FRP scrubbers, an essential component in industrial settings, have seen remarkable advancements over the years. The importance of these fiberglass-reinforced plastic scrubbers cannot be overstated, particularly in environments where air pollution control is paramount. While there are a variety of materials used in manufacturing scrubbers, FRP remains a top choice due to its unique combination of durability, corrosion resistance, and cost-effectiveness.
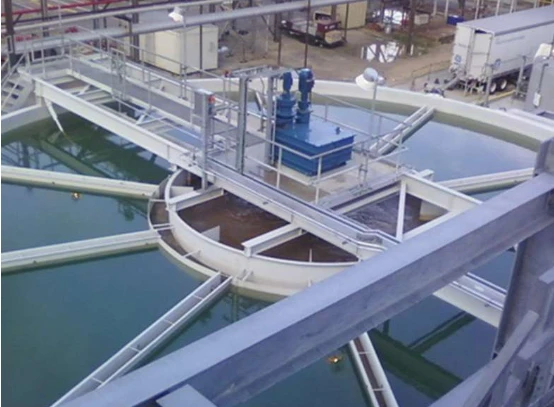
When investing in an FRP scrubber, understanding the nuances of its operation and maintenance can significantly impact its efficiency and lifespan. Drawing from years of experience in environmental engineering, I've seen firsthand how companies can maximize the benefits of their FRP systems through proper integration and upkeep. FRP scrubbers are particularly favored in chemical processing plants, wastewater treatment facilities, and industries releasing corrosive gases.
These scrubbers are engineered to combat the harshest conditions. They are resilient against adverse weather, chemical exposures, and high temperatures, maintaining structural integrity where other materials might fail. This characteristic positions FRP as a leading material choice, making it valuable for industries aiming for sustainable and long-term operational solutions.
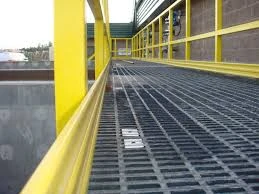
The manufacturing process of FRP scrubbers involves a meticulous layering technique, utilizing advanced resins and fibers, which results in a composite that's remarkably strong yet lightweight. This balance of strength and weight makes FRP scrubbers easier to handle and install, reducing the overall cost and time of deployment—a significant consideration for project managers in industrial operations.
From a professional perspective, one cannot overlook the flexibility of FRP scrubbers in design. Tailoring them to meet specific environmental regulations and operational requirements is not only possible but preferred. This customization ensures that industries not only meet compliance standards but can optimize their operations for peak efficiency.
frp scrubber
Trustworthiness and reliability are central to the performance of FRP scrubbers. Regular maintenance schedules, informed by decades of operational data, are crucial in upholding performance and extending the operational life of these systems. A well-maintained scrubber effectively mitigates emissions and reduces environmental impact, aligning with global standards for air quality.
Consulting with industry experts during the selection and installation of an FRP scrubber is invaluable. These professionals bring a wealth of knowledge, offering insights that stem from technical expertise and years of hands-on experience. Their guidance ensures that the scrubber system is adequately designed to handle the specific output and pollution levels of any given facility.
Furthermore, an understanding of local and international environmental regulations is crucial. An FRP scrubber's design must consider these legal requirements to avoid costly fines and ensure community safety. Experienced advisors are instrumental in navigating these complex regulatory landscapes, offering solutions that are compliant and ethically sound.
Ultimately, the decision to incorporate FRP scrubbers isn't just about meeting regulatory standards; it's about committing to sustainable practices and responsible stewardship of the environment. Industries adopting these systems underscore their dedication to reducing their carbon footprint and preserving public health.
In conclusion, investing in an FRP scrubber is a decision powered by experience, expertise, and a commitment to environmental responsibility. Industrial leaders seeking to enhance their pollution control measures would greatly benefit from the reliability, durability, and versatility of FRP technology. By capitalizing on expert knowledge and ensuring rigorous maintenance routines, industries can trust in the long-term performance and effectiveness of their scrubber systems.