The world of tunnel construction presents unique challenges that demand specialized tools designed to effectively drill through formidable rock formations. Today, advancements in technology have ushered in new tools specifically designed for this arduous task, meeting the needs of the construction industry with greater efficiency and precision than ever before. This article delves into the intricacies of these tools, highlighting their design, application, and impact on the tunnel construction industry.
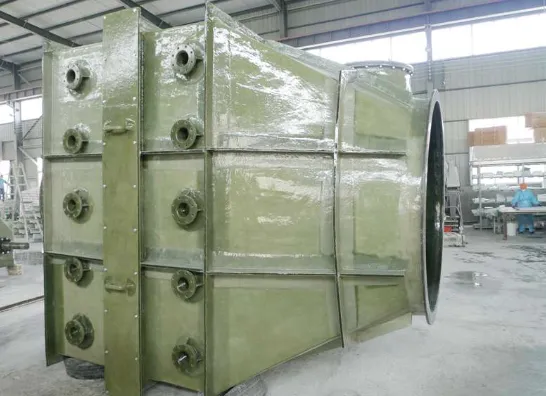
One of the most crucial components in drilling through rock in tunnels is the Tunnel Boring Machine (TBM). Known for its efficiency and precision, the TBM is a sophisticated piece of machinery that revolutionizes how tunnels are drilled. The TBM is equipped with a rotating cutting wheel supported by a durable shield which methodically excavates the tunnel while simultaneously supporting the surrounding rock structure. This dual functionality minimizes risks associated with structural failures, ensuring that large-scale tunnel projects remain on track.
Though TBMs are a centerpiece, they are complemented by a variety of other specialized tools. For example, roadheaders play a vital role, especially in projects where flexibility is needed. Roadheaders are versatile machines equipped with a powerful rotating cutting head that allows them to adapt to varying rock hardness levels, making them particularly effective in mixed rock conditions. Their precision cutting and maneuverability offer unique advantages in complex geological structures where adaptable solutions are necessary.
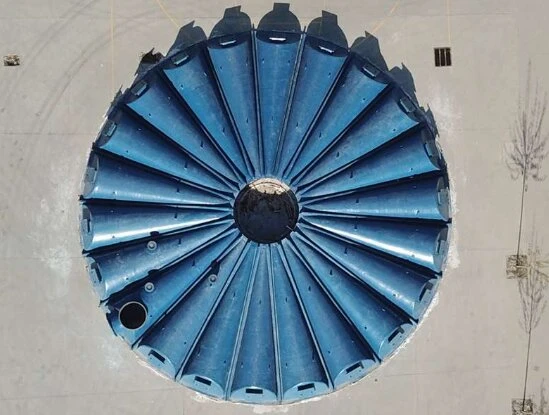
Understanding the nature and composition of the rock through which a tunnel will pass is essential. Geotechnical analysis informs the choice of tools, allowing engineers to select the optimal configuration for drill bits and cutting heads. Polycrystalline diamond compact (PDC) cutters are often used for their durability and ability to maintain cutting efficiency over prolonged use. PDC cutters effectively handle tough crystalline rock formations, providing consistent performance and extending the operational life of the cutting tools.
Additionally, down-the-hole (DTH) drilling systems are crucial in drilling through rugged rock layers. These systems use a pneumatic hammer-like action that delivers focused energy directly to the rock face, breaking it down efficiently. This precise application of energy minimizes the wear and tear on machinery, reducing operational costs and enhancing the longevity of the equipment.
tools for drilling through rock in tunnels, specifically designed
The role of robotics and automation in modern rock drilling cannot be understated. Automated drilling systems offer precision and control, reducing human error and enhancing safety. Tunneling rigs equipped with advanced sensors and AI-driven controls can adapt to changing rock conditions in real-time, optimizing the drilling process and ensuring maximum efficiency.
Guiding the successful use of these advanced tools is a team of specialists who possess both the expertise and experience necessary to tackle the complexities of tunnel construction. These professionals draw on years of hands-on knowledge, ensuring that each piece of equipment is used to its fullest potential. Their understanding of rock mechanics, coupled with machine handling expertise, guarantees a seamless integration of machinery and manpower, fostering an environment where advanced technological solutions meet human ingenuity.
One must also consider the environmental impact and sustainability when using these tools. Advances in drill bit technology and the reduction of noise and vibrations have made significant strides in making tunnel construction more eco-friendly. Tool designs that maximize drilling efficiency while minimizing energy consumption are becoming a focal point, signaling the industry’s commitment to sustainable practices.
In conclusion, the development and application of tools specifically designed for drilling through rock in tunnels represent a blend of cutting-edge technology and engineering expertise. By continually refining these tools and techniques, the industry not only improves its ability to undertake complex tunneling projects but also fosters a culture of innovation and responsibility. The ongoing evolution of these specialized tools stands as a testament to the industry’s capacity to meet modern engineering challenges with creativity and diligence, paving the way for future advancements in tunnel construction.