Fiberglass reinforced plastic (FRP) chemical tanks have long been a preferred choice for industries requiring durable, corrosion-resistant, and cost-effective storage solutions for chemicals. Combining innovation with tried-and-tested technology, FRP tanks offer a superior alternative to traditional materials such as steel and concrete, especially in highly corrosive environments.
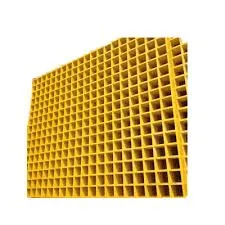
The standout feature of FRP chemical tanks lies in their exceptional resistance to a wide range of chemicals. Thanks to the non-reactive nature of fiberglass and the adaptability of resin formulations, these tanks can be custom-designed to withstand specific chemicals without the risk of structural degradation over time. This adaptability not only extends the lifespan of the tanks but also reduces maintenance costs substantially. Industries that regularly deal with corrosive substances, such as petroleum, wastewater treatment, and chemical manufacturing, find FRP tanks invaluable due to their exceptional durability and reliability.
Expert engineering and manufacturing processes ensure that FRP tanks meet rigorous industry standards. With expertise rooted in advanced composite material science, manufacturers employ precise resin and reinforcement techniques to produce tanks that exhibit consistent performance characteristics. This engineering acumen translates into tanks capable of withstanding harsh environmental conditions while maintaining structural integrity. FRP tanks often surpass standard compliance, offering peace of mind to industries that prioritize safety and durability.

The design flexibility of FRP tanks allows them to be tailored to unique industry requirements. With a wide array of shapes, sizes, and configurations available, FRP tanks can be engineered to fit spatial constraints or specific installation needs that traditional materials struggle to accommodate. Moreover, these tanks often feature additional design elements, such as secondary containment systems, to enhance safety and efficiency. Customizable features ensure that each FRP tank performs optimally in its intended application, whether aboveground, underground, or within specialized processing systems.
frp chemical tank
What further distinguishes FRP chemical tanks is their commitment to sustainability. The manufacturing process of FRP materials typically results in a lower carbon footprint compared to traditional metals, aligning with industries seeking eco-friendly solutions. Additionally, the long lifespan and reduced need for frequent replacements or repairs lower the overall environmental impact, reinforcing the corporate responsibility goals of modern businesses. As industries place greater emphasis on environmentally friendly practices, the utilization of FRP tanks supports both operational goals and environmental stewardship.
Trust in FRP chemical tanks is bolstered by decades of successful deployment across various sectors. Industry professionals continue to advocate for their application, citing firsthand experiences in efficiency and cost savings. The collaborative approach between manufacturers and end-users ensures that FRP tanks are designed and implemented to exacting specifications, fostering a partnership that is both consultative and solution-oriented. This trusted relationship underscores the value of FRP chemical tanks not just as a product, but as a cornerstone for business operations that demand reliability and precision.
In conclusion, FRP chemical tanks stand as a testament to the evolution of industrial storage technology. With unmatched resistance to corrosion, customizable design, robust manufacturing, and a focus on sustainability, these tanks represent the pinnacle of industry solutions for chemical storage. For businesses seeking to enhance their operational integrity while embracing modern advancements, FRP chemical tanks deliver on all fronts, ensuring safety, efficiency, and peace of mind for years to come.