In the realm of manufacturing and engineering, the term mandrel signifies a crucial component that profoundly impacts the quality and efficiency of various production processes. This robust tool serves as an indispensable aid in industries spanning from metalworking and aerospace to medical device fabrication. Mandrels are not mere implements; they are the unsung heroes that ensure precision, durability, and optimal functionality in countless applications.
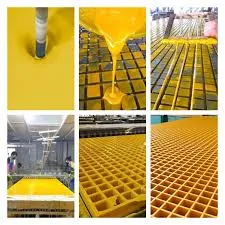
A mandrel, in its most basic definition, is a device used to shape, support, or deliver components in manufacturing and assembly processes. Its essential role is often understated, yet without it, the precision and perfection required in industrial production could be compromised. Mandrels serve a multitude of purposes, from holding workpieces during machining or shaping tubular items to being the core around which objects are formed.
The expertise involved in designing and utilizing mandrels cannot be overstated. Each mandrel must be meticulously crafted to match the specific requirements of the task it is meant to perform. In the medical field, for example, mandrels might be used in the creation of stents where precision can mean the difference between success and failure. Experts in the field carefully consider material properties, dimensions, and stress tolerances to produce mandrels that can withstand rigorous conditions while maintaining their integrity.
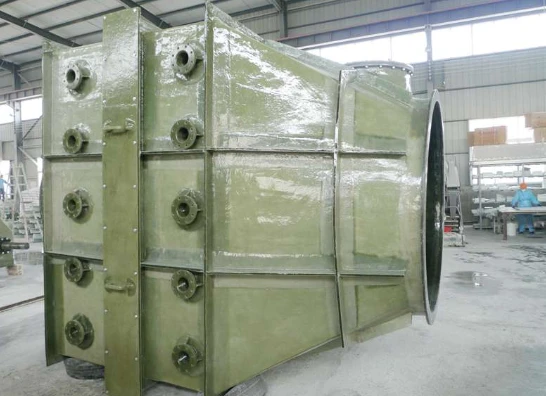
From an experience perspective, seasoned engineers and machinists understand that the choice of mandrel directly affects the quality of the output. A poorly chosen or fabricated mandrel can lead to defects in the finished product, whether that's poor alignment in automotive parts or irregular dimensions in extruded materials. Experience brings wisdom in selecting not only the right type of mandrel but also in implementing it effectively within the production line. Skilled professionals can anticipate potential challenges and adjust processes to mitigate them, ensuring that the mandrels contribute positively to the desired outcome.
mandrel
Mandrels also possess a significant authoritative presence in the industry due to their indispensable roles. With the evolution of technology, modern mandrels are engineered with superior materials such as high-strength alloys or composites that offer robustness while minimizing weight. This advance has significantly expanded their application to various high-tech fields such as aerospace engineering, where every gram matters. Companies specializing in mandrel production are at the forefront of innovation, continuously improving upon designs to meet ever-stringent industrial demands.
Trustworthiness in the use of mandrels is paramount. Manufacturers need to be confident that their mandrels will perform consistently under pressure.
This trust is built through rigorous testing and quality assurance processes. For instance, mandrels for the oil and gas industry must endure extreme conditions and corrosive environments, necessitating thorough material testing and lifecycle analysis. By adhering to stringent industry standards and regulations, manufacturers can assure clients of their mandrels’ reliability, longevity, and adherence to safety protocols.
In conclusion, the mandrel is a pivotal component in today's manufacturing landscape. Combining experience, expertise, authority, and trustworthiness, mandrels not only enhance production processes but also ensure the highest quality end products. Whether in the precision-dependent medical sector or the dynamically complex aerospace industry, mandrels continue to prove their worth time and again as essential tools that underpin the success of modern manufacturing endeavors.