Molded fiberglass, an innovative material, has revolutionized the way various industries approach design and production, offering a blend of strength, versatility, and aesthetic appeal. This article delves into the multifaceted world of molded fiberglass, exploring its applications, benefits, manufacturing process, and future potential within product realms.
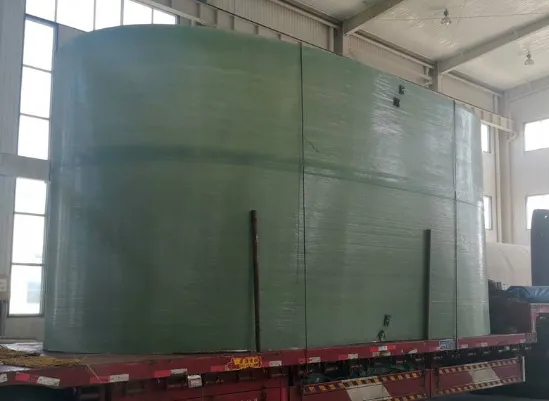
Understanding Molded Fiberglass
Molded fiberglass is renowned for its lightweight yet durable nature, making it an ideal choice for a wide array of products, from automotive components to architectural features. This material comprises glass fibers reinforced with plastic, often polyester resin, creating a composite with high tensile strength and impressive resistance to environmental factors.
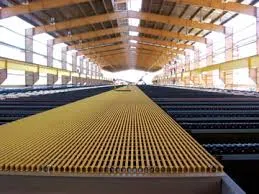
Applications Across Industries
Transportation
The transportation industry exploits molded fiberglass's low weight and high durability, which are crucial for enhancing fuel efficiency and performance. It finds applications in manufacturing automobile body panels, truck beds, and components of public transportation vehicles like buses and trains. This usage not only contributes to weight reduction but also allows for innovative design possibilities due to the material's moldable nature.
Construction and Architecture
In construction, molded fiberglass is used for producing panels, roofing materials, and decorative elements. Its resistance to corrosion and weathering extends the lifespan of structures, promoting sustainability. Additionally, custom architectural elements crafted from molded fiberglass help in achieving unique designs that traditional materials might not support.
Renewable Energy
Wind turbine blades prominently use molded fiberglass due to its lightweight strength, enhancing energy efficiency and longevity. The renewable energy sector benefits immensely from these attributes, as they contribute to the development of more efficient turbines, essential for the industry’s growth.
Consumer Goods
From furniture to sporting equipment, molded fiberglass is a staple in consumer goods. Its adaptability allows for ergonomic and aesthetically pleasing designs in furniture, while its strength is harnessed in the production of durable sporting equipment like surfboards and kayaks.
The Manufacturing Process
Molded fiberglass is produced through techniques like hand lay-up, spray-up, and resin transfer molding (RTM). Each method offers distinct advantages depending on the scale and complexity of the product.
Hand Lay-Up
One of the oldest methods, hand lay-up, involves manually applying resin and fiberglass layers into a mold. This process is cost-effective for low-volume production and allows for intricate detailing, ideal for custom pieces or prototypes.
Spray-Up
molded fiberglass
Similar to hand lay-up, but involving spraying the resin and chopped fiberglass onto the mold, spray-up is faster and suited for larger products. This method balances cost and production speed, making it viable for medium-scale manufacturing.
Resin Transfer Molding (RTM)
RTM involves injecting resin into a mold where fiberglass is pre-placed. This closed-mold process provides superior surface finish and precise fiber alignment, ideal for high-volume production of complex shapes with consistent quality.
Benefits of Molded Fiberglass
Durability and Strength
Molded fiberglass products are resistant to impact, corrosion, and weather, ensuring longevity across applications. This durability reduces maintenance costs and frequency, an economic benefit for manufacturers and consumers alike.
Lightweight
The material's low density contributes to ease in handling and reduces transportation costs, critical in industries like automotive and aerospace where weight directly influences performance and efficiency.
Design Flexibility
Fiberglass's ability to be molded into virtually any shape without losing strength lends itself to innovative product designs. The material’s adaptability allows for the creation of customized solutions tailored to specific functional and aesthetic needs.
Sustainability
The production and usage of molded fiberglass support environmental sustainability. By extending the lifespan of products and structures, reducing fuel consumption due to lower weight in transportation, and being amenable to recycling, molded fiberglass aligns with eco-friendly initiatives.
Trust in Expertise
Manufacturers and consumers can trust molded fiberglass products thanks to decades of development and proven performance in critical applications. Companies specializing in fiberglass manufacturing adhere to stringent quality standards, ensuring each product meets rigorous safety and durability benchmarks.
Looking Forward
The future of molded fiberglass is promising, with advancements in resin and fiber technology paving the way for even lighter and stronger composites. The ongoing research and development efforts aim at expanding its applications in emerging fields such as aerospace and biomedicine, potentially opening new markets.
In summary, molded fiberglass stands out as a material of choice due to its versatile applications, superior performance, and sustainable qualities. As industries continue to innovate, fiberglass will likely play a pivotal role in shaping the future of product design and functionality. Its proven expertise, reinforced by continued advancements, ensures that molded fiberglass remains a trusted and authoritative choice in the evolving landscape of material science and engineering.