GRP flanges have rapidly become essential components in a variety of industrial applications, owing to their superior properties compared to traditional materials. GRP, or Glass Reinforced Plastic, is renowned for its exceptional strength-to-weight ratio, corrosion resistance, and versatility, making it a preferred choice in industries ranging from chemical processing to marine engineering.
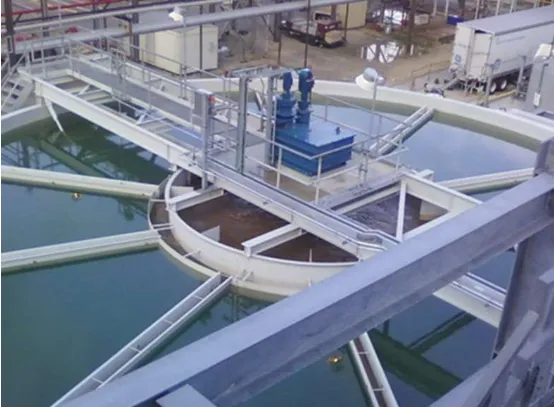
Experience with GRP flanges demonstrates their remarkable capacity to withstand extreme environments. In chemical plants, for instance, pipelines often transport highly corrosive substances. Traditional metal flanges can suffer degradation in such settings, leading to leaks and costly downtime. However, GRP flanges offer resilience against these aggressive chemicals, significantly reducing the need for frequent maintenance and replacements. Users have reported extended service life and virtually no performance issues, attributing this reliability to the intrinsic corrosion-resistant properties of GRP materials.
From a professional standpoint, the expertise involved in manufacturing GRP flanges ensures that they meet the highest industry standards. The production process involves integrating high-quality glass fibers with a plastic resin matrix, resulting in a product that can endure substantial mechanical stress.
This method guarantees uniformity and structural integrity across each flange. Specialists adept in composite materials engineering emphasize the importance of precise fabrication techniques and rigorous quality control measures, ensuring that each GRP flange performs optimally under demanding conditions.
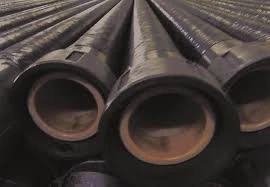
Among the authoritative voices in the industry, the consensus is clear GRP flanges provide a sustainable and cost-efficient alternative to conventional metal flanges. Institutions involved in standardizing industrial components have recognized GRP's potential and continually update guidelines to incorporate advanced composite solutions like these. The authoritative backing from such organizations bolsters confidence among users who transition to GRP systems, knowing they are supported by rigorous standards.
grp flange
Trustworthiness is further established through the continual evolution of GRP technology and its successful deployments in diverse projects worldwide. Industry leaders often highlight case studies where GRP flanges have been implemented in critical infrastructure, such as offshore oil platforms, where they encounter harsh operational conditions. These real-world applications demonstrate the material's reliability and the trust industries place in its performance.
The product's sustainability aspect also plays a vital role in its growing acceptance. GRP flanges contribute to environmental conservation by being lightweight, which reduces transportation fuel consumption during installation. Additionally, the durability of GRP flanges lessens the demand for replacements, minimizing waste and supporting sustainable industry practices.
In conclusion, GRP flanges are at the forefront of modern industrial components, offering peerless performance, expert engineering, and validated reliability. Their adoption continues to rise as industries seek materials that not only perform under pressure but also align with environmental objectives. By choosing GRP flanges, industries are investing in a future-proof solution that delivers on both technical specifications and corporate responsibility.