Fiberglass, a versatile and durable material, is increasingly finding its niche in the realm of steel smelting plants. Its application spans over various crucial areas, offering a unique set of advantages that enhance efficiency, safety, and sustainability within these industrial environments. This article delves into its multifaceted roles and the enduring benefits it brings, highlighting why fiberglass is essential for steel smelting operations.
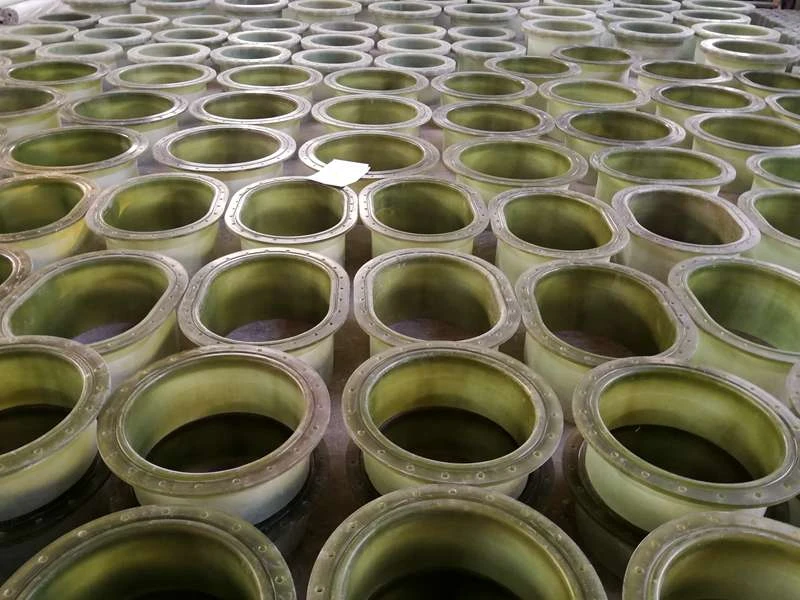
The integration of fiberglass in steel smelting plants primarily addresses the insulation needs. Due to its non-conductive nature and ability to withstand high temperatures, fiberglass serves as an excellent insulator. In environments where extreme heat is a constant, such as smelting plants, maintaining temperature stability is pivotal. Fiberglass insulation ensures that heat loss is minimized, preserving energy and reducing operational costs. Its resistance to thermal degradation significantly prolongs the life of equipment, minimizing downtime and enhancing productivity.
In addition to its insulating properties, fiberglass exhibits exceptional resistance to corrosion—a frequent and costly issue in steel smelting facilities. These plants are often exposed to a variety of harsh chemicals and byproducts, which can rapidly deteriorate less resilient materials. Fiberglass's intrinsic chemical resistance makes it an ideal material for constructing components like ducts, tanks, and linings, which are regularly in contact with corrosive substances. The longevity of fiberglass in such applications not only decreases replacement costs but also enhances the overall safety of the plant.
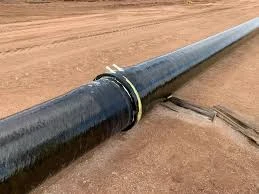
Another critical advantage of fiberglass is its lightweight nature compared to traditional materials like metal or concrete. This characteristic simplifies installation and reduces the load on supporting structures. For steel smelting plants, where large-scale constructions and equipment are the norms, the adoption of fiberglass can lead to significant reductions in construction time and labor costs. Moreover, its ease of transportation and adaptability in various forms allow for customizable solutions tailored to specific plant layouts and requirements.
fiberglass for steel smelting plant.
Beyond its physical properties, fiberglass also contributes to enhanced environmental sustainability in steel smelting operations. Its insulation capabilities result in improved energy efficiency, aligning with the global industrial shift towards greener practices. Furthermore, fiberglass is composed of abundant raw materials, and innovations in its manufacturing process have made it increasingly recyclable. By incorporating fiberglass, smelting plants can reduce their carbon footprint and adhere to stricter environmental regulations.
The safety aspect is another critical facet where fiberglass's benefits come to the fore. Unlike metals, fiberglass is non-flammable, which is a considerable advantage in high-temperature environments where sparks and heat can easily ignite fires. Its fire-retardant properties help in mitigating risks, protecting both the workforce and the infrastructure. Additionally, since fiberglass does not conduct electricity, it reduces the risk of electrical hazards, further ensuring the safety of personnel operating within these facilities.
From an economic perspective, the initial costs associated with fiberglass might be higher than some conventional materials. However, the long-term cost efficiency it provides through durability, reduced maintenance, and energy savings outweighs the initial investment. Incorporating fiberglass into infrastructure intensifies its market value and operational appeal, making it a prudent investment for forward-thinking businesses in the steel industry.
Overall, the use of fiberglass in steel smelting plants exemplifies a confluence of durability, safety, economic sense, and environmental responsibility. As this industry continues to confront challenges related to efficiency, sustainability, and safety, materials like fiberglass will be at the forefront of innovations that drive future transformation. Its versatile applications demonstrate an exemplary balance between modern industrial demands and ecological mindfulness, ensuring it remains indispensable to the infrastructure of steel smelting plants now and in the future.