GRP grating, or glass reinforced plastic grating, has emerged as a game-changer in industries where durability, safety, and maintenance are paramount. In situations where metal grating may corrode or heavy materials are impractical, GRP grating stands out as a superior alternative. This article breaks down the essential attributes of GRP grating, offering insights into its applications, benefits, and considerations, fortified by real-world experiences and expert evaluations.
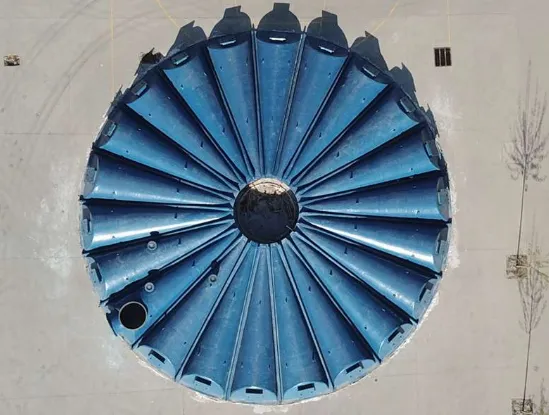
GRP grating is woven with glass fibers and thermosetting resin, creating a strong yet lightweight material. This composition is resistant to corrosion, making it ideal for environments exposed to moisture and chemicals, such as wastewater treatment plants, marine applications, and chemical factories. Unlike steel, which can rust and require ongoing maintenance, GRP grating maintains its structural integrity over time, resulting in lower lifecycle costs.
Professionals in the field note the tremendous ease of installation associated with GRP grating. Given its lightweight nature, it can be transported and installed without the need for heavy lifting equipment, reducing labor costs and installation time. For industries like petrochemical plants, where downtime translates to lost revenue, GRP grating’s quick installation process is a crucial advantage.
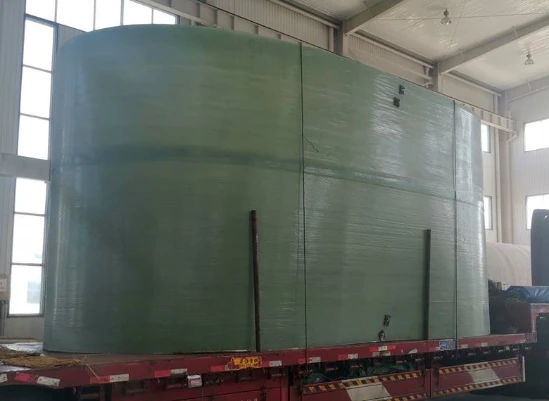
Safety is another domain where GRP grating excels. The anti-slip surface of GRP grating is particularly beneficial in environments prone to spills or wet conditions, as it significantly reduces the likelihood of workplace accidents. An industry expert from a leading offshore drilling company highlights that after replacing traditional metal grating with GRP grating, incidents related to slips and falls have decreased by over 30%.
grp grating
The longevity of GRP grating facilitates its portrayal as an economical choice. Despite higher initial costs compared to traditional materials, the reduced need for maintenance and replacements curtails long-term expenses. An engineer from a major water treatment facility shares their experience “Switching to GRP grating was strategic. Our maintenance team has noted the reduced upkeep needed — the investment has paid for itself over five years due to decreased replacement and labor costs.”
In terms of customization, GRP grating offers unmatched versatility. It can be crafted in various shapes, sizes, and colors to meet the specific requirements of any project. It is also available in different fibrous configurations, catering to specific strengths and rigidity demands. A construction manager affirms that this adaptability has allowed their projects to meet both aesthetic and functional design criteria without compromise.
When considering the transition to GRP grating, potential users should evaluate the specific environmental conditions and mechanical stresses likely to be encountered by the grating. Consulting with suppliers and field experts will ensure selection of an appropriate resin type and design configuration, optimizing the grating for its intended purpose.
In conclusion, the application of GRP grating promises enhanced safety, durability, and cost-effectiveness across various high-stress environments. Its proven track record of reducing maintenance costs and improving safety standards provides authoritative evidence of its value. Incorporating GRP grating is a forward-thinking strategy that aligns with industry-wide shifts toward sustainable and low-maintenance solutions, reinforcing trust and confidence in its capabilities from both users and experts.