The advent of FRP (Fiber Reinforced Plastic) pipes has revolutionized the material handling landscape within various industries, offering an unparalleled blend of durability, cost-efficiency, and versatility. As a material that has steadily secured its place as a preferred solution, understanding the dynamics and advantages of FRP piping systems is crucial for businesses aiming to optimize their infrastructural integrity and longevity.
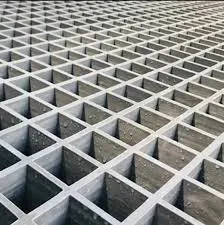
Experienced engineers and industry experts vouch for the effectiveness of FRP pipes in corrosive environments. Unlike traditional materials such as steel or iron, FRP pipes do not succumb to rust, making them ideal for transporting corrosive chemicals and fluids over extended periods. Industries that deal with high levels of acidity or alkalinity find FRP pipes to be indispensable, as conventional pipes require frequent maintenance and replacement, which can be both costly and time-consuming.
From an expertise standpoint, FRP pipes boast an impressive strength-to-weight ratio. This is particularly notable in applications requiring significant mechanical endurance without the burden of excessive weight. Engineers appreciate the ease of installation and handling associated with FRP pipes. Their lightweight nature reduces manpower and machinery requirements, directly translating into lower installation costs and faster project turnaround times—a crucial factor in large-scale industrial projects.
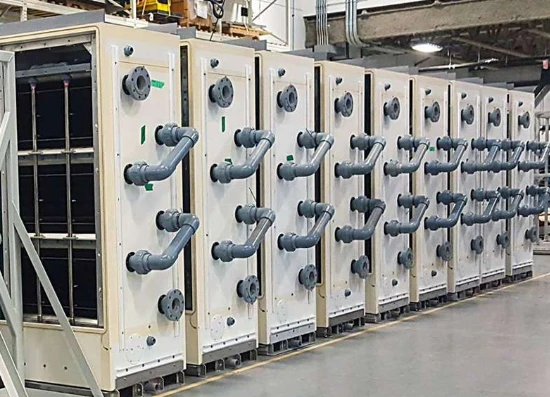
Authoritative industry analyses reveal that the long-term cost benefits of switching to FRP piping systems are substantial. While the initial investment might appear marginally higher compared to more traditional alternatives, the extended service life and minimal maintenance demands of FRP pipes ensure a favorable return on investment. This longevity is supported by numerous case studies wherein facilities have reported intact functioning of FRP systems for decades without significant degradation.
frp pipe
Trustworthiness in FRP pipe systems also comes from their customized composition and manufacturing process. Unlike homogeneous materials, FRP pipes can be tailor-made to meet specific industry requirements. The adaptability in resin selection, fiber orientation, and wall thickness enables engineers to design piping systems that address nuanced operational conditions, ensuring resilience and efficiency. This customization is not only a testament to the material’s versatility but also speaks volumes about its reliability in specialized applications.
Moreover, parts of industries focusing on sustainability and environmental impact have highlighted the eco-friendly nature of FRP pipes. Their long lifespan and reduced need for replacements contribute to waste minimization. The manufacturing process of FRP also generally involves fewer ecological footprints compared to more energy-intensive processes associated with metals.
In terms of application, FRP pipes have become a mainstay in sectors like oil and gas, wastewater treatment, and power plants. In each of these areas, the need for robust, corrosion-resistant, and durable pipelines cannot be overstated. The ongoing evolution of composite materials technology continuously enhances the efficacy of FRP, keeping it at the forefront of industrial material innovations.
The collective experience and expert consensus around FRP pipes build a compelling narrative for their continued use and development. They address a frequent industry pain point—balancing performance with economic feasibility. As more businesses pivot towards efficient, sustainable infrastructure solutions, FRP piping systems provide a tested and trusted option, underscoring their position as a cornerstone of modern industrial plumbing solutions.