Fiber Reinforced Plastic (FRP) tanks are revolutionizing industries across the globe by offering an unparalleled combination of durability, versatility, and cost-effectiveness. Over the past decades, these tanks have become essential in fields such as chemical processing, wastewater management, and agricultural storage, largely due to their unique properties which surpass those of traditional materials like steel or concrete.
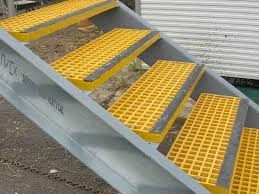
In the realm of chemical processing, the outstanding corrosion resistance of FRP tanks makes them a superior choice. These tanks are constructed using high-quality, corrosion-resistant resins that can withstand aggressive chemicals which typically cause rapid degradation in metal counterparts. This property not only prolongs the service life of the tanks but reduces the need for costly maintenance and potential downtime, ensuring that operations remain smooth and uninterrupted.
Experienced operators often report significant cost savings and enhanced operational efficiency after switching to FRP tanks.
The expertise involved in manufacturing FRP tanks is profound, calling for a specific blend of materials and skilled craftsmanship. The manufacturing process involves layering reinforced fibers with thermosetting resins, which are then cured under specific conditions to achieve unparalleled structural integrity. This expertise ensures that each tank is designed to meet specific pressure, temperature, and chemical exposure demands, while also adhering to rigorous safety standards. Leading manufacturers guide this process with precision, backed by years of engineering prowess and technological advancement, ensuring the highest levels of safety and performance.

The authoritativeness of FRP tanks can be further recognized by their increasing acceptance and specification in international industry standards. Organizations such as the American Society for Testing and Materials (ASTM) and the International Organization for Standardization (ISO) have established comprehensive guidelines that govern the design, manufacturing, and testing of FRP tanks. Compliance with these standards is a testament to the tanks’ reliability and the trust that industry leaders place in them to store and manage valuable and hazardous products.
frp tank
Trustworthiness in the industry is garnered through continuous innovation and proven performance in real-world applications. Companies using FRP tanks often benefit from reduced insurance premiums due to their enhanced safety profile, which emanates from their inherent fire retardant properties and the electrical non-conductivity of fiberglass. Furthermore, the lightweight nature of FRP facilitates easier transport and installation, reducing initial setup costs and lowering transportation-related emissions, which resonates with companies aiming for sustainable practices.
For industries with specialized needs, such as food processing or potable water storage, FRP tanks offer solutions that meet stringent hygiene standards. They can be equipped with smooth inner linings that resist bacterial growth, ensuring that contents remain uncontaminated. This makes FRP tanks a trusted choice across sectors where safety and quality are non-negotiable.
In conclusion, FRP tanks stand out in the market due to their unmatched ability to offer durability, safety, and cost efficiency. These attributes are backed by genuine industry experience, cutting-edge manufacturing expertise, and a solid track record of dependability. As industrial needs continue to evolve, the adoption of FRP tanks is likely to expand, driven by their proven advantages and compliance with global safety standards. Businesses choosing FRP tanks today make a long-term investment in performance and peace of mind, trusting in their proven capability to protect and preserve valuable resources.