Unlike metal alternatives, FRP does not succumb to rust or deteriorate under constant exposure to environmental stressors and chemicals, which is crucial for long-term durability and reliability. This characteristic ensures that infrastructure using FRP components remains safe and reliable over the years, positioning FRP as a trusted material in safety-critical applications.
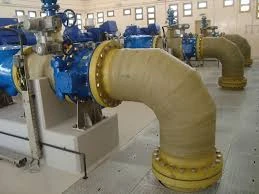
Furthermore, the installation of FRP flanges is straightforward due to their lightweight nature, which reduces labor costs and time during the setup process. The ease of handling and installation is particularly beneficial in projects with tight timelines or those located in remote areas where transportation of heavy materials poses a significant challenge.
For those considering FRP blinds, the benefits are equally tangible. These components are crucial for temporarily sealing pipelines or vessels during maintenance or in case of emergencies. The strength and resilience of FRP blinds ensure a secure fit, preventing leaks that could lead to environmental hazards or operational downtimes.
frp flange and blind
From an expertise perspective, selecting FRP flanges and blinds should be guided by a comprehensive understanding of the specific operational environment and stress conditions. Consulting with manufacturers who specialize in FRP technology can provide invaluable insights into the appropriate specifications suited to individual project needs.
Authorities in the field, such as chemical engineers and compliance inspectors, endorse the use of FRP components given their proven track record in enhancing safety and efficiency. Adopting FRP materials is a step towards sustainable engineering practices, aligning with modern sustainability goals without compromising on performance.
Trust in the reliability of FRP products stems from rigorous quality control measures adhered to in their manufacturing process. Reputable suppliers conduct exhaustive testing to ensure that each FRP flange and blind meets stringent industry standards and client specifications, reinforcing their dependability in critical applications.
In conclusion, the adoption of FRP flanges and blinds represents an intersection of advanced material science and practical engineering solutions. Their robust properties not only lead to significant lifecycle cost savings but also align with the increasing demand for eco-friendly and efficient infrastructure development. Embracing FRP technology not only addresses current industry challenges but also prepares businesses for future advancements, ensuring they remain competitive in an evolving marketplace.