The world of industrial manufacturing and engineering is vast, with tools and components playing a crucial role in ensuring accuracy and efficiency. Among these, the mandrel stands out as an essential tool used in various applications, from precision engineering to complex manufacturing processes.
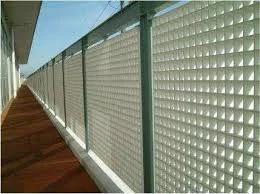
A mandrel, often underestimated, is integral to many industries, offering unprecedented support in machining, bending, and forming tasks. For those unfamiliar, a mandrel refers to a cylindrical tool inserted into materials to shape or support them during the manufacturing phase. This tool may seem simple, but its applications are diverse and significant.
In the realm of precision engineering, mandrels have carved a niche by ensuring immaculacy. Products demand specific measurements, and the mandrel ensures these specifications are met, preventing deviations that could lead to potential failures or inefficiencies.
Take the aerospace industry, for example. Here, the mandrel is used extensively in the production of engine components where precision is not just a requisite but a necessity. Any deviation in the component shape or size could lead to catastrophic failures. Therefore, the reliability of a mandrel directly influences the quality of the output, enhancing trust in the manufacturing process.
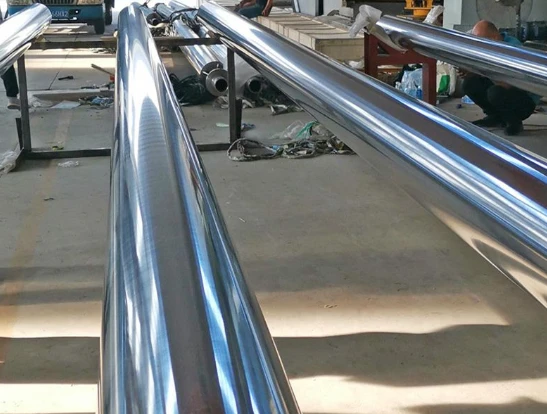
Professional expertise relies heavily on the qualities and characteristics of the mandrel used. Not all mandrels are created equal, and different applications require specific types. Tapered mandrels might be suitable for one operation, while an expanding mandrel is necessary for another. An expert eye can discern which mandrel to employ based on material properties, desired outcomes, and operational conditions. This expertise ensures optimal performance, showcasing the mandrel's indispensable nature in specialized fields.
mandrel
Furthermore, innovation in materials and design have expanded the applications of mandrels. Traditionally made from steel, modern mandrels may incorporate composite materials to improve durability and reduce weight. Innovations such as these increase the mandrel's applicability across various industries, including automotive and medical devices, where even a slight miscalculation can have significant consequences. Manufacturers now offer customized mandrels tailored to specific industrial needs, further enforcing their expert value proposition.
Authoritatively speaking, the significance of mandrels goes beyond their immediate functionality. Their design and material impact operational efficacy, cost-effectiveness, and even energy consumption during production. Consequently, they represent a cornerstone in sustainable manufacturing practices. Industries are increasingly looking for ways to minimize waste and energy usage, and mandrels contribute by ensuring components are produced right the first time, thereby reducing the need for rework and excess material usage.
Trustworthiness in tools is non-negotiable in high-stakes industries. Manufacturers who prioritize quality mandrels ensure longer tool life, minimizing downtime due to tool failure. This trust translates into financial savings and enhances an organization's reputation as a reliable partner in the production chain. Additionally, as industries evolve with advancements in technology and materials, the adaptability and reliability of mandrels keep them relevant and trustful in the eyes of engineers and manufacturers alike.
In conclusion, understanding and choosing the right mandrel is not just about selecting a tool but is an investment into the production's success and reliability. It embodies experience, expertise, authority, and trustworthiness, making it an invaluable asset across various fields. As industries continue to evolve, the humble mandrel will undoubtedly continue to play its quiet yet powerful role in shaping the future of manufacturing and engineering.