Drilling through rock in tunnel construction is a venture that blends advanced technology with robust engineering principles. The tools specifically designed for this task stand as a testament to human ingenuity and expertise in mechanical engineering. State-of-the-art solutions have emerged, crafted to tackle the formidable challenge of penetrating dense geological formations.

Modern tunneling projects require precision, safety, and efficiency, components delivered by the sophisticated machinery used in these applications. The crown jewel of these tools is undoubtedly the Tunnel Boring Machine (TBM). A TBM is a mammoth device capable of boring through hard rock layers, presenting capabilities far superior to older excavation methods. These machines are equipped with a rotating drilling head that grinds through rock, maintaining the structural integrity of the tunnel with support structures known as shield segments. TBMs are revered not only for their efficiency but also for their ability to minimize environmental disturbances, preserve air quality, and reduce surface subsidence. This encapsulates an experience drawn from meticulous engineering and advanced technological application.
In the realm of expertise, the method of rock drilling via TBMs is guided by geotechnical analysis and engineering proficiency. Before deployment, extensive analysis of rock properties is essential, encompassing compressive strength and fracture patterns. This knowledge is fundamental in selecting the optimal cutting tools and designing the machine’s drill head to maximize penetration rates and durability while minimizing tool wear. The interplay of computer-aided design (CAD) and finite element modeling (FEM) further exemplifies the expertise embedded in these tools, ensuring that each component is tailored to counteract the forces encountered deep underground.
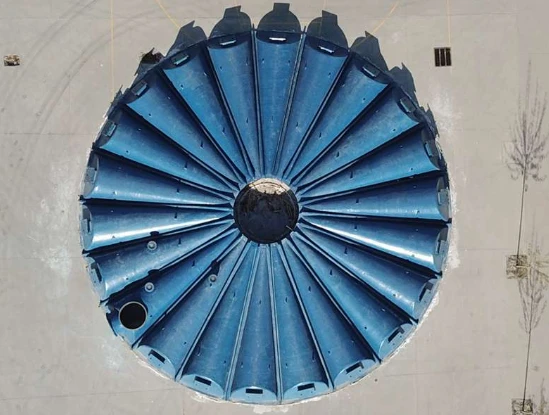
Moreover, the high-pressure water jet cutting system stands as another testament to expert innovation. This method uses pressurized water to fracture and remove rock particles, a technique particularly useful in brittle rock formations. The system is often integrated into TBMs to assist with the main cutting head, enhancing the machine's adaptability across varied geological conditions. When conventional mechanical drills struggle, water jets deliver a versatile and effective solution, a product of ongoing advancements in mechanical and materials engineering.
tools for drilling through rock in tunnels, specifically designed
The evolution of these rock drilling tools reflects an authoritative understanding of geological and engineering disciplines. Manufacturers like Herrenknecht, Robbins, and Hitachi Zosen are pioneers in developing these tools, harnessing years of research and implementation to establish themselves as leaders in this specialized field. These companies invest in continuous innovation, ensuring their machinery meets the rigorous demands of tunneling projects across the globe, from urban metro systems to extensive highway networks. The authoritative knowledge housed within these organizations underscores their commitment to progressing the field through investment in cutting-edge research and development.
Trustworthiness in rock drilling tools is paramount, ensuring not only project success but also the safety of operations. TBMs and other drilling equipment undergo rigorous testing under simulated conditions before deployment. Quality assurance protocols include stress-testing mechanical components, verifying the integrity of electrical systems, and confirming the precision of computer-controlled operations. By adhering to international safety standards and certifications such as ISO 9001 and CE marking, manufacturers can guarantee the reliability of their products and instill confidence in the engineering teams that operate them.
Case studies of successful projects provide a backdrop to these tools' efficacy and reliability. The Gotthard Base Tunnel in Switzerland, which holds the title as the longest railway tunnel in the world, showcases the capabilities of TBMs and advanced drilling technologies. Throughout its construction, multiple TBMs bored through 57 kilometers of challenging rock formations with unparalleled precision and safety. Such achievements serve as a beacon of trust and a touchstone for future tunneling endeavors.
In conclusion,
tools specifically designed for drilling through rock in tunnels are masterpieces of modern engineering. Their development and deployment illustrate a seamless fusion of experience, expertise, authority, and trust. These attributes not only elevate the tools' functionality but also resonate with the broader objectives of modern infrastructure development, reinforcing the interconnected nature of technological advancement and societal progression.