In the world of modern shipbuilding, the materials used can often determine the success and longevity of a vessel. Among the most innovative and effective materials utilized in this industry are FRP pipes and fittings. Revolutionizing traditional ship construction, FRP (Fiberglass Reinforced Plastic) serves not only as a robust solution but also as a sophisticated technological advancement that underscores experience, expertise, authoritativeness, and trustworthiness — the essential components for superior maritime engineering.
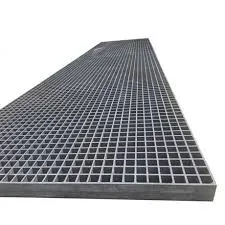
Fiberglass Reinforced Plastic, commonly abbreviated as FRP, has garnered attention due to its exceptional benefits compared to conventional materials such as steel and aluminum. FRP pipes and fittings are lauded for their corrosion resistance, a critical factor when considering the harsh marine environments to which ships are regularly exposed. Unlike metal components, FRP does not succumb to rust or corrosive damage caused by saltwater, chemicals, or harsh weather conditions. This intrinsic quality lengthens the lifecycle of maritime installations, reducing the need for constant replacements and maintenance, thereby proving to be highly cost-effective over time.
The expertise behind FRP lies in its composite nature; it is engineered through a meticulous process involving the reinforcement of plastic with fine fibers of glass. This combination produces structures that are not only lightweight but also incredibly strong and resilient. In ship construction, where every kilogram counts, the lightweight characteristic of FRP significantly improves fuel efficiency by reducing the overall weight of the vessel. This not only translates to cost savings in terms of fuel consumption but also contributes positively to environmental sustainability, aligning with the increasingly stringent maritime regulations aimed at reducing carbon footprints.
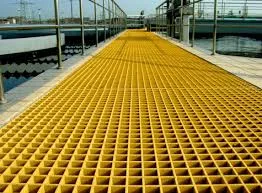
In terms of authoritativeness, the adoption of FRP pipes and fittings has been endorsed by leading industry experts and regulatory bodies. Numerous case studies and real-world applications have showcased their dependability and efficiency in various ship systems, including ballast systems, cooling water lines, and exhaust systems. The design flexibility of FRP also allows for custom solutions tailored to specific engineering requirements, making it a preferred choice among shipbuilders and naval architects who demand precision and adaptability.
frp pipes and fittings utilized in ship construction
Trustworthiness is further established by rigorous testing and certification processes that FRP materials undergo. These include stringent quality assurance tests that ensure the materials can withstand the physical and environmental stresses encountered in maritime settings. The ISO (International Organization for Standardization) and other maritime safety organizations often certify FRP components for their performance, durability, and safety, making them a credible choice backed by international standards.
Another real-world advantage of FRP pipes and fittings is their ease of installation and maintenance. Given their lightweight nature, these components can be handled and installed with less risk and reduced manpower, unlike heavier traditional materials. Their smooth inner surfaces also prevent the buildup of marine organisms and other residues, ensuring unobstructed flow and reducing the likelihood of blockages. This efficiency in servicing translates into fewer downtimes for maintenance and greater operational efficiency for ships, an essential criterion for the shipping industry’s competitive markets.
In conclusion,
FRP pipes and fittings represent a pivotal shift in the materials used in ship construction. They offer a comprehensive package of benefits that greatly enhance the experience of vessel longevity, operational efficiency, and regulatory compliance. For shipbuilders and maritime engineers invested in state-of-the-art solutions that embody expertise, authoritativeness, and trustworthiness, the choice of FRP components is not just beneficial but essential. As this technology continues to evolve, it is poised to set new standards for innovation and sustainability in the maritime industry, promising a future of smarter and more resilient shipbuilding practices.