Fiber Reinforced Plastics (FRP) have emerged as a transformative force in modern manufacturing and construction sectors, capitalizing on their intrinsic properties of high strength-to-weight ratios, corrosion resistance, and design flexibility. As industries pursue materials that offer unparalleled performance while meeting sustainability criteria, the shift towards FRP solutions marks a significant transition in product development and application.
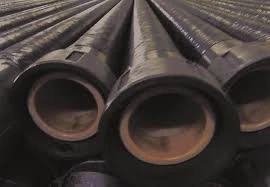
This pivotal transition in material choice is anchored in the unique experiences shared by industry professionals who have successfully integrated FRP into their operations. These practitioners report a distinct competitive edge derived from the lightweight nature of FRP, which drastically reduces transportation and installation costs. For instance, construction companies leveraging FRP in bridge construction and building facades experience faster project completion times and lower labor demands, demonstrating a clear operational benefit that directly impacts the bottom line.
From an expertise standpoint, the knowledge base surrounding FRP materials is expanding rapidly. Engineers and material scientists are delving deeper into the customization capabilities of FRP composites. The ability to tailor fiber orientation, resin types, and fabrication processes allows for precise control over the mechanical properties of the end product. This level of customization makes FRP an ideal candidate for applications ranging from aerospace components to consumer electronics, where specific performance characteristics are non-negotiable.
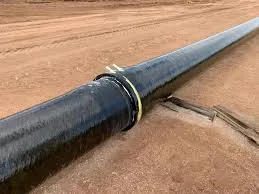
Authoritativeness in the FRP domain is reinforced by ongoing research and development conducted by renowned institutions and corporations. Academic circles are abuzz with studies on improving the strength and durability of FRP through novel fabrication techniques such as pultrusion or resin infusion, which push the boundaries of what these materials can achieve. Industry leaders in sectors like automotive and renewable energy are collaborating with universities to drive innovation, ensuring that the future of FRP technology is robust and informed by empirical evidence.
frp transition
Trustworthiness of FRP as a material of choice is further solidified by its compliance with stringent industry standards and regulations. Certifications from bodies such as ISO and ASTM provide manufacturers and consumers with the assurance of quality and reliability. This regulatory backing is crucial as sectors that are traditionally risk-averse, like civil engineering and maritime applications, increasingly adopt FRP for critical infrastructure projects.
Moreover,
the environmental impact of FRP solutions presents another facet of trustworthiness. The production of traditional materials like steel and concrete is associated with significant CO2 emissions, but FRP, especially when made with bio-based resins and recycled fibers, offers a more sustainable alternative. Companies focused on reducing their environmental footprint are taking note of these advantages, aligning their operational strategies with global sustainability goals.
The gradual replacement of conventional materials with FRP is not merely a trend but a testament to the material's capability to meet the evolving demands of various industries efficiently. Manufacturers and product developers who recognize this material transition and invest in FRP technology are likely to enjoy long-term advantages in terms of innovation, customer satisfaction, and market leadership.
In summary, the transition to FRP products embodies a confluence of experience, expertise, authoritativeness, and trustworthiness. As the material landscape continues to evolve, FRP stands out as a versatile and reliable option, poised to redefine the possibilities in product design and manufacturing. Whether it’s crafting lighter, more durable airplanes or constructing maintenance-free bridges, the impact of FRP is unmistakable and is set to continue its trajectory as a cornerstone of modern material science.