FRP (Fiberglass Reinforced Plastic) step systems represent a revolutionary shift in ensuring safety while maintaining functionality in various construction and industrial applications. Unlike traditional materials such as wood or steel, FRP combines durability with lightweight properties, making it an optimal choice for environments where corrosion, chemical exposure, and safety are primary concerns.
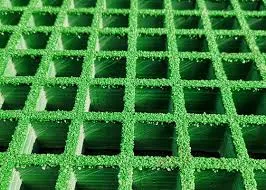
One substantial advantage of FRP steps is their exceptional resistance to harsh environmental conditions. In maritime settings, where saltwater and humidity are prominent foes to metals, FRP steps demonstrate unparalleled performance. They do not corrode, ensuring the longevity and reliability of the structures they support. This makes them a superior choice for offshore platforms and docks, embodying the essence of durability.
Furthermore, FRP steps are lauded for their anti-slip characteristics. They are designed with specific surfaces that reduce the risk of slips and trips, thereby enhancing workplace safety, which is particularly crucial in wet and oily conditions commonly found in industrial plants. Safety managers and engineers frequently praise this feature, emphasizing how it aids in mitigating potential on-site accidents, consequently reducing liability and enhancing workforce confidence.
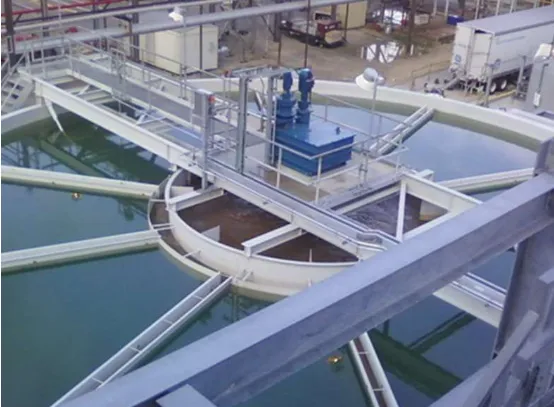
The lightweight nature of FRP adds a layer of practical utility not found in heavier materials. This characteristic eases the installation process significantly. Unlike steel or concrete, which requires substantial manpower and machinery to maneuver, FRP can be installed using minimal equipment and manpower, resulting in substantial cost savings. Construction projects benefit distinctively from reduced installation times and labor costs, making it an economically viable option for large-scale deployments.
In addition to their functional attributes, FRP steps are designed to meet rigorous fire safety standards. They exhibit excellent fire retardancy, which is a critical requirement in many industries where fire hazards are a concern. This quality extends its applicability to sectors such as chemical plants and manufacturing facilities, where maintaining high safety standards is imperative.
frp step
Moreover, from a sustainability perspective, FRP steps contribute positively to environmental goals. As industries aim to minimize their carbon footprint, the manufacturing process of FRP involves lower emissions compared to more traditional materials. Companies that adopt FRP steps are therefore able to align themselves with environmental conservation efforts, showcasing a commitment to sustainable practices that resonate with today's eco-conscious consumers and stakeholders.
Organizations that adopt FRP steps also experience a reduction in maintenance costs. While steel and wood structures often demand regular treatment or replacement due to wear and damage, FRP's robustness means fewer repairs and longer intervals between maintenance cycles. Over time, this reduces the total cost of ownership, freeing up financial resources that can be allocated to other critical operational needs.
Expert opinions consistently highlight the adaptability of FRP steps to various customizations, meaning they can be tailored to customer-specific requirements without compromising their inherent qualities. Whether it’s a particular color for aesthetic coherence or precision engineering for specific industrial applications, FRP provides a flexible solution that meets diverse needs.
In conclusion, FRP steps manifest a combination of innovative engineering, sustainability, and safety, establishing themselves as the future-standard for infrastructures facing demanding environmental and safety challenges. For industries stepping towards future resiliency and efficiency, the integration of FRP systems represents not just an upgrade, but a strategic investment. This investment enhances operational efficiency while safeguarding employee well-being and supporting environmental stewardship—a testament to progress in modern construction and industrial design.