Molded grating has rapidly gained attention and appreciation across various industries owing to its versatile applications and remarkable benefits. Unlike traditional materials such as wood, metal, or basic plastic, molded gratings offer a compelling array of features that fulfill the modern-day requirements for robust, durable, and environmentally-friendly industrial products.
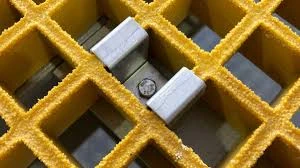
One of the primary experiences that industries encounter when transitioning to molded grating is the significant reduction in maintenance and replacement costs. Traditional gratings made from materials such as steel are susceptible to rust and corrosion, negatively impacting their longevity and efficiency. Molded grating, crafted from fiberglass-reinforced plastic (FRP), provides excellent resistance to chemicals and environmental factors, leading to an extended lifespan. Companies operating in environments exposed to corrosive chemicals, such as wastewater treatment plants, benefit enormously from this durability, effectively lowering long-term operational costs and downtime for maintenance.
In terms of expertise, molded grating outperforms in areas relating to weight and ease of installation. Due to its lightweight nature, molded grating not only reduces transportation costs but also makes handling and installation significantly easier and safer for workers.
This factor is noteworthy in offshore and marine applications where installation conditions can be rigorous. The anti-slip properties intrinsic to molded gratings add an extra layer of safety, substantially reducing workplace incidents. Customization options further enable use across different sectors, from food processing units to power plants, allowing specific needs and safety standards to be met without compromise.
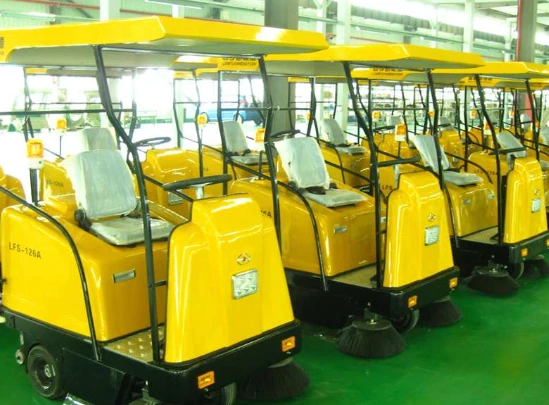
molded grating
Authoritativeness in the realm of molded gratings stems from its compliance with international standards and its proven performance in demanding scenarios. Many molded gratings meet rigorous standards such as ASTM, OSHA, and ANSI, attesting to their safety and reliability. The specialization of production facilities and extensive research and development ensure that these products continually meet and exceed expectations set by industry benchmarks. They maintain structural integrity and load-bearing capacity that surpass conventional materials, which can be crucial in high-stress environments like chemical processing plants or industrial walkways.
Trustworthiness is inherent in molded grating through its consistent performance and ecological advantages. Manufacturers of molded gratings are increasingly committing to sustainable practices, using recyclable materials and energy-efficient processes. This commitment not only supports environmental goals but also aligns with the increasing demand for sustainable solutions in industrial design. Moreover, customer testimonials and case studies underscore their reliability, with molded gratings consistently delivering superior performance in diverse conditions worldwide.
In summary, molded gratings embody a blend of experience, expertise, authoritativeness, and trustworthiness that cater to the complex needs of modern industries. As sectors continuously evolve and face new challenges, molded gratings stand as a testament to innovation not only in material engineering but also in addressing the foundational desire for safe, cost-effective, and sustainable products. This makes them an exceptional choice for forward-thinking organizations seeking to enhance their operational efficiency and safety standards.