In the evolving landscape of global commerce,
the demand for GRP (Glass Reinforced Plastic) customized products has surged remarkably. Industries are consistently seeking innovative materials that not only promise durability but also offer flexibility in customization. GRP customized products have emerged as a frontrunner, catering to diverse industry needs from automotive to construction, and even aerospace. This article explores the niche market of GRP customized products, focusing on its unique advantages, application expertise, engineering authority, and trusted implementations across various sectors.
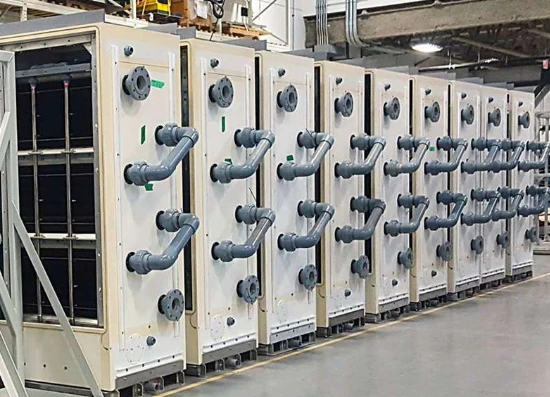
GRP, a composite material made of plastic reinforced with fine glass fibers, stands out due to its exceptional strength-to-weight ratio. This intrinsic property makes GRP an ideal choice for customization projects that require both durability and lightweight features. Unlike metals, GRP resists corrosion, which is a significant advantage in industries exposed to harsh environmental conditions. Manufacturers and engineers can trust in GRP's longevity and performance, enabling them to design products that meet specific client requirements without compromising on quality or functionality.
One of the distinct experiences with GRP customization is its versatility. Whatever the industry, GRP products can be tailored in terms of shape, texture, and color, thanks to advanced molding processes. This customization capability supports innovative design solutions, making these products especially valuable in applications such as bespoke vehicle body panels, tailored water storage solutions, and unique architectural features. Each design can be refined to precise specifications, ensuring every custom GRP product serves its intended purpose flawlessly, a testament to both material expertise and engineering skill.
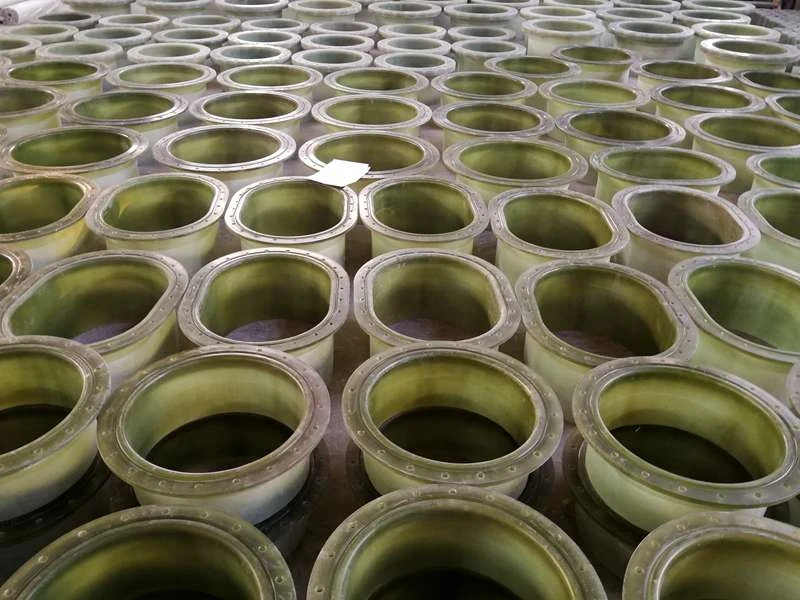
The expertise involved in the creation of GRP customized products extends beyond mere craftsmanship; it encompasses a deep understanding of material science and engineering principles. Professionals working with GRP must possess a nuanced knowledge of its properties to manipulate and mold it effectively. This includes understanding thermal expansion coefficients, the significance of fiber orientation, and how these factors influence the final product's performance. Investing in GRP not only involves selecting a material but also choosing a pool of expert craftsmen and engineers who understand the science and art behind GRP customization.
grp customized product
Authoritativeness in GRP products is established through rigorous industry standards and certifications that these products often meet or exceed. Trusted manufacturers adhere to these standards, ensuring the resultant customized products not only fulfill client expectations but also comply with industry regulations. This credibility is crucial in sectors where material failure is not an option, such as in aviation or maritime transport. Here, the confidence in GRP products' reliability and authority translates directly into enhanced safety and operational efficiency.
Trustworthiness, another critical pillar of GRP product use, is cemented through long-standing industry partnerships and successful project deliveries. Companies involved in GRP product customization prioritize building lasting relationships with their clients, ensuring transparency in processes, timelines, and materials used. Furthermore, testimonials and case studies from satisfied clients often reinforce trust. These documented instances of successful custom GRP applications highlight the products' robustness and the manufacturers’ commitment to quality assurance and client satisfaction.
Navigating the market of GRP customized products demands a comprehensive understanding of potential applications and the ability to innovate consistently. As more industries realize the benefits of customizable solutions that GRP offers, the onus lies on manufacturers and suppliers to maintain high standards of expertise, authority, and trustworthiness. By doing so, they not only contribute to their industry's growth but also drive forward the adoption of this remarkable material across new and exciting applications.