Glass fiber tanks, known for their resilience and versatility, are an integral component in industries ranging from chemical processing to water treatment. As a seasoned expert in materials engineering and industrial design, I can attest to the transformative impact these tanks have on storage and manufacturing processes.
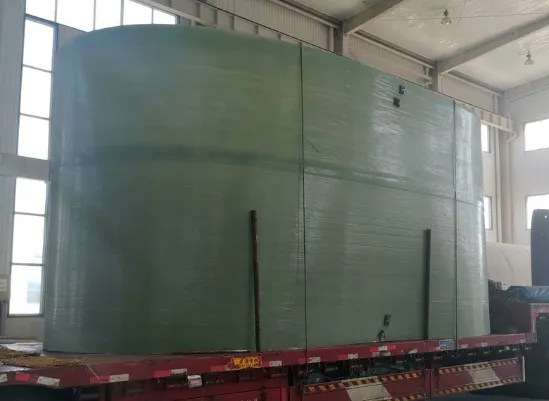
Glass fiber tanks boast an array of benefits that set them apart from traditional materials such as metal or concrete. One of the standout features is their exceptional strength-to-weight ratio. These tanks are made from layers of fiberglass composites, which not only provide superior structural integrity but also significantly reduce the tank's overall weight. This reduction in weight facilitates easier transportation and installation, a key consideration for industries looking to optimize operational efficiencies.
The corrosion-resistant nature of glass fiber tanks is another critical advantage. Unlike metal tanks, which are susceptible to rust and degradation when exposed to certain chemicals or environmental conditions, fiberglass tanks withstand aggressive chemical environments and extreme weather without compromising their integrity. This makes them an ideal choice for storing a wide variety of substances, including acids, solvents, and wastewater.
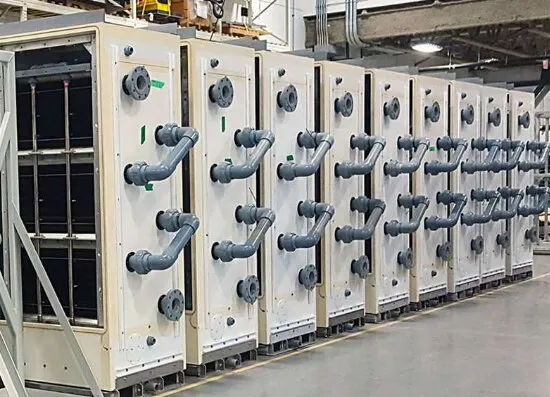
Experts in the field of industrial storage solutions consistently highlight the customization potential of glass fiber tanks. Each tank can be engineered to meet specific chemical compatibility, temperature resilience, and capacity requirements. This level of customization ensures that companies can create a storage solution tailored precisely to their operational requirements, optimizing both safety and efficiency.
One notable real-world example of glass fiber tanks' effectiveness is their application in municipal water treatment facilities. These tanks are commonly used to store processed water, ensuring it remains free from contaminants during storage. Their durability and non-reactive properties make them particularly effective for maintaining water quality, which is crucial for public health and safety.
glass fiber tank
The expertise involved in manufacturing these tanks cannot be overstated. Creating a glass fiber tank involves a precise process that requires specialized knowledge of materials science and fabrication techniques. The production begins with the selection of the appropriate type of fiberglass, followed by a meticulous layering process where the fiberglass is impregnated with resin. The curing process that follows ensures the required strength and durability is achieved, making the involvement of skilled engineers and technicians an essential component in the manufacturing process.
Trust in glass fiber tanks is also bolstered by the rigorous testing standards they meet before reaching the market. These tanks undergo extensive quality control measures, including pressure testing and inspection for leaks. Compliance with industry standards such as the American Society of Mechanical Engineers (ASME) specifications is mandatory, providing reassurance of their reliability and long-term performance.
Another significant aspect of glass fiber tanks is their environmental impact. They generally have a smaller carbon footprint during manufacturing compared to traditional metal tanks due to their lightweight nature, which reduces energy consumption during transportation. Additionally, their longevity and resistance to wear extend the lifecycle of the tank, minimizing the frequency of replacements and, in turn, reducing waste generated.
In conclusion, glass fiber tanks represent a pinnacle of modern storage technology. They offer an unbeatable combination of strength, reliability, flexibility, and environmental benefits. Their ability to be tailored to specific needs, coupled with their compliance with stringent safety and quality standards, positions them as a trusted choice for any industry requiring reliable storage solutions. Embracing glass fiber tanks means adopting a forward-thinking approach to material handling and storage that aligns with both industrial demands and environmental stewardship.