Innovative Tools for Efficient Tunnel Rock Drilling
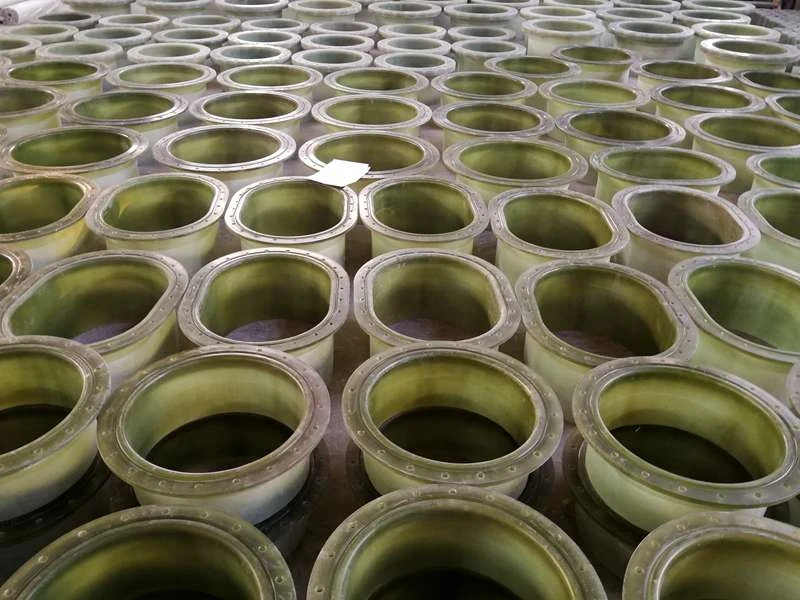
Building expansive underground networks, whether for transportation, utilities, or mining, requires sophisticated tools designed specifically to drill through solid rock. As the demand for efficient and reliable infrastructure grows, the importance of optimized tools for rock drilling in tunnels cannot be overstated. Here is an exploration of the latest advancements, founded on substantial research and expert assessment, that are revolutionizing the industry.
The Evolution of Rock Drilling Tools
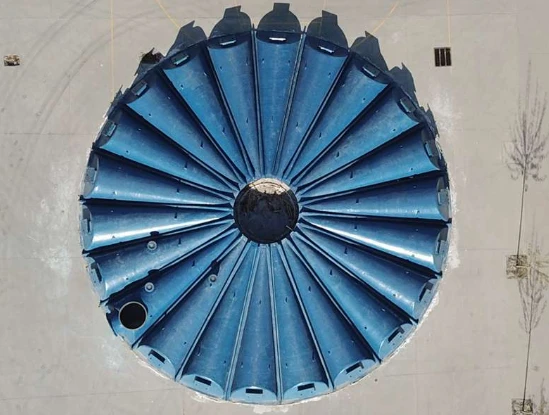
The need to drill through rock effectively and safely has led to significant advancements in drilling technology. Traditional methods, though effective in their time, posed numerous challenges including slow progress, excessive wear, and high fuel consumption. Today’s tools are engineered to overcome these shortcomings with improved precision and durability. They offer enhanced penetration rates, allowing for faster completion of projects without compromising safety standards.
High-Performance Tunnel Boring Machines (TBMs)
Modern Tunnel Boring Machines (TBMs) exemplify a leap in technological innovation and are at the forefront of rock drilling technology. These machines boast cutting-edge features that make them indispensable in tunneling projects. Equipped with rotating cutting wheels, TBMs cut swiftly through rock and simultaneously support the tunnel face with pre-cast segments. This dual functionality minimizes surface subsidence and enhances safety.
A key component to the effectiveness of TBMs is their cutter heads, often equipped with diamond or tungsten carbide tips that resist wear and tear far longer than their predecessors. This not only extends the life of the tools but also reduces downtime and maintenance costs. Moreover, the hydraulic systems in TBMs allow for adaptive control, optimizing pressure and cutting angles for different rock densities, thus maximizing efficiency.
Precision Drilling with Raise Boring Machines (RBMs)
Raise boring machines (RBMs) furnish another effective solution for vertical and inclined shafts within tunnels. These machines are particularly designed to create large-diameter holes without the use of explosives, making them safer and more environmentally friendly. RBMs operate by rotating a boring head from beneath,
cutting upwards through rock with extreme precision.
tools for drilling through rock in tunnels, specifically designed ...
The innovation in RBM technology lies in adjustable reaming heads that cater to varying rock toughness and bore diameters. Advanced models feature computer-controlled guidance systems for precise alignment, ensuring that the tunnels meet exact specifications. As a result, RBMs have become an industry staple for tasks demanding high accuracy and minimal structural deviation.
Integrating Rock Fragmentation Technologies
Beyond conventional drilling, rock fragmentation technologies have emerged as complementary solutions. Technologies such as hydraulic fracturing and high-frequency acoustic devices offer methods to pre-crack rock formations, significantly decreasing drilling resistance. These approaches increase drilling efficiency and extend the life of mechanical components by reducing wear stress.
Hydraulic fracturing, for instance, involves the injection of high-pressure fluid to create fractures in the rock, making it more susceptible to penetration by cutting tools. Its application in tunneling is gaining traction owing to its effectiveness in lowering operational costs and its ability to function within environmentally stringent regulations.
Quality Assurance in Rock Drilling
Quality control is pivotal to ensure the reliability and safety of rock drilling tools. Manufacturers engage in rigorous testing and certification processes to validate their equipment's performance under varied geological conditions. Material integrity tests, such as hardness and fatigue tests, ascertain that the tools can withstand the immense pressures encountered underground. Furthermore, regular maintenance protocols and real-time monitoring of tool conditions are fundamental practices to mitigate risk and optimize operational efficiency.
In the realm of tunnel construction, adopting tools and technologies that not only enhance the effectiveness of rock drilling but also ensure precision and safety is paramount. Companies leading the charge in this field are those that invest in innovation and uphold the highest standards of reliability and quality in their products.
Conclusion
The domain of tunnel rock drilling is witnessing unprecedented growth, powered by advanced technologies that blend expertise, precision, and environmental consciousness. Whether through sophisticated TBMs, efficient RBMs, or integrative rock fragmentation techniques, the future of tunnel construction is bright with innovations that promise to reshape the geological landscape with unprecedented efficacy and safety. These tools are the bedrock upon which the infrastructure of tomorrow will be built, driving progress in a sustainable and robust manner.