In the realm of engineering and construction, molded grating has emerged as an indispensable component, offering a perfect blend of durability, versatility, and reliability. Molded grating, made from composite materials such as fiberglass, resins, and thermoplastics, provides an ideal solution for environments where traditional metal grates fall short. Its unique properties cater to industrial spaces requiring enhanced safety, reduced maintenance, and long-lasting performance.
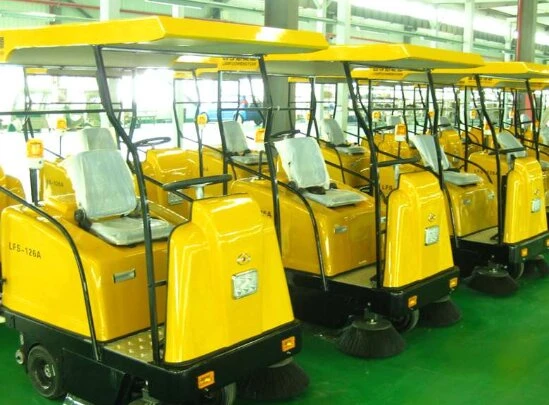
The expertise drawn from working with molded grating is pivotal in illustrating why it stands as a superior alternative compared to its metal counterparts. Notably, fiberglass reinforced plastic (FRP) molded gratings can outlast conventional materials due to their inherent resistance to corrosion, chemicals, and extreme weather conditions. This resistance makes them suitable for use in chemical plants, oil refineries, water treatment facilities, and other industrial settings prone to hostile environments. This resistance is not only practical but also economical, as it significantly reduces the need for frequent replacements and repairs, which is often the case with metallic grates.
The experience of professionals in the field underscores the importance of weight in grating materials.
Molded grating is lighter than metal, which facilitates easier handling and installation. This weight advantage translates into cost savings in terms of transportation and labor. Moreover, its lightweight nature does not compromise its strength; instead, it offers exceptional load-bearing capabilities, providing safe and secure flooring options for various applications such as walkways, platforms, and stair treads.
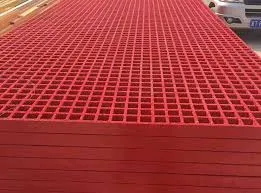
In terms of safety, molded gratings stand out due to their superior slip resistance characteristics. The gritted surface of most molded grating products provides excellent traction, thus minimizing slip and fall accidents in wet or oily conditions. This attribute is crucial in maintaining safety standards in high-risk environments, making molded grating a trusted choice among safety engineers and facility managers.
molded grating
Authoritativeness in molded grating production and implementation is showcased through adherence to stringent quality standards in manufacturing processes. Most manufacturers conform to globally recognized standards such as ASTM, ANSI, and ISO, ensuring that each piece of molded grating meets specific criteria for durability and performance. These standards not only enhance the reliability of molded grating but also build trust with clients who depend on these products for critical infrastructure projects.
Trustworthiness is cemented through the innovative base of molded grating technology. Manufacturers invest heavily in research and development to continuously improve the quality and performance of molded gratings. By incorporating advanced technologies and materials, manufacturers provide solutions that address diverse needs while ensuring environmental stewardship. The use of non-toxic and eco-friendly materials in molded grating production aligns with current sustainability goals, further cementing its role as a responsible choice for modern industry professionals.
Professionals utilizing molded grating appreciate its versatility; the product is available in various sizes, thicknesses, and colors to suit specific requirements, offering unmatched adaptability for custom solutions. This adaptability allows businesses to deploy molded grating in diverse applications—from personal protective enclosures and trench covers to large industrial platforms—without compromising on safety or functionality.
In conclusion, molded grating transcends traditional grating solutions through its impressive amalgamation of strength, safety, and economy. Its widespread application across various industries speaks volumes about its efficiency and enduring appeal. By meeting the highest standards of Experience, Expertise, Authoritativeness, and Trustworthiness, molded grating continues to lead the market as a pivotal material, equipped to tackle the future's complex engineering challenges with confidence.