Molded fiberglass grating has become a cornerstone in modern industrial design, offering a unique blend of durability, versatility, and resilience. Understanding the extensive applications and benefits of molded fiberglass grating is crucial for industries looking to optimize long-term performance and safety.
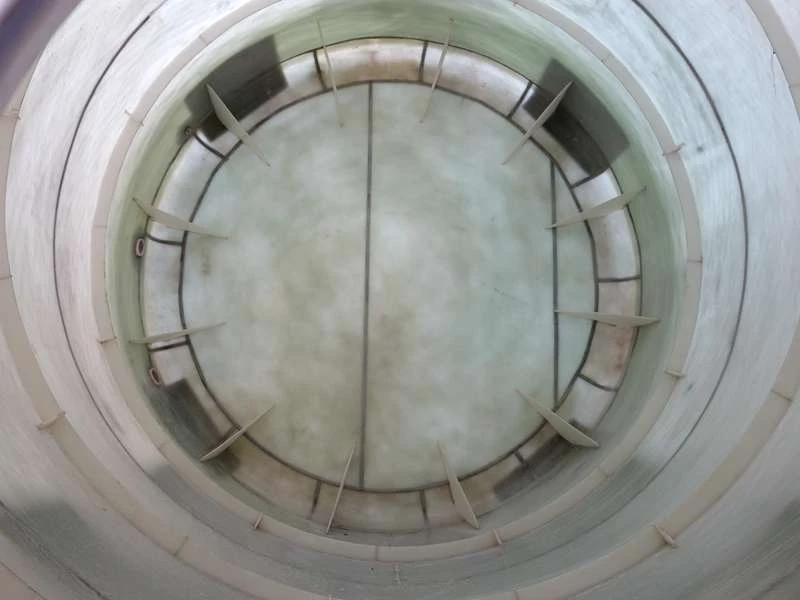
At its core, molded fiberglass grating is a composite material crafted mostly from glass fibers and resin. This combination results in a product that is significantly less dense than metals, making it lightweight yet exceptionally strong. This strength-to-weight ratio is one of the key elements that distinguish molded fiberglass grating from traditional materials like steel or aluminum.
One of the most significant advantages of molded fiberglass grating is its exceptional resistance to corrosive environments. In industries where chemical exposure is frequent, such as in chemical processing plants, wastewater treatment facilities, and marine settings, this resistance ensures longevity and reduces maintenance costs. Fiberglass grating does not rust or corrode, unlike metals that degrade over time when exposed to harsh chemicals or saline environments.
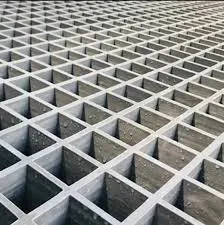
Moreover, the safety benefits of using molded fiberglass grating cannot be overstated. The non-slip surface of the grating, created through its inherent design and texture, significantly reduces the risk of accidents in wet or oily environments, making it an ideal choice for flooring, walkways, and platforms. Furthermore, fiberglass grating is non-conductive, providing an added layer of safety in electrical applications, where the risk of conducting electric currents can pose a serious hazard.
Another noteworthy attribute of molded fiberglass grating is its ease of installation. The lightweight nature of fiberglass makes it much easier to handle and install than metal alternatives, which often require heavy equipment and extensive labor. This ease of installation translates to lower labor costs and faster project completion times, an attractive offering for project managers and contractors.
molded fiberglass grating
In terms of industry application, molded fiberglass grating is versatile. In the construction industry, it serves as a reliable component for roof walkways and scaffolding. In the transportation sector, it’s used in rail platforms and airport maintenance areas. In addition, in the food and beverage industry, it provides a hygienic, durable surface that withstands high-pressure cleaning and harsh chemical sanitization.
Despite its lightweight and easy-to-install nature, molded fiberglass grating does not compromise on strength. It offers a load-bearing capacity that rivals traditional materials, making it suitable for applications that involve substantial weight loads, such as heavy machinery platforms or storage areas in warehouses.
Environmental impact is another arena where molded fiberglass grating excels. Unlike materials prone to rust and breakdown, leading to frequent replacements and increased waste, fiberglass has a long lifecycle. This durability minimizes the frequency of replacement, thus reducing landfill contributions and resource consumption. Additionally, fiberglass grating can be made with resins that are non-toxic and environmentally friendly, bolstering its appeal in eco-conscious projects.
From a cost perspective, while the initial investment for molded fiberglass grating may be higher than traditional materials, its long-term savings, due to reduced maintenance and replacement costs, make it an economically sound choice. Companies looking to invest in sustainable, cost-effective infrastructure will find molded fiberglass grating a wise long-term investment.
Equipped with these benefits, choosing molded fiberglass grating for industrial applications becomes an exercise in foresight and efficiency. Businesses across sectors are discovering the transformative impact of this versatile material. As industries continue to prioritize safety, durability, and sustainability, the demand for molded fiberglass grating is expected to rise, reaffirming its position as a vital component in industrial design and engineering.