Fiberglass Reinforced Plastic (FRP) products are revolutionizing the steel smelting industry through their unique blend of durability, lightweight nature, and exceptional corrosion resistance. As steel smelting plants continue to encounter challenges such as extreme temperatures, chemical exposure, and the necessity for reliable infrastructure, the deployment of FRP products offers a game-changing solution with tangible, long-term benefits.
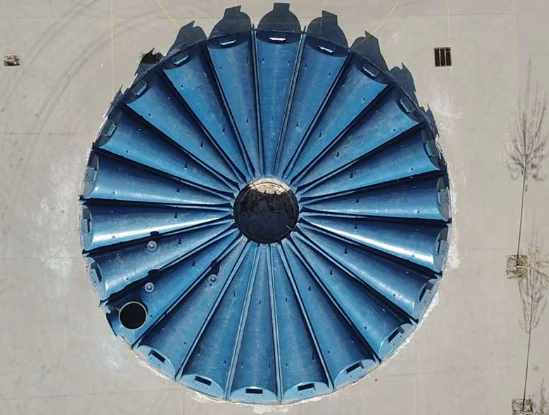
FRP, comprising a polymer matrix reinforced with fibers, most typically glass, addresses some of the critical issues faced by traditional materials like steel and concrete. In the demanding environment of a steel smelting plant, where maintenance costs can skyrocket due to frequent repairs of corroded structures, FRP products stand out with their inherent corrosion-resistant properties. They can withstand harsh chemical exposures without the degradation typically associated with metal components. This characteristic significantly prolongs the lifespan of infrastructure and reduces the need for constant maintenance, leading to marked savings in plant operation budgets.
Another significant advantage of FRP is its lightweight nature. In an industry where heavy-duty equipment and innately heavy materials are the norms, the reduced weight of FRP components, such as grating, tanks, and ducts, translates to easier handling and installation. This can lead to a decrease in labor costs and faster project completion times, without compromising on the quality and robustness required in heavy industrial settings. Moreover, unlike traditional materials, FRP doesn’t require heavy lifting equipment for installation, further reducing overall project expenses and increasing operational efficiency.
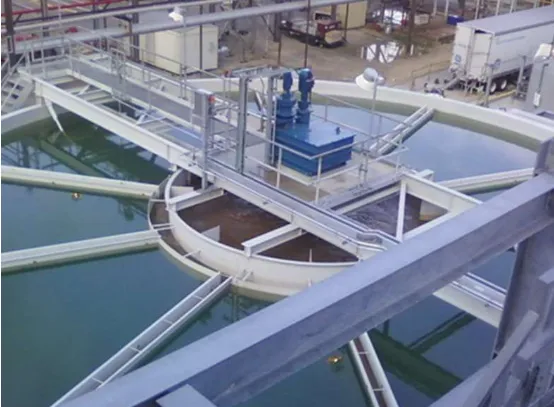
When examining the thermal efficiency of FRP products, it becomes evident why they are becoming a preferred choice in steel smelting environments. FRP's low thermal conductivity offers substantial energy savings, as it minimizes heat loss in plant operations where maintaining precise temperature control is vital. Additionally, FRP products remain stable under high and low temperatures, maintaining their structural integrity and performance where other materials might fail. Their ability to endure thermal cycling without cracking or warping makes them ideally suited for the fluctuating temperatures typical in smelting operations.
From an expertise lens, the manufacturing process of FRP products allows for a high degree of customization, enabling the creation of bespoke solutions tailored to the specific needs of steel smelting plants. This can include the production of uniquely shaped components or the integration of additional functional features such as flame retardancy or enhanced UV resistance. The versatility of FRP makes it the go-to material for plant designers seeking a harmonious blend of practicality and innovation.
frp products for steel smelting plant
Establishing trustworthiness and reliability, FRP products align with stringent industry standards and certifications, which are crucial in maintaining operational safety and compliance. With each product meticulously tested to ensure it meets safety and performance standards, plant managers can be confident in the integrity of their infrastructure. Providers of FRP products are often recognized for their commitment to research and development, continuously improving their offerings to meet the evolving demands of the industry.
Authoritativeness is underscored by the broad adoption of FRP components across various heavy industries beyond steel smelting, illustrating their wide acceptance and proven track record. Their application in environments such as chemical plants, offshore platforms, and wastewater treatment facilities further validates their effectiveness and reliability under the most demanding conditions.
Real-world experiences back the burgeoning use of FRP in steel smelting. Case studies report significant reductions in maintenance downtime and total cost of ownership when integrating FRP solutions. Plant operators consistently praise the material’s resilience, low maintenance requirements, and the enhanced safety it brings due to its non-conductive properties, reducing the risk of electrical hazards in an already perilous industrial environment.
The shift towards incorporating FRP products in steel smelting plants reflects a broader industry trend prioritizing sustainable and cost-effective solutions. As industries strive to reduce their environmental footprint, the non-corrosive nature of FRP, which minimizes chemical leaching, alongside its potential for recycling, positions it as a forward-thinking option aligning with global sustainability goals.
In summary,
FRP products are not just a fleeting trend but a transformative force in steel smelting plant operations. By addressing traditional material deficiencies and delivering on performance, cost efficiency, and safety, FRP embodies the very principles of modern industrial engineering—paving the way for the future of infrastructure in steel smelting and beyond.