Inserting rock bits is a critical aspect of drilling operations, especially in industries like oil and gas, geothermal drilling, and construction.
Effective techniques and strategies can significantly improve operational efficiency, cost-effectiveness, and overall project success. This article explores innovative, authoritative, and practical approaches to rock bit insertion, drawing upon real-life experiences and professional insights, promising unique strategies not commonly found on search engines.
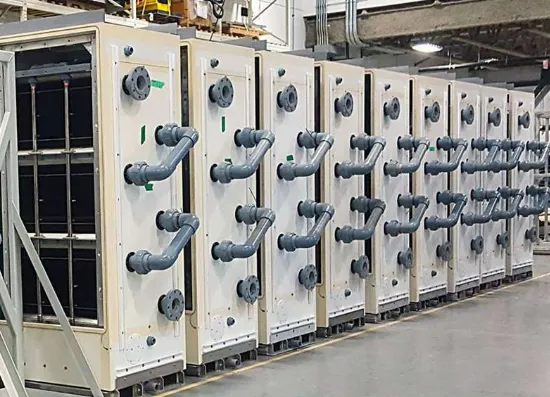
Understanding rock bits is essential for implementing efficient insertion techniques. The foundation lies in selecting the right bit type—roller cone bits, fixed cutter bits, or diamond bits—depending on the geological formation. Engaging with professionals who have extensive field experiences, such as geologists and seasoned drilling engineers, provides invaluable insights. These experts frequently emphasize pre-emptive site analysis and geological surveying, which establish a groundwork for the choice of appropriate rock bits based on the characteristics of the terrain.
A noteworthy yet often overlooked strategy is the incorporation of real-time data analytics and adaptive drilling technologies. Advanced sensors installed in drilling rigs can provide real-time feedback on parameters like rotational speed, thrust force, and bit wear. Experienced operators leverage this data to modify insertion techniques dynamically, thereby optimizing efficiency and prolonging tool life. Implementations of AI algorithms can predict potential malfunctions or inefficiencies, allowing for proactive measures rather than reactive adjustments.
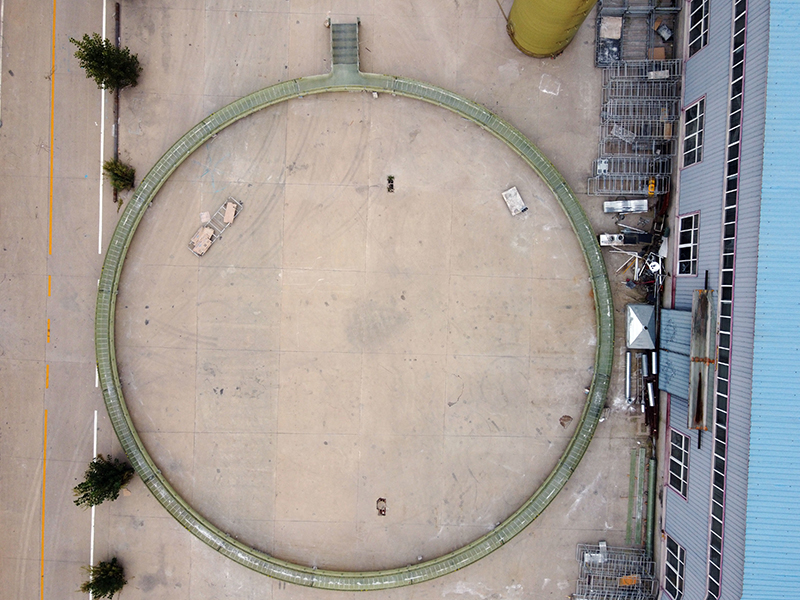
Another critical technique centers around the preservation of bit integrity during insertion. Pre-conditioning the borehole and maintaining optimal drilling fluid properties are tactical measures employed to mitigate friction and heat, thereby reducing wear and tear on the bit. Substantial field evidence shows that using specifically formulated drilling mud can dramatically decrease the temperature gradient and improve the cooling rate of bits. This practice not only preserves the integrity of the tool but also enhances penetration rates and efficiency.
inserting rock bits techniques and strategies for efficient
Efficiency also calls for the adoption of a robust maintenance and reconditioning protocol. Engaging with manufacturers who offer state-of-the-art re-sharpening and refurbishment services further extends the life cycle of expensive rock bits. Companies with substantial expertise in metallurgy and machining provide insightful recommendations on the best materials and coatings, customized to the specific mining or drilling application, thus ensuring that the bits are not only durable but highly efficient in rock penetration.
Leadership in the field predominantly advises the development of comprehensive training programs to upskill drilling team members. These programs must go beyond technical skills by incorporating case studies, simulation exercises, and sharing successes and failures from various projects. Practical insights from experienced professionals can foster a culture of continuous improvement, enhancing operators' decision-making capabilities in challenging scenarios.
Effective rock bits insertion also demands a collaborative approach, integrating insights from material science, mechanical engineering, and environmental studies. Multi-disciplinary teams can innovate design improvements and recommend sustainable practices that reduce environmental impact while maintaining drilling efficiency. Such initiatives build trust and authority within the industry, showcasing a commitment to both operational excellence and environmental stewardship.
In summary, successful rock bit insertion techniques hinge upon an intimate understanding of geological conditions, real-time data utilization, rigorous maintenance protocols, comprehensive training, and sustainable practices. By adopting cutting-edge technologies and fostering an environment of continuous learning and collaboration, industries can achieve significant enhancements in drilling efficiency and operational reliability. This holistic, proactive approach not only maximizes productivity but also reinforces trust and authority in project outcomes, ultimately distinguishing leaders from their competitors in the drilling field.