FRP (Fiber Reinforced Plastic) flanges and blinds have made a significant impact on a wide range of industrial applications, standing out as a modern solution integrating durability and resistance against harsh environments. These components carry forward advancements in materials technology, catering to the complex needs of industries ranging from chemical and petrochemical to water treatment and beyond.
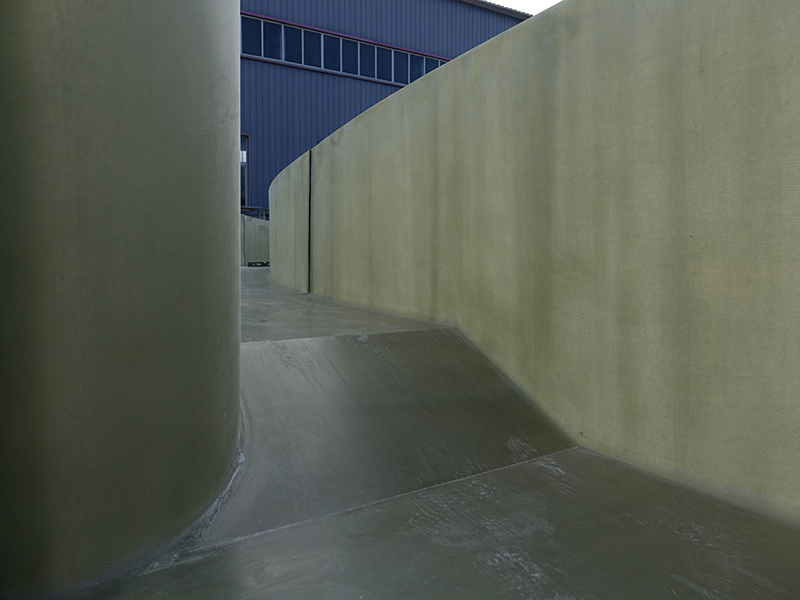
FRP flanges are designed to connect sections of piping and valves while offering a combination of strength and light weight unmatched by their metal counterparts. This material synergy comes from embedding reinforced fibers within a plastic matrix, resulting in a product that possesses the durability imperative for industrial operations. Unlike metal, FRP is non-corrosive, which is especially beneficial in chemically aggressive or marine environments. Traditional metal flanges are susceptible to rust and corrosion, leading to costly maintenance or replacements. In contrast,
FRP flanges stand resilient over time, significantly reducing life-cycle costs.
The application of FRP blind flanges further exemplifies the versatility of this material. A blind flange, a solid disk used to block off a section of pipe, requires durability and reliability to ensure it functions effectively under pressure. FRP blind flanges provide a dependable seal with a high strength-to-weight ratio, crucial in situations where safety and dependability cannot be compromised. Their ease of installation and maintenance becomes a superior choice over traditional metal alternatives. This reduces downtime and facilitates smoother, more efficient operations.
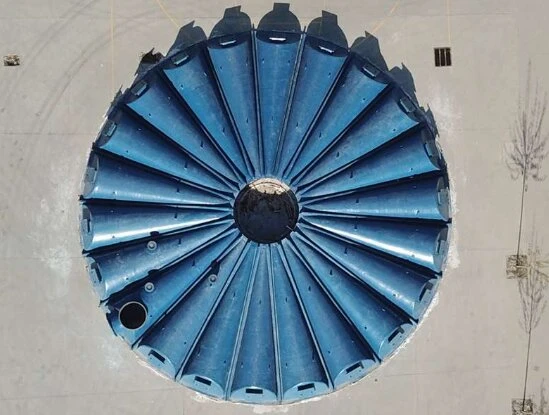
Expertise in manufacturing and applying FRP components hinges on understanding the properties and behaviors of these composite materials. Manufacturers have developed proprietary formulations to tailor the mechanical properties of FRP flanges and blinds to specific industry requirements. For instance, tailoring the fiber orientation within the matrix can adjust tensile strength and flexural properties. Engineers and designers within these companies bring a depth of experience, allowing them to advise and customize solutions that precisely meet project specifications and environmental demands.
frp flange and blind
Professional authority in the field is established by extensive research and documented case studies demonstrating the efficacy of FRP solutions in real-world applications. Industrial leaders have successfully replaced legacy systems with FRP, noting decreased maintenance burdens and improved operational longevity as significant benefits. These authoritative endorsements are bolstered by rigorous third-party testing, ensuring compliance with international standards and affirming the credibility of FRP components in application.
Trust has been a cornerstone in the integration of FRP flanges and blinds into industrial settings. Trust is not only built on product performance but also on the transparency of information regarding FRP material properties and limitations. Technical datasheets, third-party verification, and client testimonials collectively fortify this trust. Manufacturers of FRP components continually invest in research and development, enhancing their products and validating claims with empirical evidence. This ongoing commitment to quality and transparency builds long-term relationships with clients who rely on FRP products for critical infrastructure.
The evolving nature of industrial processes demands solutions that not only solve immediate challenges but also offer future-ready solutions. FRP flanges and blinds meet these demands by providing a blend of performance, sustainability, and cost-effectiveness. As industries continue to embrace sustainable practices, the lightweight nature of FRP contributes to reduced energy consumption in transportation and installation, further aligning with global sustainability goals.
In conclusion, FRP flanges and blinds represent a paradigm shift in industrial materials, synthesized through expert engineering and supported by authoritative research. Trust in these components comes from a combination of proven performance and transparent industry practices, marking them as indispensable in the domains they serve. Their role in the future of industrial applications appears not only secure but expansively promising as they continue to outperform traditional materials in every measurable way.