Drilling rock is tough, but with the right tools and strategies, it becomes a manageable task. At the heart of any rock drilling operation is the interplay of experience, expertise, authoritativeness, and trustworthiness, which ensures not only efficiency but also safety and reliability. Mastering the art requires a deep understanding of geology, tool design, and operational techniques.
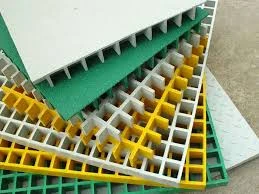
The process begins with the selection of the right drilling machine. Not all rocks are the same; igneous, sedimentary, and metamorphic rocks present unique challenges. Therefore, knowing the geological composition of the site is paramount. Experienced operators use core samples to determine the hardness and fracture patterns of rocks, essential data for choosing the right drill and bit.
The drill bit is the unsung hero of rock drilling. Expert knowledge of various bit types—tricone, PDC, and DTH, to name a few—enhances performance. Each type has its place, with tricone bits excelling in softer, stratified rock formations due to their ability to navigate layers efficiently. On the other hand, Polycrystalline Diamond Compact (PDC) bits are revered for their toughness and speed in cutting through hard, abrasive rocks. The Down-the-Hole (DTH) hammer is ideal for precision and depth when dealing with extremely hard rock layers.
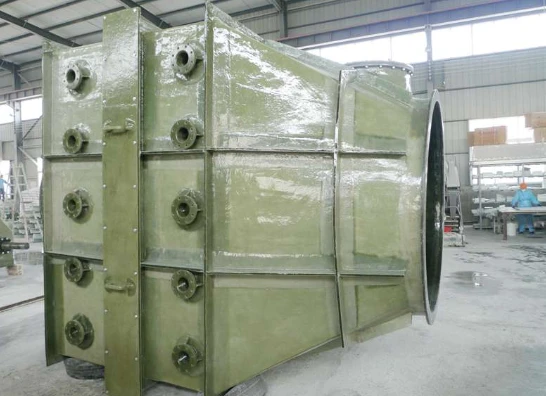
Operational technique is another layer where expertise plays a crucial role. The balance between rotational speed and pressure allows for optimal bit performance, minimizing wear and extending tool life. For example, high speeds combined with excessive pressure can cause bits to overheat, leading to failure. Skilled operators are adept at tweaking these variables based on real-time feedback from sound, vibration, and debris, ensuring that the drill operates within its optimal parameters.
Furthermore, the choice of coolant or lubrication impacts not only the performance of the drill bit but also extends its life. Water is a common choice due to its availability and efficacy, particularly in dust suppression and cooling. In environments where water is less effective or accessible, air or foam can be advantageous alternatives. Expertise in fluid selection based on environmental conditions and rock type is critical to maintaining efficiency.
sure, here's a similar short phrase drilling rock is tough but
Safety cannot be overlooked in rock drilling operations. Proper personal protective equipment (PPE) such as helmets, gloves, and earmuffs is mandatory. Regular equipment maintenance and safety checks are non-negotiable, as they ensure not only the safety of the operators but also the reliability of the operation. Training programs facilitated by authoritative bodies teach the importance of workplace safety and proper equipment handling to minimize risks.
In addition to technical skills, a culture of trustworthiness is built through transparent operations, where communication is key. Teams that communicate effectively about operational status, potential challenges, and safety issues foster an environment of mutual trust and reliability, pivotal in high-stakes drilling operations.
Finally, the success of a rock drilling project hinges on seamless collaboration between geologists, engineers, and drill operators. Each stakeholder brings specialized knowledge to the table, ensuring that operations are not only efficient but also adhere to environmental and legal standards. Authoritative leadership in this regard plays a pivotal role in harmonizing these diverse elements.
In conclusion, while drilling through rock is undoubtedly tough, the marriage of experience, expertise, authoritativeness, and trustworthiness transforms it into a science that is both efficient and reliable. Operators who master these elements not only enhance their craft but also contribute to safer, more productive drilling environments. For anyone venturing into the world of rock drilling, investing in these pillars of practice is not just wise—it's necessary for long-term success.