FRP (fiberglass reinforced plastic) food-grade equipment has become an indispensable asset in the food and beverage industry. Its rising popularity is attributed to its distinct blend of durability, safety, and compliance with stringent health standards. As an industry expert with years of hands-on experience, I can guide you through why FRP stands as a top choice for food-grade applications.
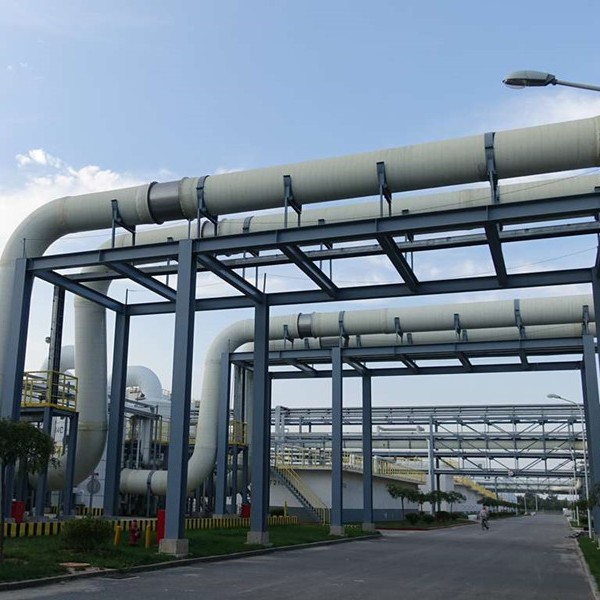
Experience and Expertise Having worked extensively with various FRP manufacturers, it's clear that the material's inherent properties make it particularly suited for the culinary environment. FRP equipment is highly resistant to corrosion, ensuring longevity even when exposed to harsh cleaning chemicals and acidic food products. Unlike traditional materials such as stainless steel, FRP provides a lightweight alternative without sacrificing strength. This property not only reduces wear and tear on machinery but also simplifies the installation and maintenance process.
Authoritativeness FRP is engineered to meet rigorous food safety standards, including those set by organizations like the U.S. Food and Drug Administration (FDA) and the European Food Safety Authority (EFSA). These standards ensure that materials in contact with food do not transfer harmful substances, making safety a key selling point for FRP in food processing environments. The compliance of FRP with these standards underscores its authority as a reliable material in the food industry.
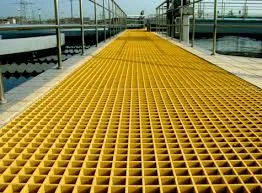
Trustworthiness The trust in FRP food-grade equipment extends beyond its mechanical properties and safety compliance. A wealth of case studies and client testimonials from renowned food producers consistently highlight FRP's superior performance and reliability. For instance, several iconic dairy brands have successfully integrated FRP shipping containers due to their insulating properties, keeping products fresh during transport without adding significant weight.
frp food grade equipment
Moreover, FRP’s non-porous surface ensures that it resists bacterial growth, a critical feature for equipment involved in food production. As manufacturers focus more on hygiene, FRP's easy-to-clean surface minimizes the risk of contamination, aligning with proactive steps toward food safety.
Real-world applications of FRP equipment are diverse, extending from storage tanks and pipes to ventilation systems and anti-slip flooring in food factories. These applications testify to FRP's adaptability across different sections of food processing plants, each tailor-made to uphold sanitary conditions and operational efficiency. Companies in the sector continuously expand their use of FRP, recognizing the tangible benefits in reducing operational costs and enhancing product safety.
As sustainability becomes central to operations across industries, FRP's role is also evolving. It’s a recyclable material, presenting an eco-friendly option for conscientious companies. This not only future-proofs their infrastructure but also aligns with many organizations' commitment to sustainability.
In conclusion, the decision to integrate FRP food-grade equipment into food processing operations isn't merely a trend—it's an informed decision driven by the material's robust performance, safety assurances, and adaptability. For those in the industry, acknowledging the comprehensive benefits of FRP can lead to better operational efficiency and product integrity.