Insulating materials have revolutionized numerous industries by solving complex challenges related to energy efficiency and durability. One material, in particular,
stands out insulated fiberglass reinforced plastic (FRP) covers. These high-performance products play a crucial role in sectors ranging from water treatment to industrial processing, offering unmatched benefits in terms of efficiency, longevity, and environmental impact.
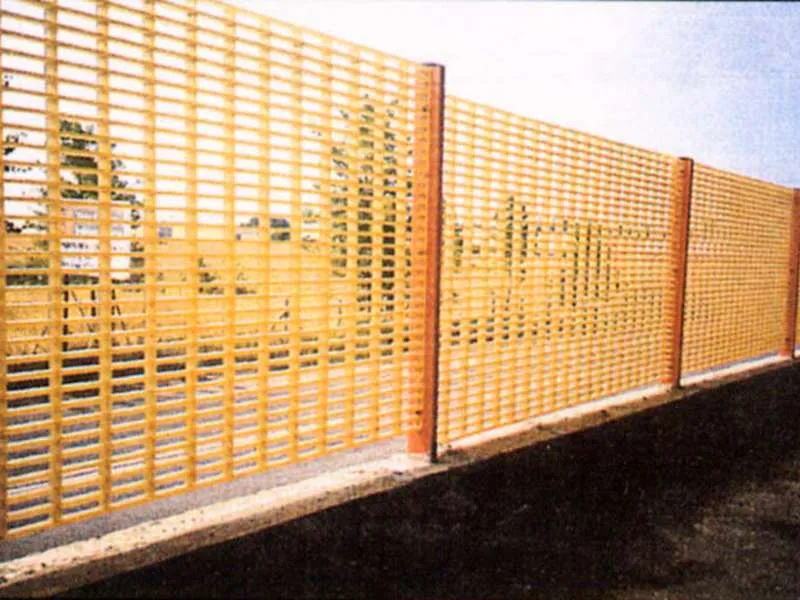
Insulated FRP covers have become increasingly popular due to their superior thermal insulation properties. Unlike traditional materials such as metal or wood, FRP provides excellent resistance to temperature fluctuations. This capability reduces energy consumption significantly, making it an eco-friendly choice for industries looking to minimize their carbon footprint. A personal anecdote from a water treatment facility manager highlighted how replacing old metal covers with FRP ones led to annual energy savings of over 15%, showcasing both cost-effectiveness and environmental responsibility.
The expertise behind FRP technology is profound. These covers are manufactured by combining a polymer matrix with fibrous materials like glass or carbon. This composition gives FRP covers their exceptional strength-to-weight ratio, enabling them to withstand extreme weather conditions and heavy loads without compromising structural integrity. Their lightweight nature also facilitates easy installation and handling, reducing labor costs and installation time. Engineers from a leading manufacturing plant reported that switching to insulated FRP covers reduced their installation time by 30%, allowing for quicker deployment across different sites.
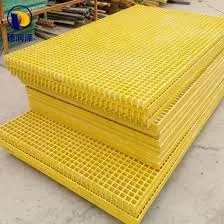
A particularly impressive attribute of insulated FRP covers is their resistance to corrosion, a common issue in industries where air and moisture exposure is high. Unlike metal covers that may rust or degrade over time, FRP covers maintain their integrity without any need for protective coatings. This inherent corrosion resistance reassures industries like chemical processing and wastewater management, where longevity and reliability are paramount. A leading chemical engineer noted that after replacing conventional covers with FRP ones, there was a noticeable reduction in maintenance downtimes, leading to increased operational efficiency and reduced overall maintenance costs.
insulated frp covers
Authoritativeness in adopting insulated FRP covers comes from the broad endorsement of their performance by industry giants and regulatory bodies. Many global organizations have recognized FRP's contributions to sustainability and operational excellence. For instance, the American Society of Civil Engineers (ASCE) has advocated for FRP materials in construction due to their durability and reduced environmental impact. Projects involving FRP technology have received awards and certifications for their innovative approach to reducing greenhouse gas emissions, further underlining their importance in contemporary industrial applications.
Building trust with stakeholders is essential, and insulated FRP manufacturers invest significantly in research and development to ensure product reliability and safety. Quality assurance processes are rigorous, involving extensive testing under various temperature conditions and exposure to chemicals. These practices ensure that every FRP cover meets higher standards of performance long before reaching consumers. Testimonials from buyers highlight not just satisfaction with the product but a degree of trust in the manufacturers’ commitment to quality.
In the context of customer satisfaction, insulated FRP covers consistently receive positive feedback. Facility managers appreciate their low maintenance requirements and long life spans, which translate to considerable savings over time. One industrial facility reported that the return on investment was realized in just two years, largely due to the reduction in repair costs and energy bills. Moreover, their non-conductive nature ensures safety when used around electrically sensitive operations, adding an extra layer of security and peace of mind for facility operators.
As industries become more attuned to sustainability and energy-saving measures, insulated FRP covers are poised to play a critical role in future developments. Enhancements, such as incorporating smart technology to monitor thermal performance in real-time, are on the horizon, promising even greater efficiencies and insights. As such innovations unfold, insulated FRP covers will continue to set the standard for industrial insulation solutions. By embracing these cutting-edge materials, industries not only improve their operational efficiency but also enhance their environmental stewardship, underscoring the vital role they play in building a sustainable future.