The Evolution of the Mining Extension Drill Rod
In the vast expanse of mining technology, one tool stands out for its indispensable role in extracting valuable resources from the earth's crust - the mining extension drill rod. This unassuming yet crucial component has undergone a remarkable evolution over the years, reflecting advancements in materials science and engineering.
At its core, the mining extension drill rod is a long, slender shaft designed to fit into a drill bit, extending its reach deep into mineral-rich deposits. Its primary function is to transmit rotational force from the surface to the drill bit, enabling it to bore through rock formations with precision and efficiency. However, this simple description belies the complexity and innovation that have gone into the development of modern drill rods.
Early iterations of the drill rod were made from steel, which provided adequate strength but was prone to corrosion and fatigue under the intense pressures and temperatures encountered during drilling operations. As mining ventures pushed deeper into the earth, demanding more robust and reliable equipment, material scientists turned their attention to enhancing the durability of these essential tools.
The advent of high-strength, low-alloy (HSLA) steels brought about a significant leap in performance. These alloys offered improved resistance to corrosion, higher yield strength, and better toughness, allowing drill rods to withstand the rigors of deep drilling without failing. Furthermore, heat treatment processes were refined to give the steel additional hardness while retaining its flexibility, ensuring that the rods could bend without breaking as they navigated through twists and turns in the mine shaft.
In parallel with material improvements, design optimization played a critical role in enhancing drill rod performance
In parallel with material improvements, design optimization played a critical role in enhancing drill rod performance
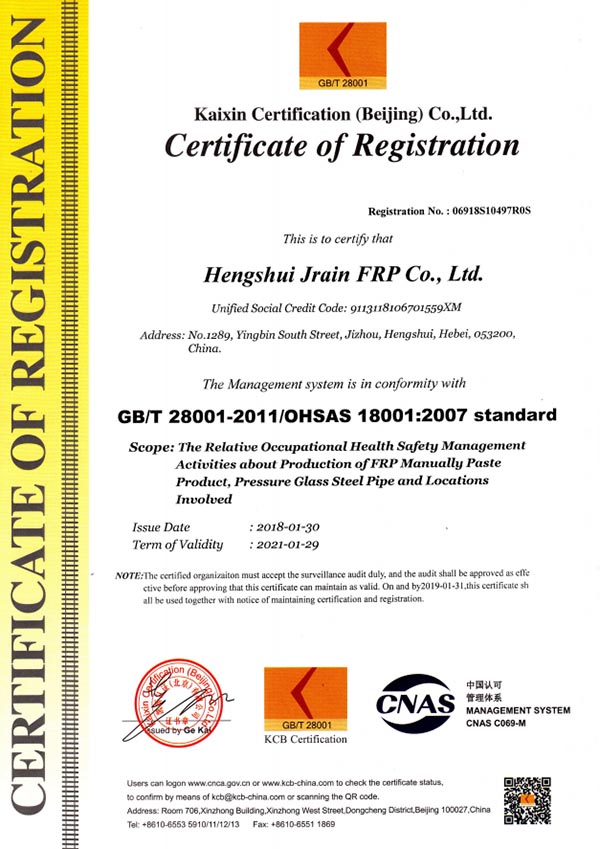
In parallel with material improvements, design optimization played a critical role in enhancing drill rod performance
In parallel with material improvements, design optimization played a critical role in enhancing drill rod performance
mine extension drill rod. The introduction of tapered threads reduced stress concentrations at thread connections, minimizing the risk of fractures. Additionally, the implementation of advanced coatings such as titanium carbonitride (TiCN) provided an extra layer of protection against abrasion and wear, extending the service life of the rods significantly.
Today, mining extension drill rods are not only stronger and more durable than ever before; they are also smarter. Some models are equipped with sensors that relay data on temperature, pressure, and vibration back to the surface. This real-time information allows operators to adjust drilling parameters on the fly, optimizing efficiency and reducing the likelihood of equipment failure.
As we look towards the future, the mining extension drill rod is set to continue evolving alongside technological breakthroughs. Materials such as carbon fiber composites may offer even lighter, stronger alternatives to traditional steel construction, while advancements in robotics could see autonomous drilling systems taking over some of the most dangerous and labor-intensive tasks in mining.
In conclusion, the humble mining extension drill rod embodies the spirit of innovation and progress that defines the mining industry. From its earliest forms to the sophisticated tools of today, it remains a testament to human ingenuity and our relentless pursuit of resources hidden beneath the earth's surface.