Inserting rock bits is a crucial task in the realm of drilling, especially within industries such as oil and gas, mining, and construction.
Having effective techniques and strategies for this process is paramount to enhancing operational efficiency, reducing costs, and maintaining safety standards. This article delves into some of the most advanced strategies that industry professionals use to optimize the performance of rock bits.
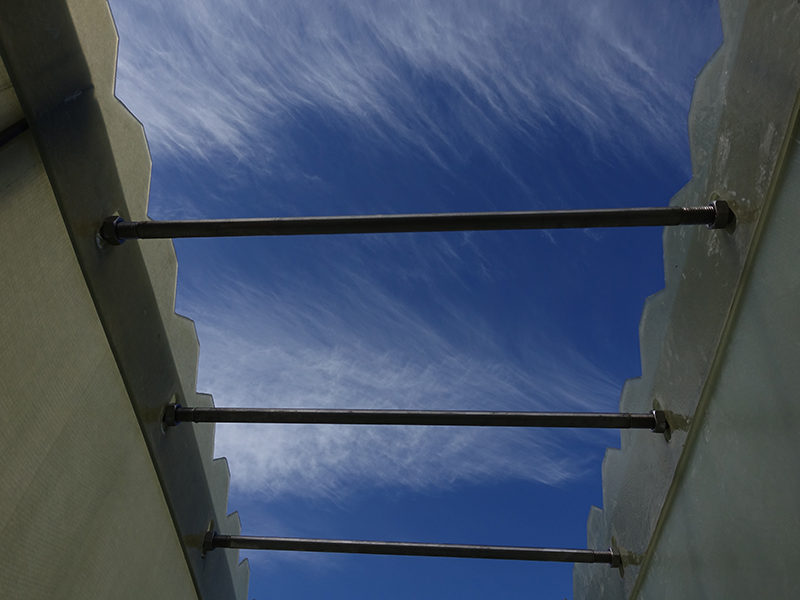
One of the primary techniques in achieving efficient rock bit insertion is selecting the appropriate bit type for the specific geological formation. Various formations require different bits; for instance, softer formations may benefit from milled-tooth bits, while more demanding, harder formations might necessitate the use of polycrystalline diamond compact (PDC) bits. Expertise in selecting the correct bit not only boosts drilling efficiency but also extends the lifespan of the equipment.
Experience dictates that proper preparation and planning significantly impact the insertion process. Implementing a comprehensive pre-drilling plan that includes a detailed analysis of the geological survey can forecast potential issues and customize solutions. Precision in planning translates to minimized downtime and reduced trial-and-error during operations.
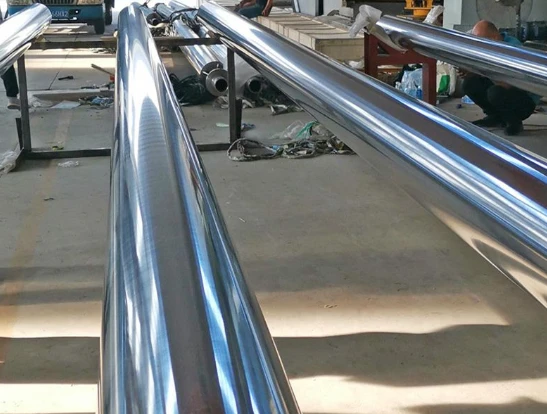
Maximizing the performance of rock bits also requires a thorough understanding of bit hydraulics. Ensuring optimal hydraulic parameters—such as mud flow rate and pressure—facilitates efficient cutting removal and cooling, extending bit life and minimizing wear. Advanced simulation tools provide insights into hydraulic behaviors, empowering engineers to make data-driven adjustments before any physical operation commences.
Authoritative drilling teams leverage technological advancements to drive efficiency further. Innovations such as real-time data monitoring systems provide engineers with continuous feedback on the bit's performance, allowing for immediate adjustments and reducing the risk of costly mistakes. This proactive approach enhances trustworthiness in the process by safeguarding equipment and personnel involved.
inserting rock bits techniques and strategies for efficient ...
Moreover, the integration of automation in the drilling process cannot be overlooked. Automated systems are carving out a new era for rock bit insertion by ensuring consistent and precise operational parameters which human intervention might sometimes jeopardize. These systems apply preset configurations for various drilling scenarios, thereby maintaining optimal bit performance and efficiency.
Trustworthiness in operations is bolstered by regularly scheduled maintenance and inspection of rock bits. Experienced professionals advocate for rigorous maintenance protocols, ensuring that bits are in peak condition before insertion. This practice involves checking for damage or wear, which could otherwise compromise drilling efficiency and safety.
Utilizing training programs that marry theoretical knowledge with practical experience provides technicians with the skill set needed to manage the nuances of bit insertion. Seasoned experts imparting this knowledge can instill a culture of excellence and innovation, leading to a continuously improving drilling operation landscape.
Strategic partnerships with suppliers also serve as a cornerstone in cultivating expertise. Collaboration with manufacturers facilitates the acquisition of the latest technologies and cutting-edge rock bit designs tailored to specific drilling needs. The shared knowledge fosters an environment where both parties can innovate and push the boundaries of current limitations.
In conclusion, effective rock bit insertion is not a one-size-fits-all process but a symphony of careful planning, precision engineering, and continuous learning. By aligning experience, expertise, authoritativeness, and trustworthiness, industries can achieve remarkable efficiencies, reduced costs, and significantly mitigate risks. As technology and methods advance, staying agile and open to change remains essential in maintaining a competitive edge and ensuring sustainability in drilling operations.