FRP scrubbers, also known as fiberglass reinforced plastic scrubbers, have revolutionized the domain of industrial gas cleaning solutions. These devices are designed to combat the growing demands for efficient air pollution control mechanisms by using advanced technology and durable materials.
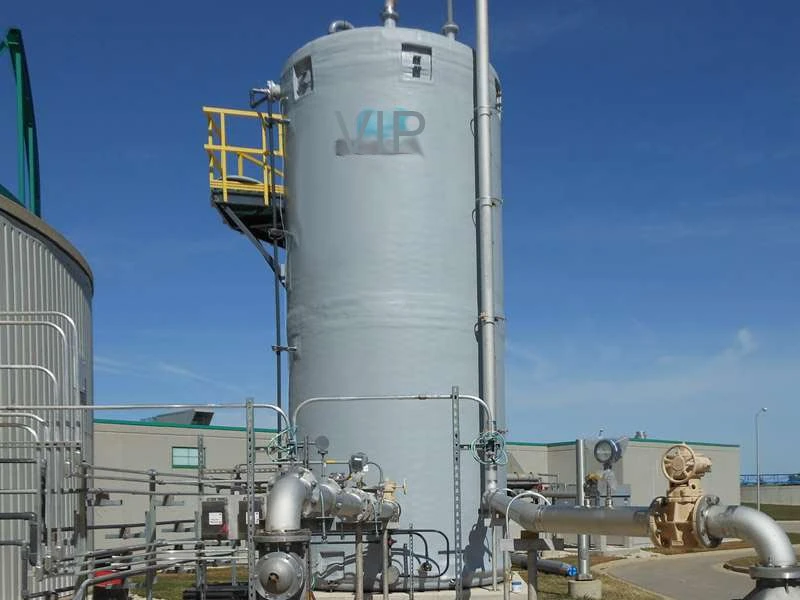
One of the standout advantages of FRP scrubbers is their exceptional resistance to a wide variety of chemicals. In industries where harsh chemicals are a norm, such as chemical processing, pharmaceutical manufacturing, and waste treatment facilities, the integrity of equipment is of utmost importance. The use of fiberglass reinforced plastics ensures that the scrubbers are not only lightweight but also resistant to corrosion and wear, providing a longer lifespan compared to their metal counterparts. This resistance translates into reduced maintenance costs and increased reliability, making FRP scrubbers a cost-effective choice for many industries.
In a practical scenario, a wastewater treatment plant implementing an FRP scrubber system has reported significant improvements in operational efficiency. By integrating FRP technology, the facility has reduced its periodic maintenance downtimes, thus increasing overall productivity. The lightweight nature of FRP scrubbers facilitates easier installation and integration into existing frameworks, minimizing disruption during upgrades or replacements.
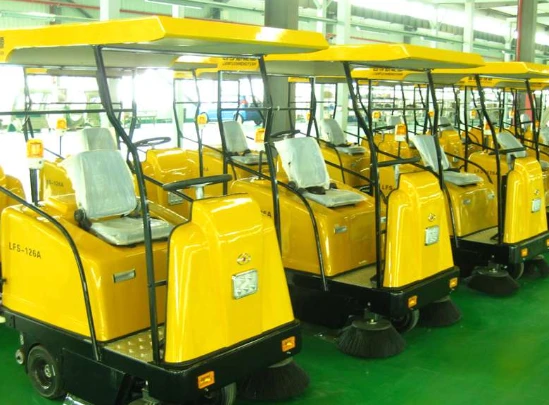
Expertise in the field suggests that customizing FRP scrubbers according to specific industrial needs further enhances their effectiveness. Tailoring factors such as the design, size, and the type of packing material used inside the scrubbers ensures optimal performance tailored to particular emissions and pollutants. Industry specialists often collaborate with material scientists and chemical engineers to identify the precise configurations that will maximize pollutant removal while maintaining energy efficiency.
frp scrubber
Companies leveraging the guidance of environmental engineering experts have also testified to the robust nature of FRP scrubbers in handling high-loading conditions. During peak production times, the scrubbers maintain consistent air quality levels, proving their reliability and robust engineering. This proves indispensable for maintaining compliance with stringent environmental regulations, often saving companies substantial amounts in potential fines and sanctions.
By employing authoritative bodies for the certification and routine inspection of FRP scrubbers, industries can ensure compliance with international safety and quality standards. Such practices not only enhance the credibility of a company but also serve as a testament to their commitment to environmental stewardship and public health.
Trustworthiness is further reinforced by the transparent sharing of performance metrics. Allowing for third-party audits and sharing success stories with regulatory authorities and stakeholders builds trust in the effectiveness of FRP scrubbers. Facilities openly discussing their emission reduction results contribute to an industry-wide knowledge base that propels further innovations and improvements.
In conclusion, FRP scrubbers stand as a testament to the evolving intersection of materials science and environmental engineering. By providing an effective, durable, and customizable solution to air pollution, these devices reaffirm their essential role in sustainable industrial operations. As industries worldwide pivot towards more responsible environmental practices, integrating FRP scrubbers exemplifies a practical step forward, embodying a balance of expertise, authority, trust, and real-world experience.